In today’s fast-paced world of manufacturing, precision and efficiency are paramount. One industry that plays a vital role in achieving these objectives is injection mold manufacturing. This article delves into the world of injection mold manufacturers, exploring their significance, processes, and the intricate craftsmanship that goes into creating these essential tools.
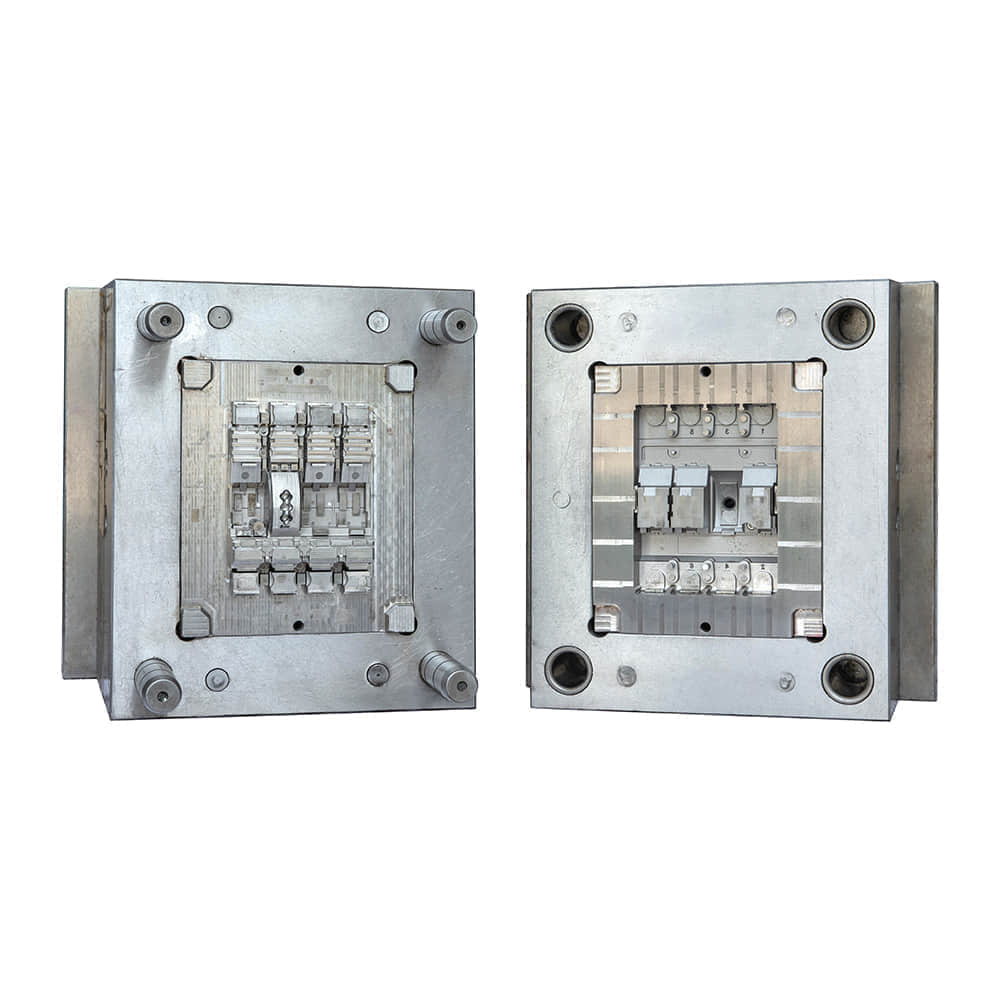
The Crucial Role of Injection Mold Manufacturers
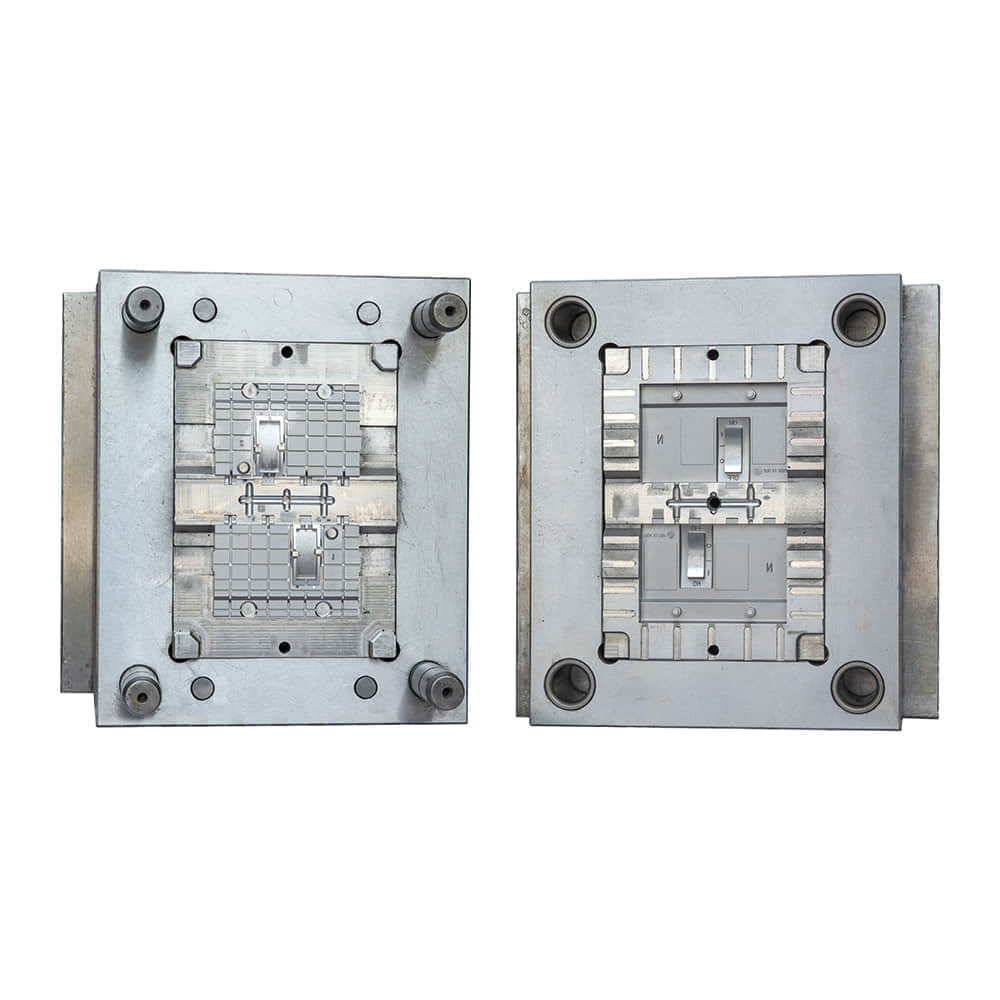
Injection molding is a widely used manufacturing process for producing plastic parts in large volumes. From intricate consumer electronics to everyday household items, a myriad of products relies on injection molding. At the core of this process is the injection mold, a meticulously designed tool that shapes molten plastic into the desired form. Injection mold manufacturers are the architects of these molds, and their work underpins numerous industries. The Art and Science of Injection Mold Making Creating an injection mold is no simple feat; it’s a harmonious blend of art and science. It starts with a detailed understanding of the product being manufactured. Manufacturers work closely with their clients to comprehend design specifications, material requirements, and production volume. This initial collaboration sets the stage for the mold’s development. The next step is engineering the mold. Advanced computer-aided design (CAD) software is employed to translate product designs into three-dimensional mold blueprints. These digital models are fine-tuned to optimize the molding process for efficiency and product quality. Skilled engineers meticulously calculate every angle and curve, ensuring that the mold will produce precise and consistent results. Material Selection and Tooling Selecting the appropriate materials is crucial in mold manufacturing. The choice depends on factors such as the type of plastic to be used, the expected production volume, and the desired mold lifespan. High-quality metals like steel or aluminum are commonly used due to their durability and heat resistance. Once the material is chosen, the manufacturing process begins. This involves precision machining and tooling. CNC (Computer Numerical Control) machines are used to cut and shape the mold’s components with unparalleled accuracy. Every cavity, core, and runner must align perfectly to ensure the final product meets specifications. Precision and Quality Control Quality control is an ongoing process throughout mold manufacturing. Each component is meticulously inspected, and any imperfections or deviations are corrected. This rigorous attention to detail ensures that the mold will perform flawlessly, producing consistent, high-quality parts. Testing and Refinement Before the mold is put into production, it undergoes a series of tests and trials. This phase allows manufacturers to fine-tune the mold’s performance, ensuring that it meets the client’s exact specifications. Adjustments are made to factors such as temperature, pressure, and cooling time to optimize the molding process. Final Thoughts Injection mold manufacturers are the unsung heroes of modern manufacturing. Their craftsmanship and precision enable the mass production of countless products that we use in our daily lives. From the initial design stages to the final testing and refinement, the work of these manufacturers is a testament to the intricate blend of art and science that goes into creating injection molds. Without their expertise, the world of manufacturing would not be what it is today. In conclusion, injection mold manufacturers play a vital role in the production of plastic parts that are integral to our daily lives. Their dedication to precision and quality ensures that the products we rely on are consistently well-made. The next time you pick up a plastic item, take a moment to appreciate the craftsmanship and ingenuity that went into creating its mold.
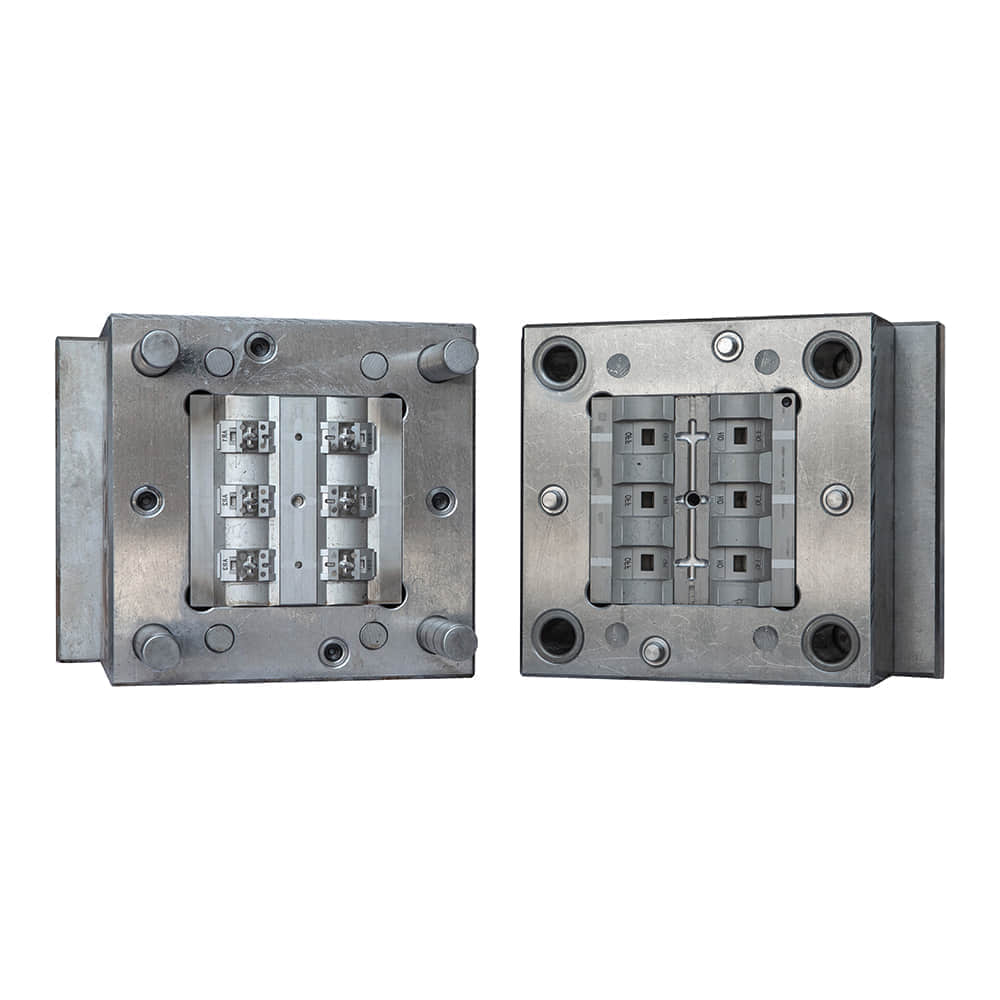