SMC Molding, or Sheet Molding Compound Molding, is a cutting-edge manufacturing process that has rapidly gained popularity in the composite material industry. This innovative technique offers numerous advantages over traditional methods, making it a game-changer in various industries. In this article, we will delve into the world of SMC molding, exploring its key features, benefits, applications, and future prospects.
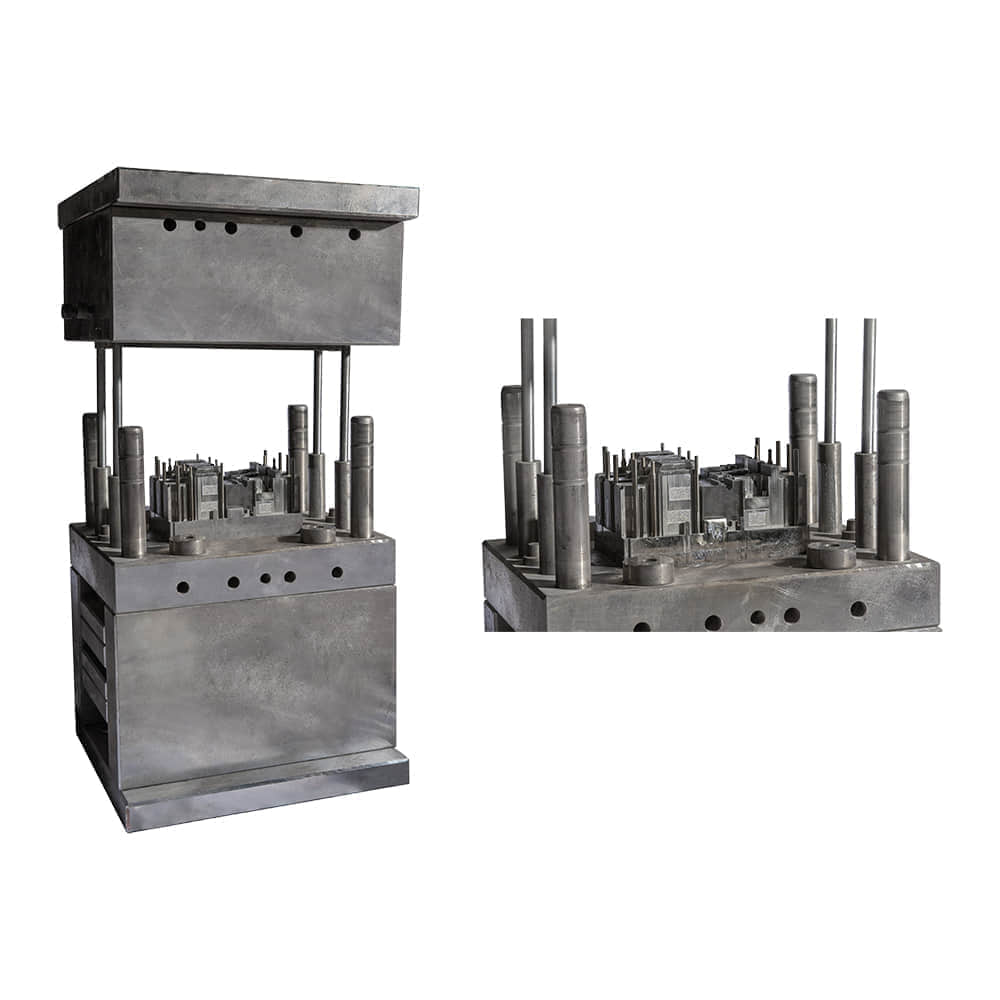
Understanding SMC Molding
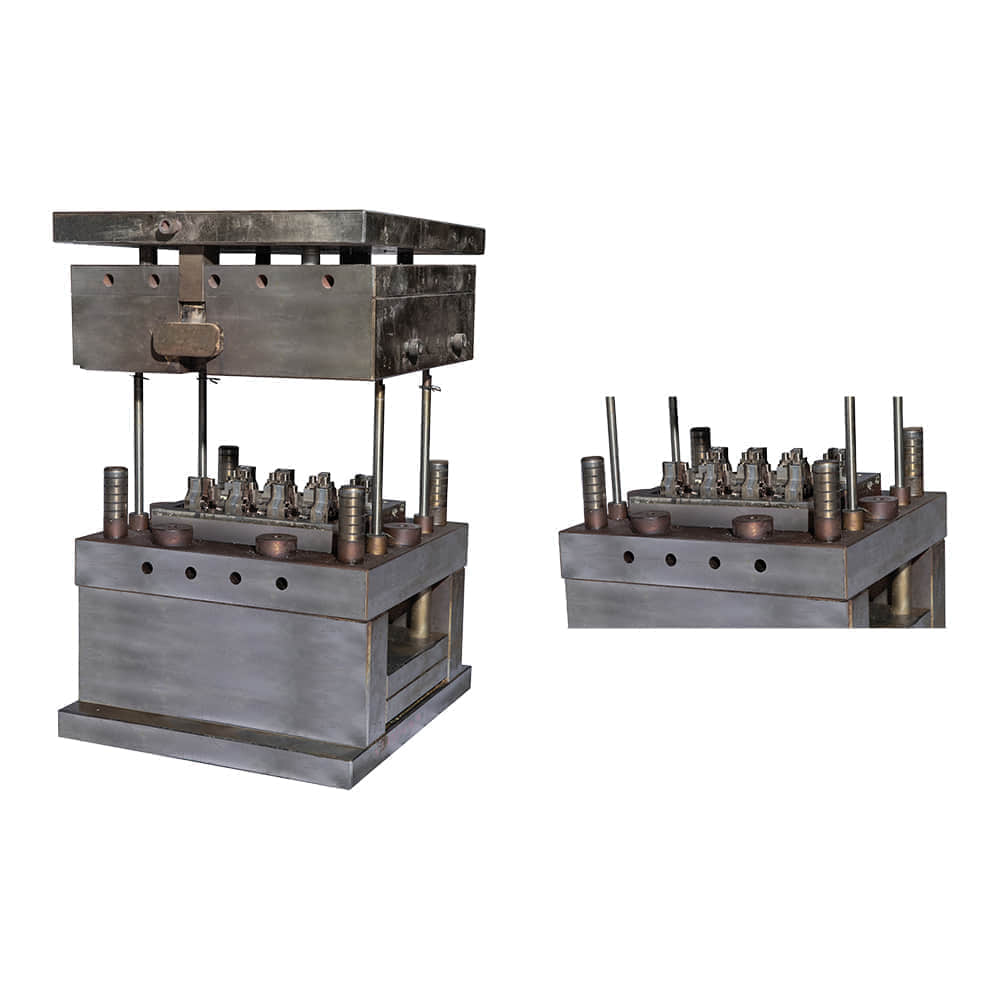
SMC molding is a process that involves the transformation of composite materials into intricate and precise shapes. It starts with a mixture of resins, reinforcements (such as glass fibers), and additives, all combined to form a thick, putty-like material called sheet molding compound (SMC). This SMC is then fed into a hydraulic press, where it undergoes compression molding under high pressure and temperature. The result is a solid, high-strength, and complex composite part that is ready for various applications. Advantages of SMC Molding Design Flexibility: SMC molding allows for intricate and precise designs, making it ideal for components with complex geometries. This flexibility opens doors to creative solutions and innovations across industries. High Strength and Durability: SMC parts exhibit exceptional strength and durability, making them resistant to impact, corrosion, and environmental factors. They are also lightweight, making them suitable for applications where weight reduction is essential. Cost-Effective: SMC molding can be a cost-effective choice due to reduced material waste and efficient production processes. It also requires fewer post-processing steps, saving both time and money. Excellent Surface Finish: SMC parts boast a smooth and high-quality surface finish, eliminating the need for additional painting or finishing work in many cases. Environmental Friendliness: SMC molding is eco-friendly as it generates minimal waste and emissions during production. It aligns with the growing demand for sustainable manufacturing practices. Applications of SMC Molding SMC molding finds applications across a wide range of industries, including: Automotive: SMC parts are increasingly used in vehicle exteriors, interiors, and structural components, contributing to weight reduction and fuel efficiency. Aerospace: In the aerospace industry, SMC molding is utilized to manufacture lightweight and robust components for aircraft and spacecraft. Construction: SMC materials are employed in building facades, electrical enclosures, and other construction elements due to their durability and weather resistance. Electrical and Electronics: SMC molding is used for electrical enclosures, switchgear components, and insulators due to its excellent electrical properties. Renewable Energy: SMC parts play a crucial role in the wind energy sector, where they are used in turbine blades and nacelles. Consumer Goods: SMC molding is employed in the production of consumer goods such as furniture, sports equipment, and appliance housings. The Future of SMC Molding As technology and materials science continue to advance, SMC molding is poised for even greater innovation and adoption. Researchers are exploring new composite formulations, including sustainable and bio-based materials, to further enhance the environmental credentials of SMC products. Additionally, automation and digitalization are being integrated into SMC manufacturing processes, leading to increased precision, reduced production times, and greater cost-effectiveness. The development of 3D printing and additive manufacturing techniques may also complement SMC molding in the future. In conclusion, SMC molding represents a significant advancement in composite material manufacturing. Its versatility, strength, cost-effectiveness, and eco-friendliness make it a compelling choice for a wide range of applications. As industries continue to seek lightweight, durable, and sustainable solutions, SMC molding is set to play an increasingly pivotal role in shaping the future of manufacturing.
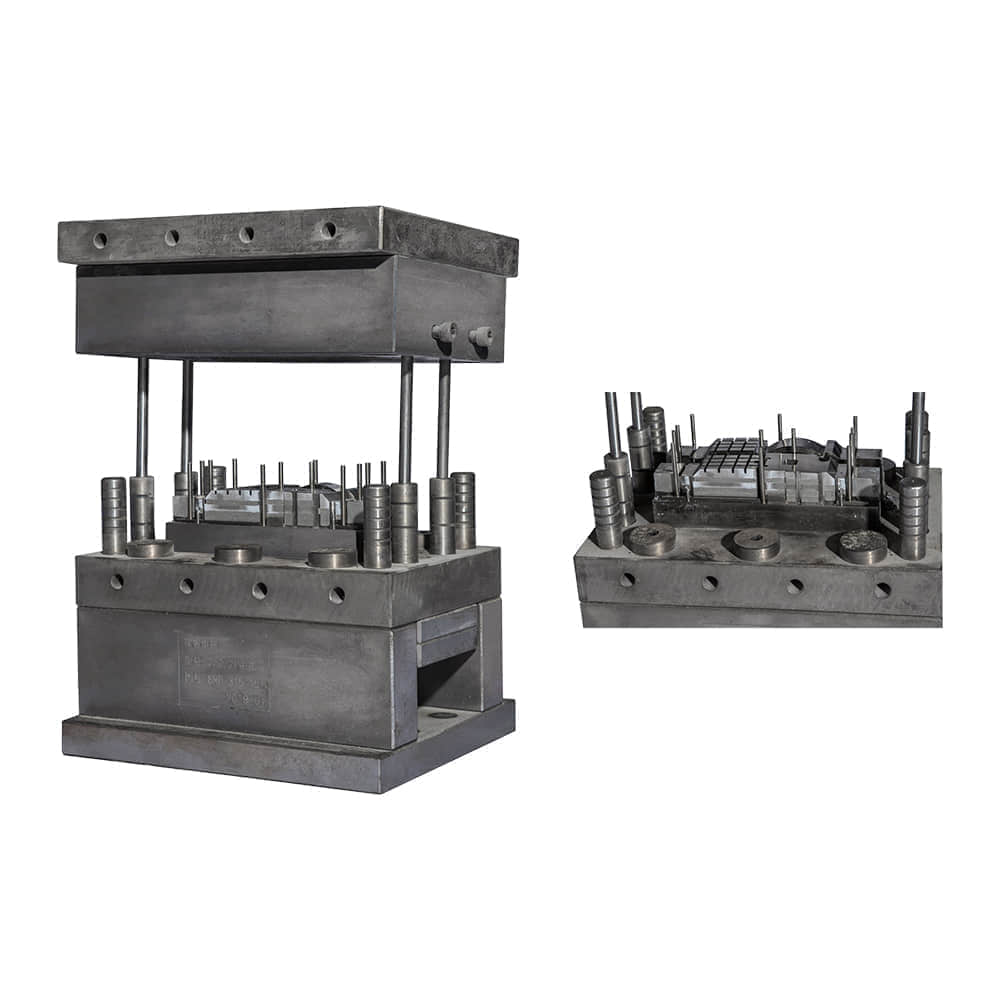