Thermosetting Compression Moulding: Crafting Durability and Precision
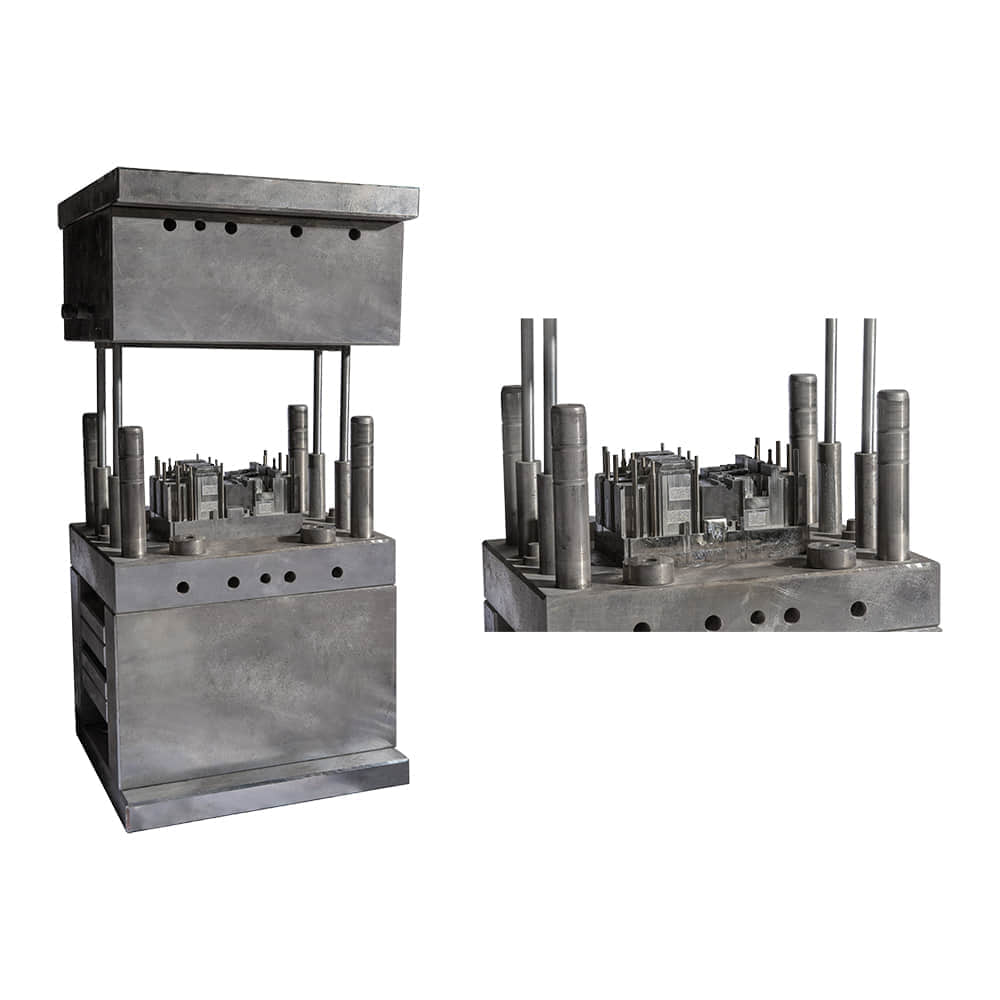
In the realm of manufacturing, where precision, strength, and durability are paramount, thermosetting compression molding emerges as a key player. This process, characterized by its ability to create robust and intricately detailed components, finds its applications in a wide range of industries, from automotive to aerospace. In this article, we will explore the nuances of thermosetting compression molding, its advantages, and its diverse applications.
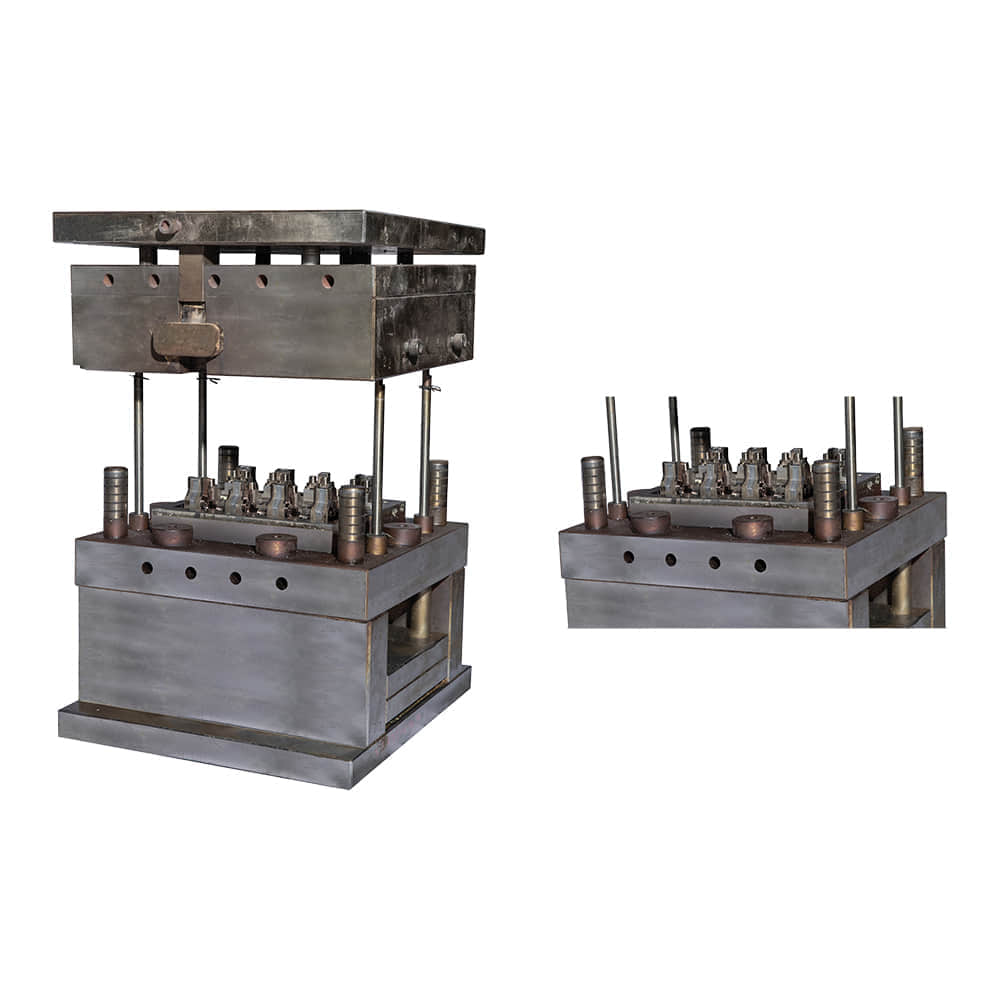
The Basics of Thermosetting Compression Molding Thermosetting compression molding is a manufacturing process that involves transforming raw materials into a solid, robust, and often intricate product. The fundamental idea behind this technique is the use of heat and pressure to cure a thermosetting resin within a mold. Unlike thermoplastic materials that can be re-melted and reformed, thermosetting materials undergo a chemical change during the molding process that renders them infusible and insoluble. This transformation results in exceptional heat resistance, dimensional stability, and mechanical strength. The Process The thermosetting compression molding process can be divided into several key steps: Material Preparation:The process begins with the preparation of the raw materials. This typically involves combining a thermosetting resin with other additives, such as fillers, reinforcements, and curing agents, to create a compound with the desired properties. Mold Preparation:A mold, usually made of metal, is prepared to shape the final product. The mold is carefully designed to accommodate the desired geometry and intricacies of the part to be produced. Loading:The prepared material is placed into the mold cavity. This can be done manually or with automated systems, depending on the complexity and scale of production. Compression:The mold is closed, and pressure is applied. The combination of heat and pressure triggers the curing process, causing the material to harden and take the shape of the mold. Curing:The material is allowed to cure for a specific duration, ensuring that the chemical reaction is complete. This step is critical in achieving the desired material properties. Demolding:After curing, the mold is opened, and the newly formed part is removed. The part may undergo additional finishing processes, such as trimming or machining, to meet precise specifications. Advantages of Thermosetting Compression Molding Thermosetting compression molding offers several advantages, making it a preferred choice in various industries: Strength and Durability:Thermosetting materials are known for their exceptional strength and durability, making them ideal for applications requiring resistance to high temperatures, chemicals, and mechanical stress. Precision and Detail:The process allows for intricate and precise parts to be manufactured with tight tolerances, making it suitable for components with complex geometries. Cost-Effective:Mass production of thermosetting components can be highly cost-effective due to shorter cycle times and minimal material waste. Customization:Manufacturers can tailor the material properties to meet specific application requirements by adjusting the resin formulation and additives. Applications Thermosetting compression molding finds applications across a spectrum of industries: Automotive:It is used to produce parts like brake pads, engine components, and interior trim pieces due to its heat resistance and durability. Aerospace:Components such as aircraft interiors, radomes, and structural elements benefit from the lightweight, strong properties of thermosetting materials. Electrical and Electronics:Insulating materials, circuit boards, and electrical connectors rely on thermosetting compression molding for their performance and reliability. Consumer Goods:Kitchenware, sporting goods, and appliance components are often manufactured using this process. Construction:Thermosetting molding contributes to the production of durable and weather-resistant construction materials. In conclusion, thermosetting compression molding is a versatile and vital manufacturing process that delivers precision, strength, and durability. Its wide-ranging applications continue to drive innovation and excellence in various industries, making it a cornerstone of modern manufacturing.
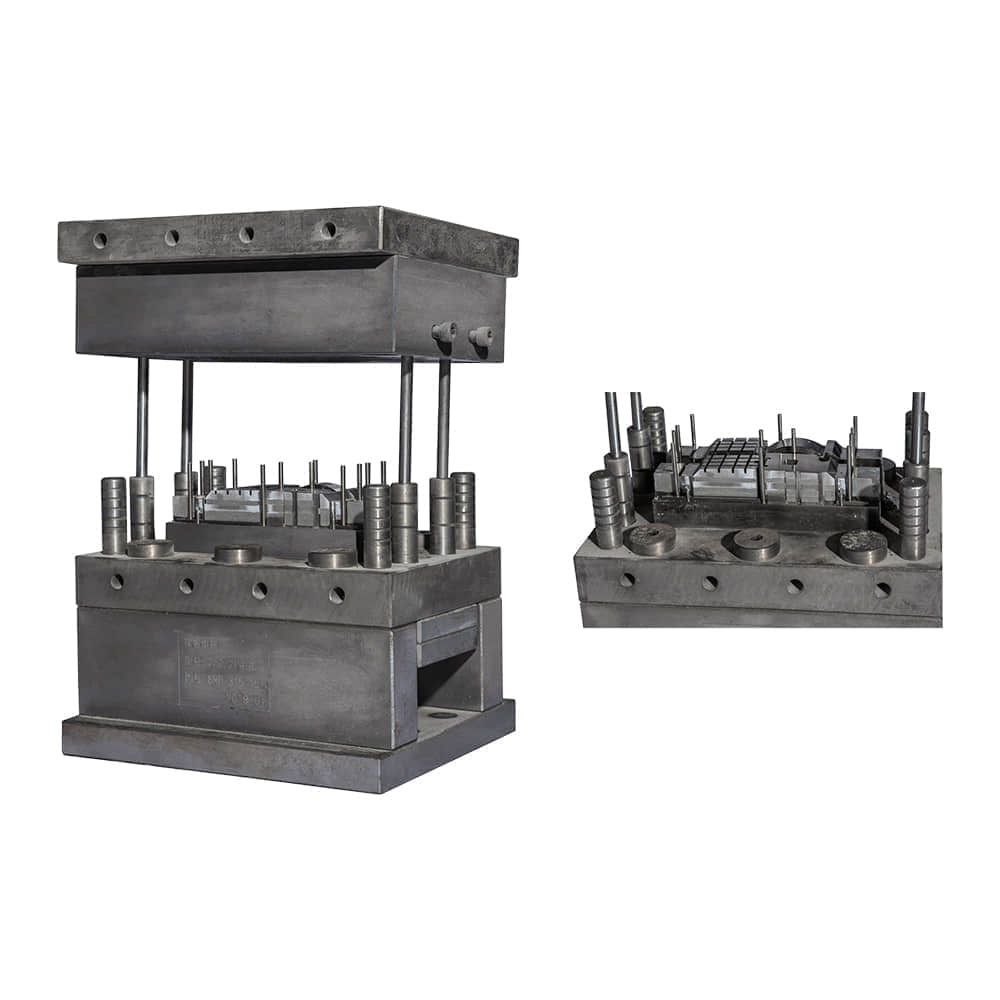