In the world of precision metal stamping, technological advancements have paved the way for more efficient and accurate manufacturing processes. One such innovation that stands out is the progressive die. This intricate tool and technique have revolutionized the way manufacturers produce complex metal parts and components. In this article, we delve into the intricacies of progressive die technology and its transformative impact on the manufacturing industry.
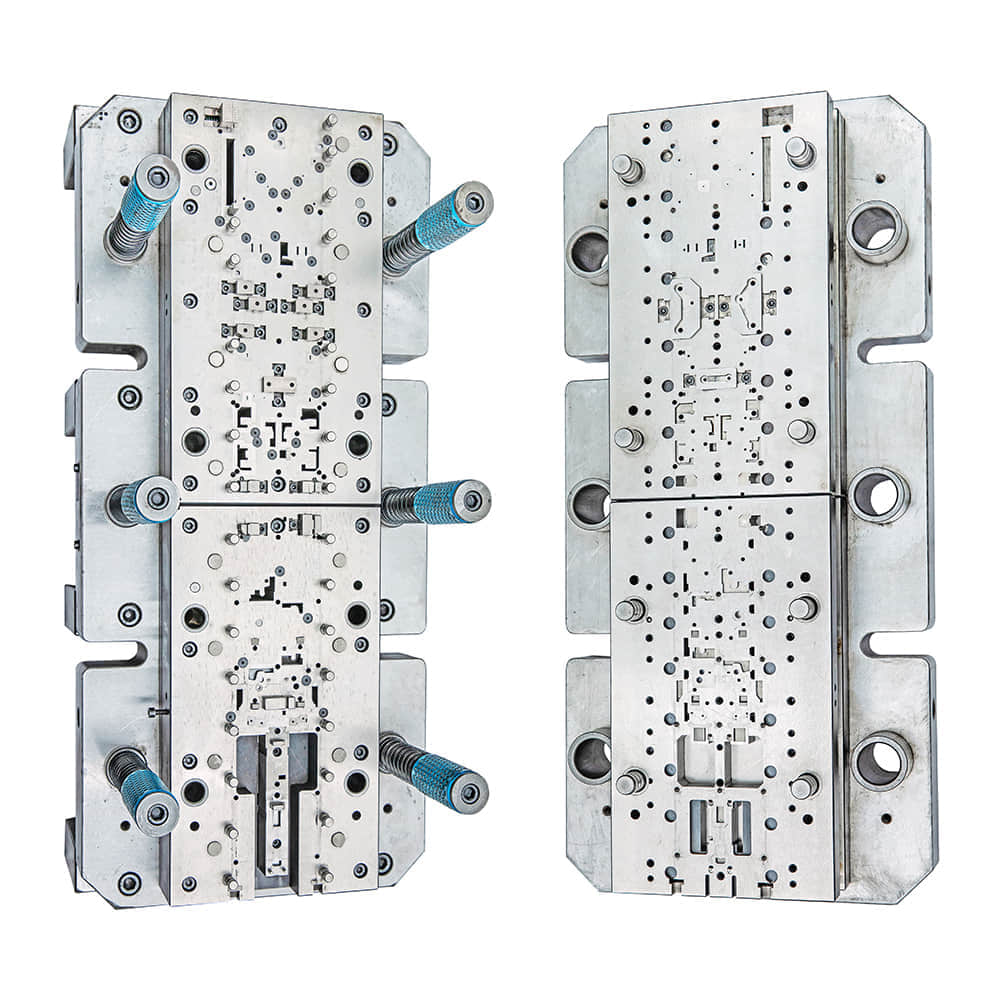
Understanding Progressive Die:A progressive die is a multi-station tool used in high-volume manufacturing processes, primarily for the production of intricate metal parts. Unlike traditional methods that require multiple individual operations, a progressive die performs a sequence of operations in a single press run. Each station in the die performs a unique cutting, bending, or forming operation on the metal sheet as it progresses through the die. This continuous process eliminates the need for manual handling between operations, reducing labor costs and minimizing errors.
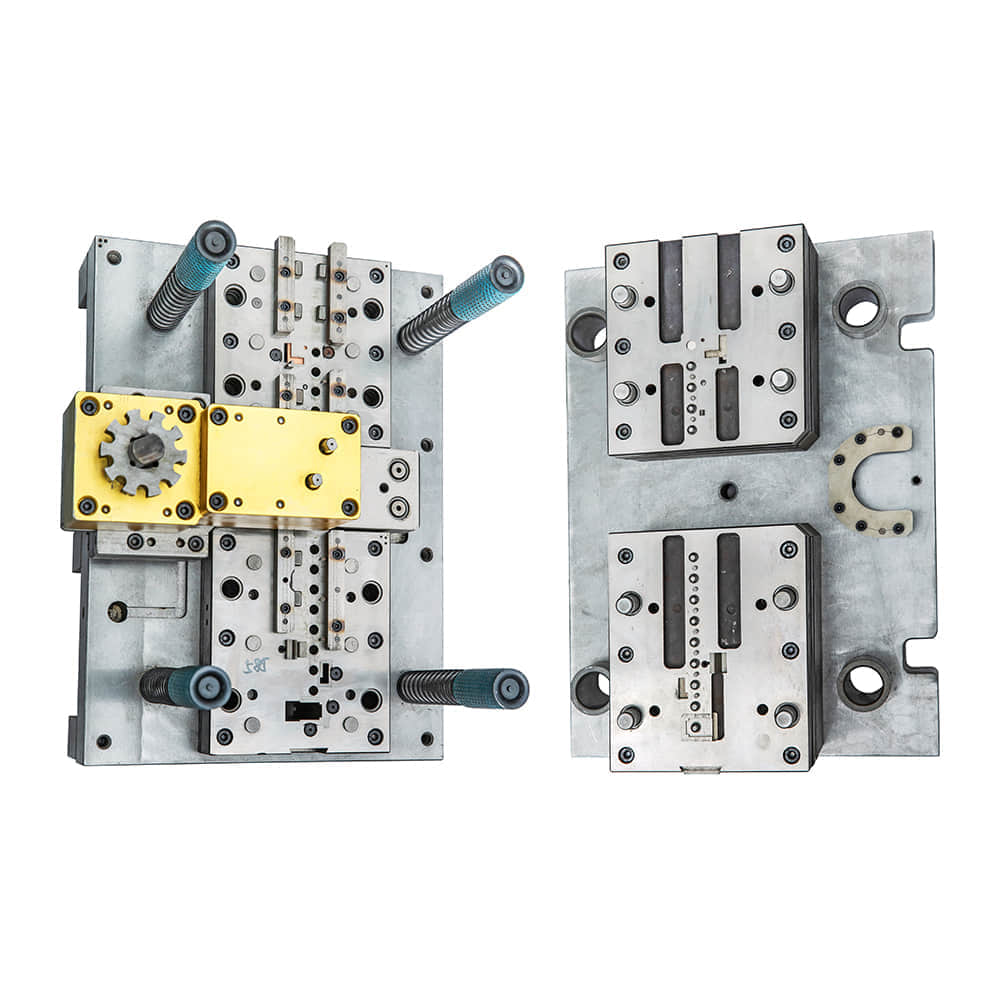
The Anatomy of a Progressive Die:A typical progressive die consists of a series of stations, each equipped with different cutting, punching, and forming tools. The metal sheet advances from one station to another, with each station performing a specific operation. This incremental process allows for the creation of complex parts with high precision. From blanking and bending to threading and extruding, a progressive die can integrate numerous operations into a single seamless workflow. Advantages of Progressive Die: Enhanced Efficiency:Progressive dies significantly improve production efficiency. As each station performs its designated task simultaneously, the overall production time is drastically reduced compared to traditional methods. Precision and Consistency:The automated nature of progressive die manufacturing ensures consistent results. This is crucial in industries where even the slightest deviation can lead to faulty products or compromised functionality. Reduced Material Waste:Precise control over each operation minimizes material waste. Traditional manufacturing processes often lead to higher scrap rates due to manual errors or inconsistencies between operations. Cost-Effectiveness:Although the initial setup cost for a progressive die can be high, the long-term benefits outweigh this investment. The increased production speed, reduced labor costs, and minimal scrap rates contribute to significant cost savings over time. Complex Designs:Progressive dies are ideal for creating intricate parts with complex designs. The ability to integrate multiple operations in a single die allows manufacturers to produce parts that would be challenging or impossible to create using conventional methods. Applications Across Industries:The versatility of progressive die technology has led to its widespread adoption across various industries: Automotive:From chassis components to intricate engine parts, progressive die technology plays a vital role in manufacturing automotive components with high precision and consistency. Electronics:The production of electronic components like connectors, terminals, and small metal parts benefits from the intricate operations facilitated by progressive dies. Appliances:Many household appliances contain precisely stamped metal parts that are efficiently manufactured using progressive dies. Aerospace:The aerospace industry demands parts with uncompromised precision and durability. Progressive die technology meets these requirements effectively. Challenges and Future Prospects:While progressive die technology offers numerous benefits, it also presents challenges such as the initial design complexity and the need for skilled operators. However, ongoing advancements in computer-aided design (CAD) software and automation are mitigating these challenges. Looking ahead, progressive die technology is poised to continue evolving, incorporating smart manufacturing principles, real-time monitoring, and predictive maintenance. As the manufacturing landscape embraces Industry 4.0 concepts, progressive die technology will likely play a pivotal role in shaping the factories of the future. Conclusion:Progressive die technology has ushered in a new era of precision metal stamping. Its ability to integrate multiple operations, enhance efficiency, and produce intricate parts has transformed the manufacturing landscape across industries. As technology continues to advance, we can expect progressive die techniques to become even more sophisticated, solidifying their position as a cornerstone of modern manufacturing.
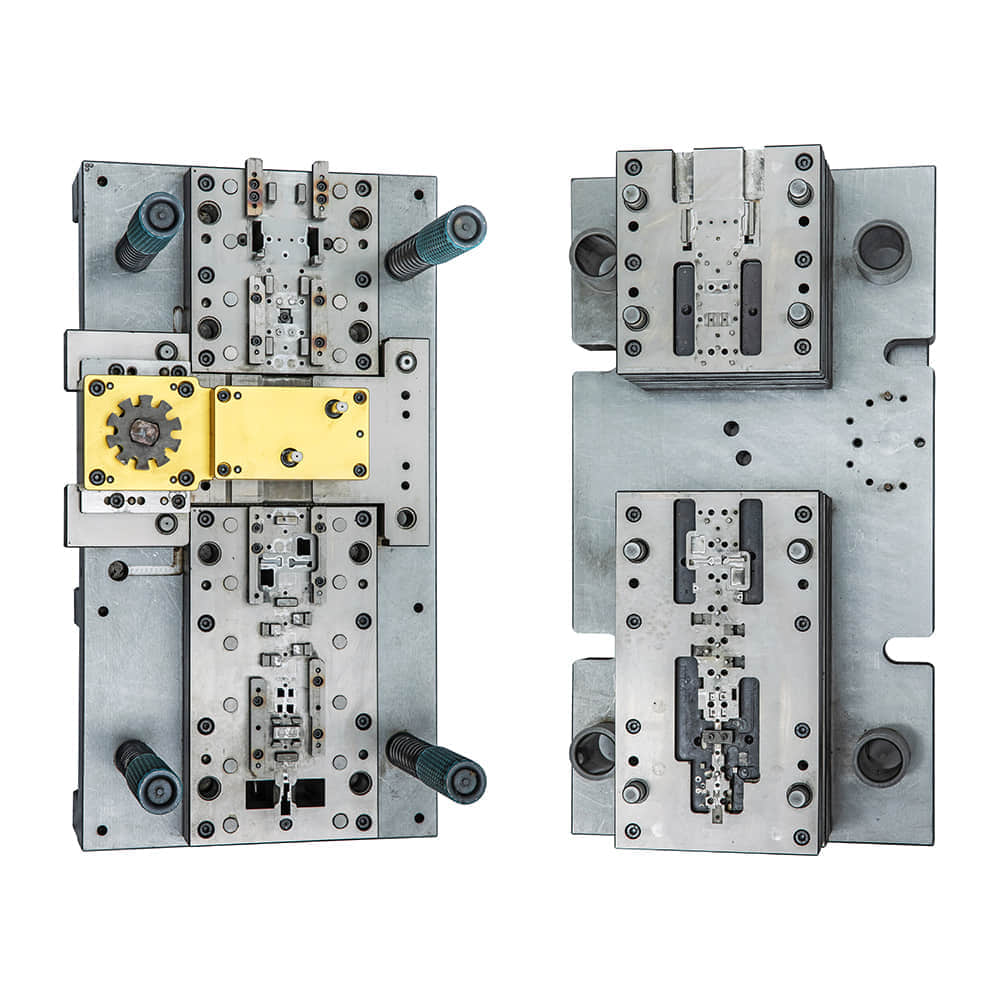