Thermosetting compression moulding is a versatile and widely used manufacturing process that plays a pivotal role in creating a multitude of products across various industries. This article aims to provide an in-depth understanding of thermosetting compression moulding, its principles, applications, advantages, and challenges.
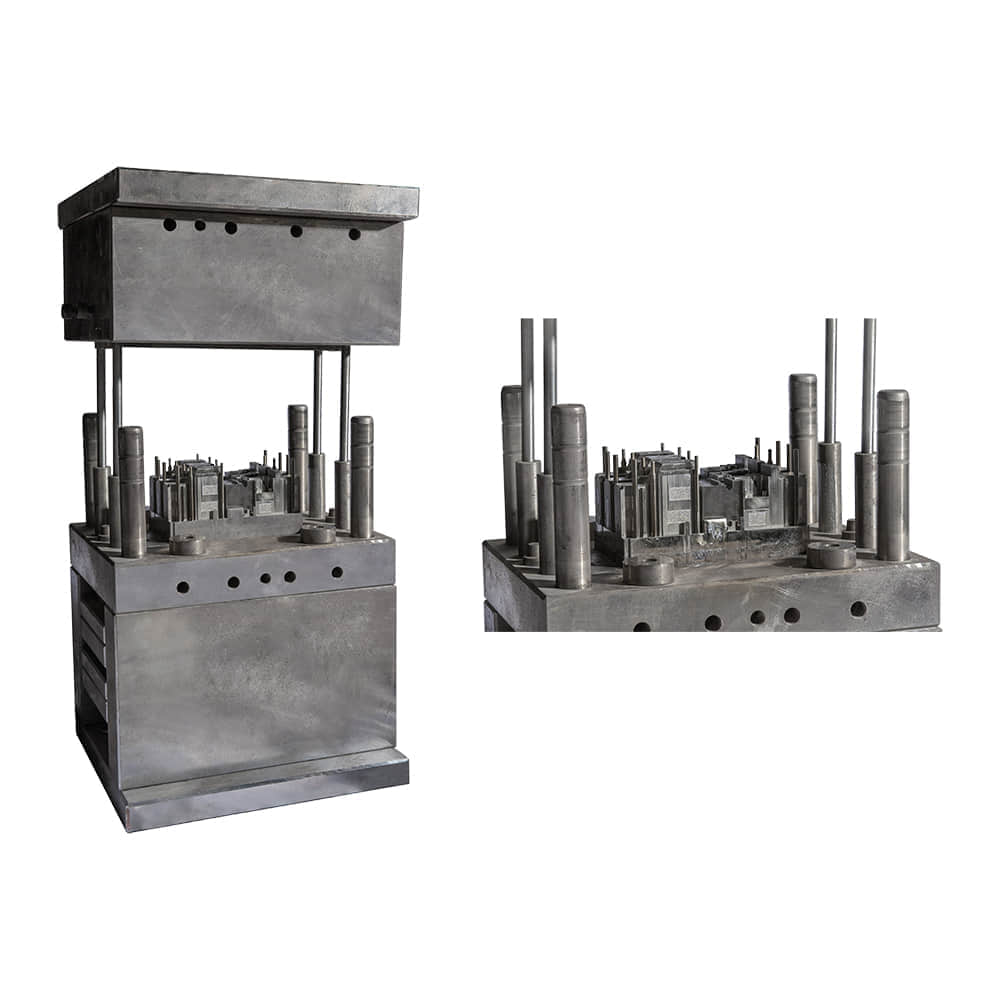
Principles of Thermosetting Compression Moulding
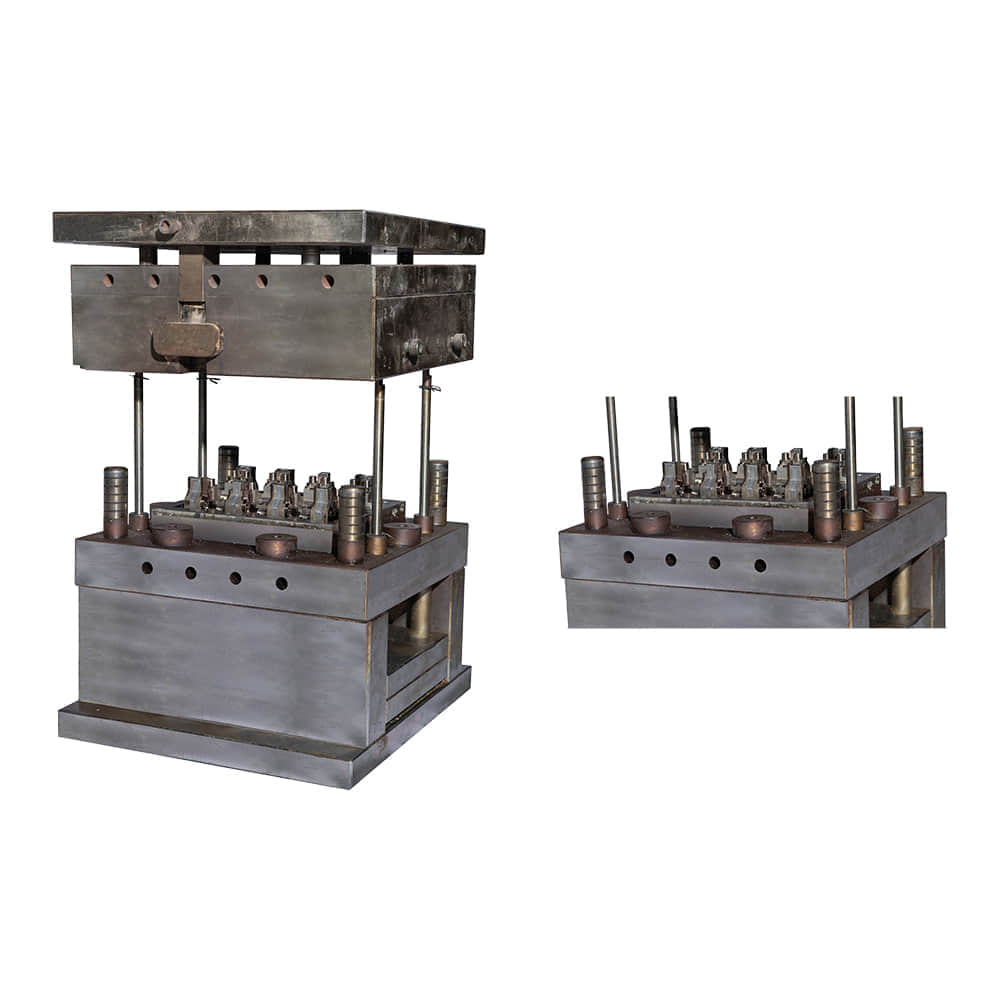
Thermosetting compression moulding is a manufacturing technique primarily employed for shaping thermosetting plastics into desired forms. Unlike thermoplastics, which can be melted and re-moulded, thermosetting plastics undergo a chemical transformation during the moulding process, irreversibly hardening and becoming rigid. The key principles of this process involve the following steps: Material Preparation: The process begins with the preparation of thermosetting plastic material in the form of granules, pellets, or preforms. These materials typically include epoxy, phenolic, melamine, and silicone resins. Heating: The prepared material is placed in a mould cavity, and heat and pressure are applied simultaneously. The heat softens the thermosetting plastic, allowing it to flow and fill the mould cavity. Compression: A hydraulic press or mechanical press applies pressure to the mould, compacting the softened material into the desired shape. This compression helps to eliminate voids and air bubbles within the material. Curing: The moulded part is subjected to elevated temperatures for a specific period, allowing the thermosetting resin to cross-link and harden permanently. This curing process creates a durable and stable product. Cooling: After the curing phase, the moulded part is gradually cooled to room temperature, ensuring dimensional stability and preventing distortion. Applications of Thermosetting Compression Moulding Thermosetting compression moulding is employed across a wide range of industries due to its ability to produce high-strength, heat-resistant, and chemically stable components. Some common applications include: Automotive Parts: It is used to manufacture components like brake pads, clutch plates, and electrical insulators due to its excellent thermal and mechanical properties. Aerospace Components: Thermosetting compression moulding produces lightweight yet strong parts for aircraft, including interior panels, gaskets, and insulation materials. Electrical and Electronic Enclosures: The process is ideal for creating electrically insulating enclosures, switchgear components, and circuit breakers. Consumer Goods: Thermosetting compression moulding is used to produce kitchenware, electrical outlets, and appliance components. Construction Materials: It is employed to manufacture building materials such as laminates, decorative panels, and structural elements. Advantages of Thermosetting Compression Moulding This manufacturing process offers several advantages, making it a preferred choice for many applications: High Strength and Durability: Thermosetting plastics are known for their superior mechanical properties and resistance to heat and chemicals. Dimensional Stability: Parts produced through compression moulding maintain their shape and size even under extreme conditions. Cost-Effective: It allows for the efficient use of materials, reducing waste and minimizing production costs. Versatility: Thermosetting compression moulding can accommodate complex shapes and intricate designs. Challenges and Considerations While thermosetting compression moulding has numerous advantages, it also presents some challenges: Tooling Costs: Designing and fabricating moulds can be expensive, particularly for intricate or large parts. Cycle Time: The curing phase can extend the production cycle, making it less suitable for high-volume production. Material Selection: Choosing the right thermosetting resin for the application is critical, as different resins offer varying properties. In conclusion, thermosetting compression moulding is a valuable manufacturing process with widespread applications. Its ability to produce durable, high-strength components with excellent thermal and chemical resistance makes it indispensable in various industries. By understanding its principles, advantages, and challenges, manufacturers can harness the full potential of this versatile technique to create innovative and reliable products.
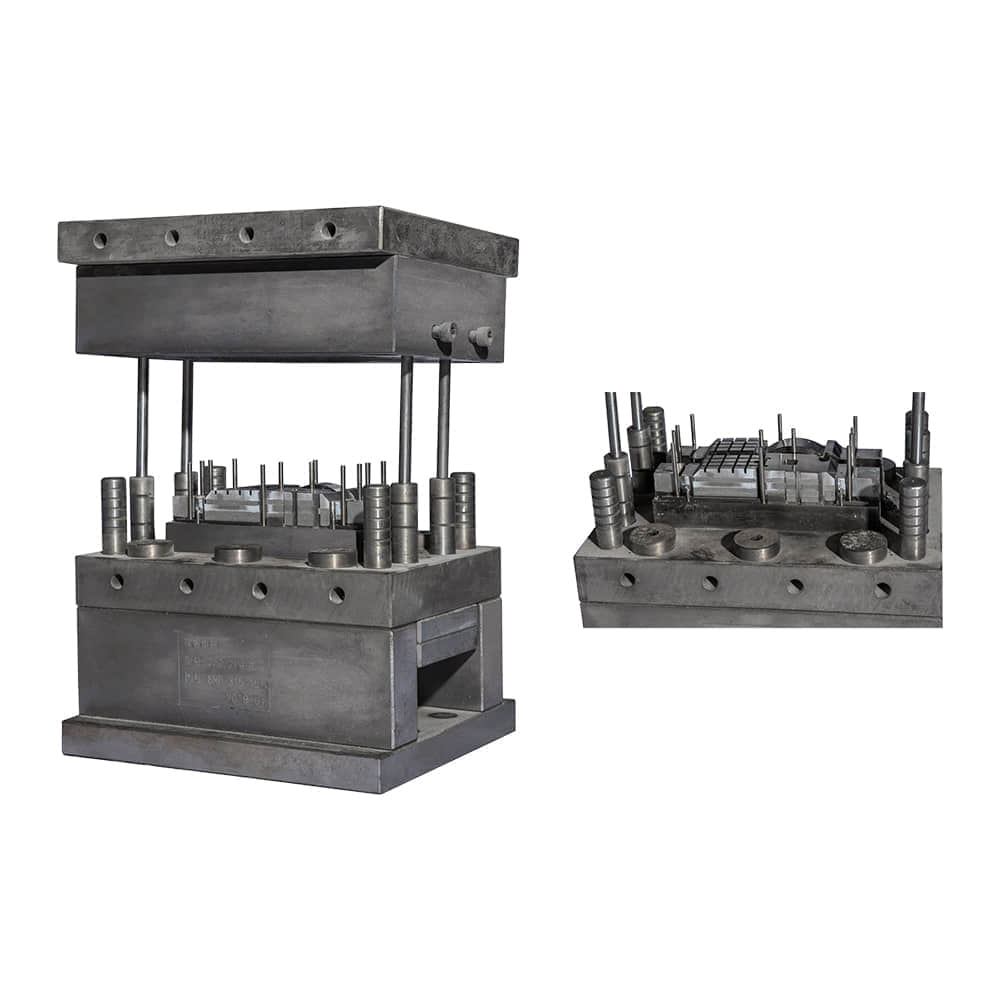