In the quest for sustainable energy solutions, hydrogen has emerged as a promising alternative to fossil fuels. Hydrogen energy offers numerous advantages, including its abundance, high energy density, and environmental benefits. However, for hydrogen energy systems to be effective and efficient, reliable control mechanisms are crucial. One such mechanism is the hydrogen energy pneumatic butterfly valve. This article explores the significance of pneumatic butterfly valves in hydrogen applications, their operational principles, advantages, and challenges.
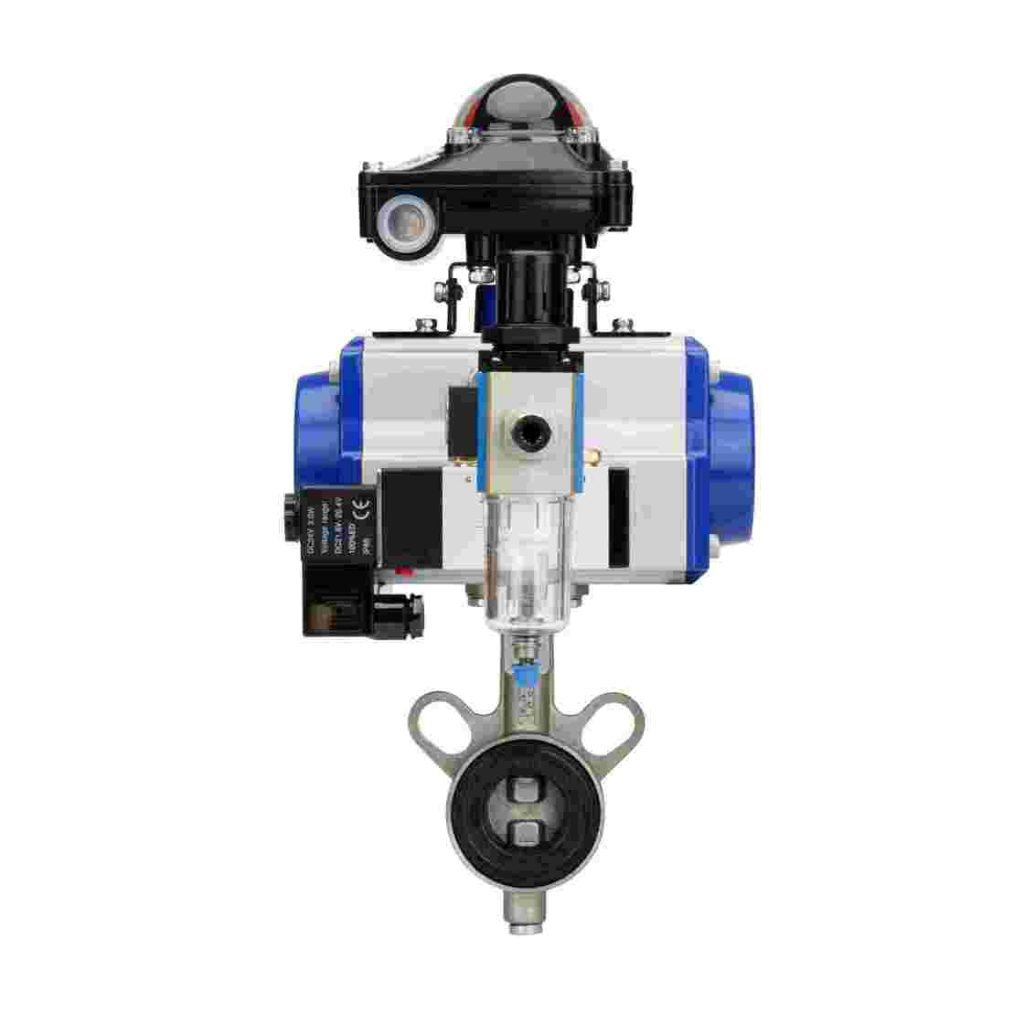
Understanding Pneumatic Butterfly Valves
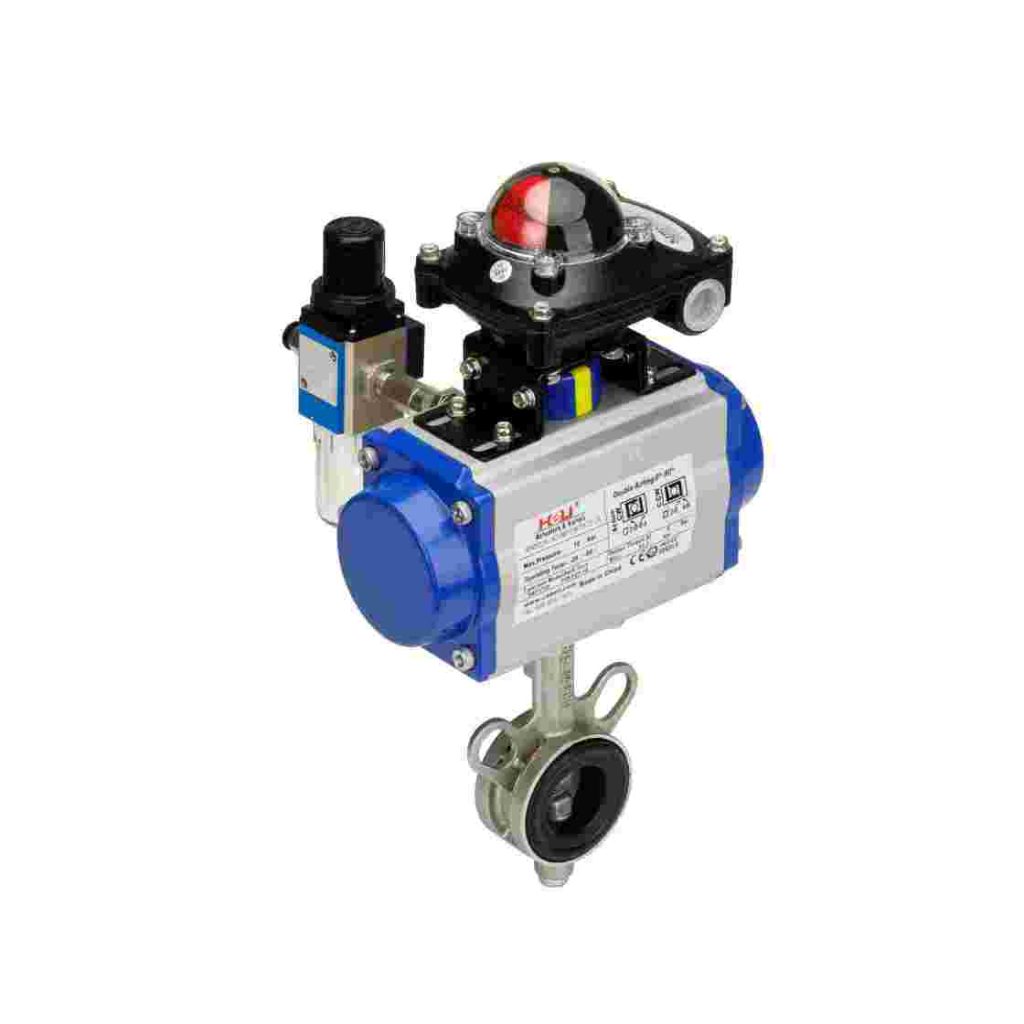
Pneumatic butterfly valves are quarter-turn valves that utilize a rotating disc to control the flow of fluids. In hydrogen energy systems, these valves regulate the flow and pressure of hydrogen gas within pipelines, storage tanks, and fuel cells. The valve’s design includes a disk that rotates within a pipe, opening or closing the flow path based on its position. When the disk is parallel to the flow, the valve is fully open, allowing maximum flow. Conversely, when the disk is perpendicular, the valve is closed, stopping the flow completely. These valves are actuated by pneumatic systems, which use compressed air to drive the valve’s opening and closing actions. Pneumatic actuation provides several advantages, including rapid response times, precise control, and minimal energy consumption compared to other actuation methods.
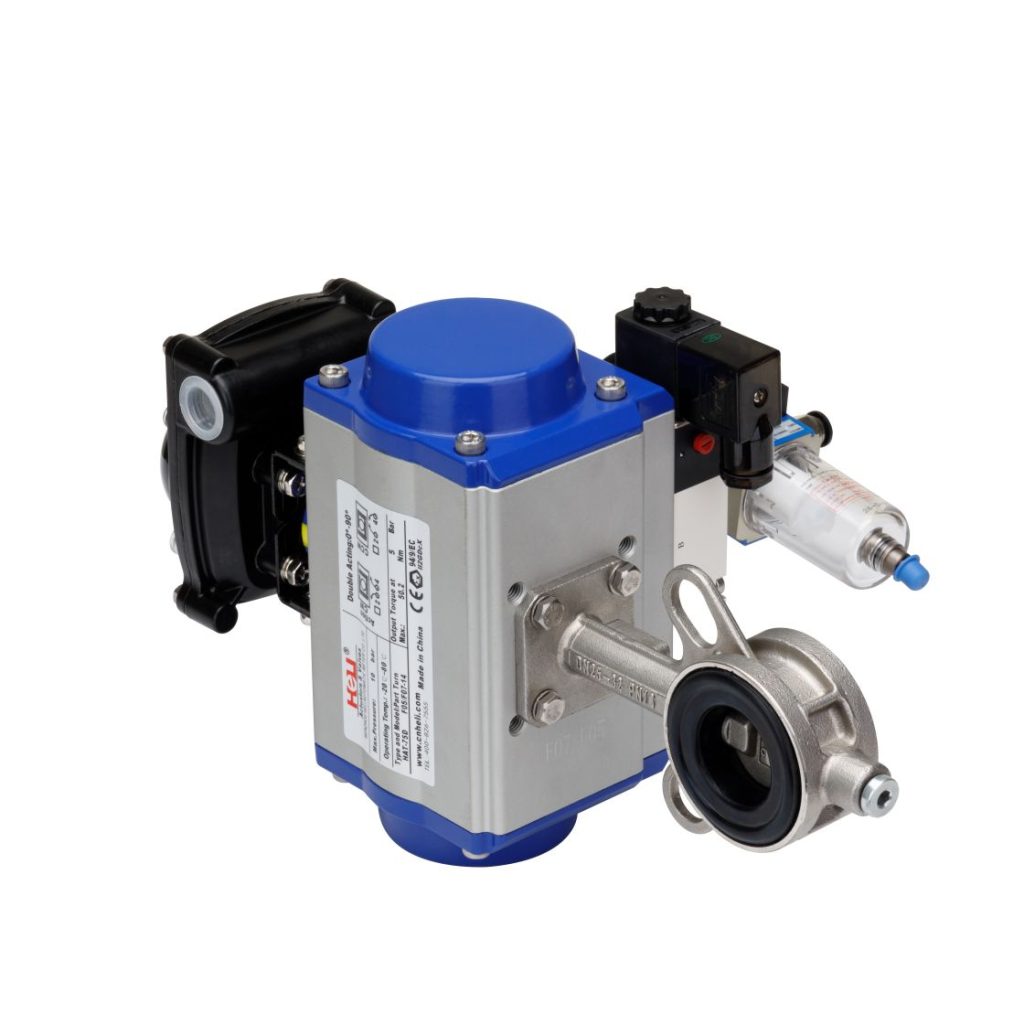