Pneumatic ball valves are widely recognized for their efficiency and reliability in fluid control applications across various industries. These valves use compressed air to control the opening and closing of the valve, offering a highly effective way of regulating the flow of gases, liquids, and steam in piping systems. Pneumatic ball valves combine the simplicity of ball valve design with the precise control capabilities of pneumatic actuators, making them essential for processes requiring automated operation and reliable performance.
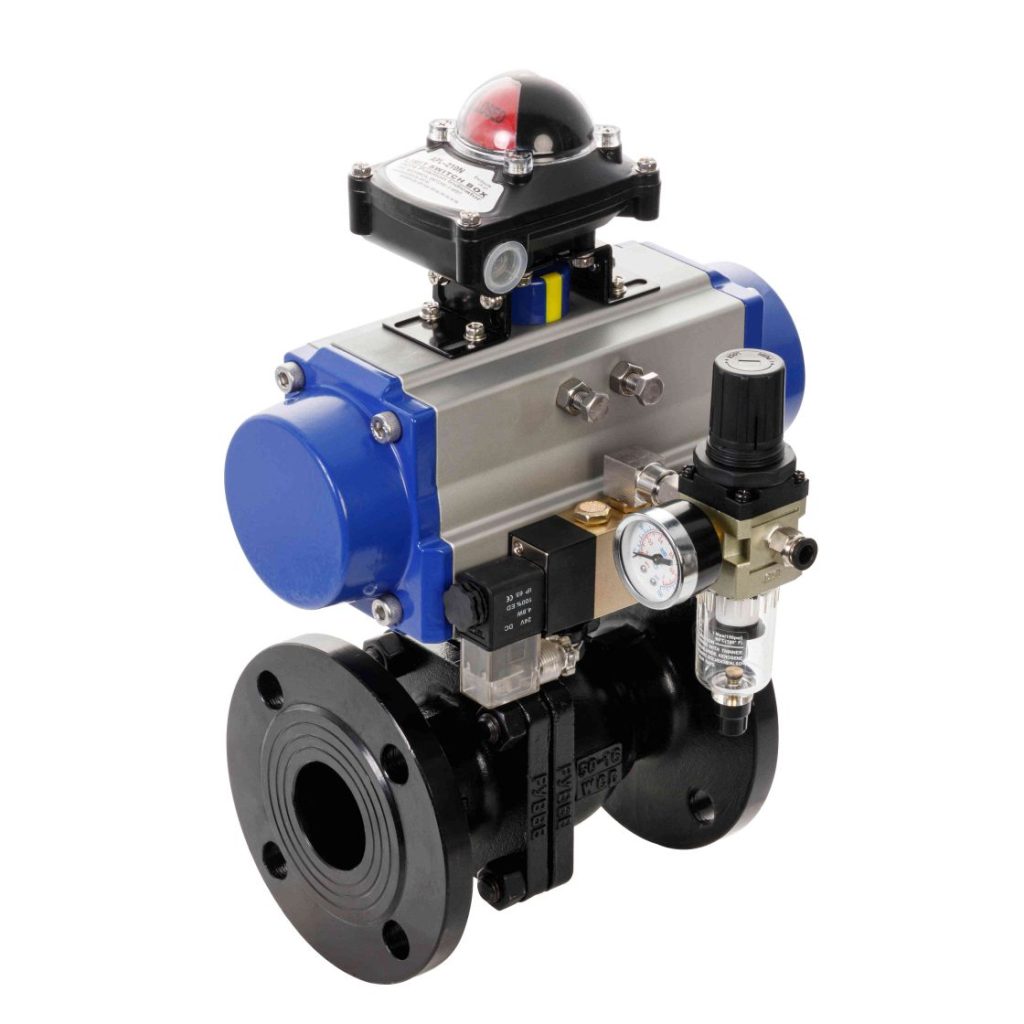
What is a Pneumatic Ball Valve?
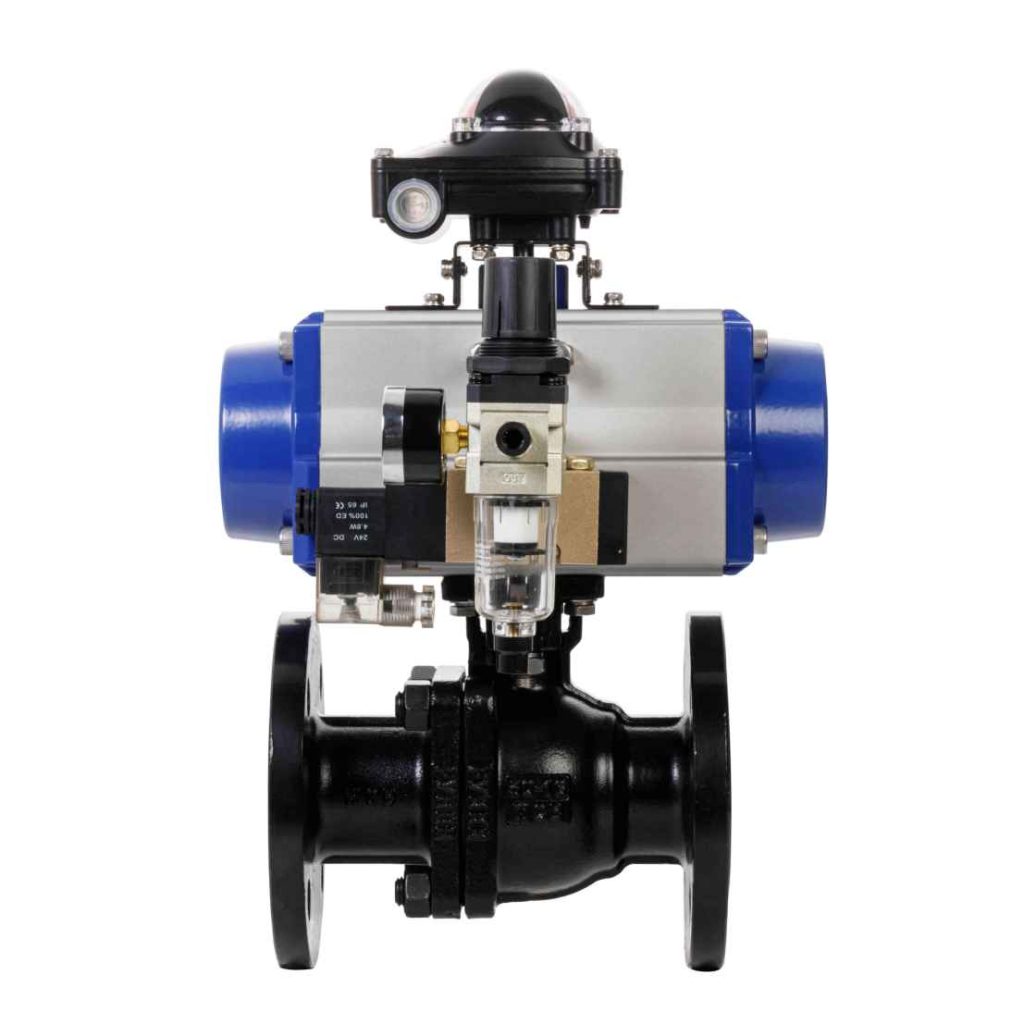
A pneumatic ball valve consists of three main components: the valve body, the ball, and the actuator. The valve body is typically made of durable materials such as stainless steel, brass, or PVC, while the ball inside the valve has a hole through its center that allows fluid to flow when the valve is open. The actuator is a key element in the functioning of the pneumatic ball valve, as it is powered by compressed air to rotate the ball to either the open or closed position. The primary purpose of a pneumatic ball valve is to control the flow of media through a pipeline by using air pressure to actuate the valve. The pneumatic actuator typically operates using an input of compressed air, which moves the internal mechanism to rotate the valve ball. This simple yet effective design makes pneumatic ball valves suitable for a range of applications in industries like oil and gas, water treatment, chemicals, food processing, and HVAC systems.
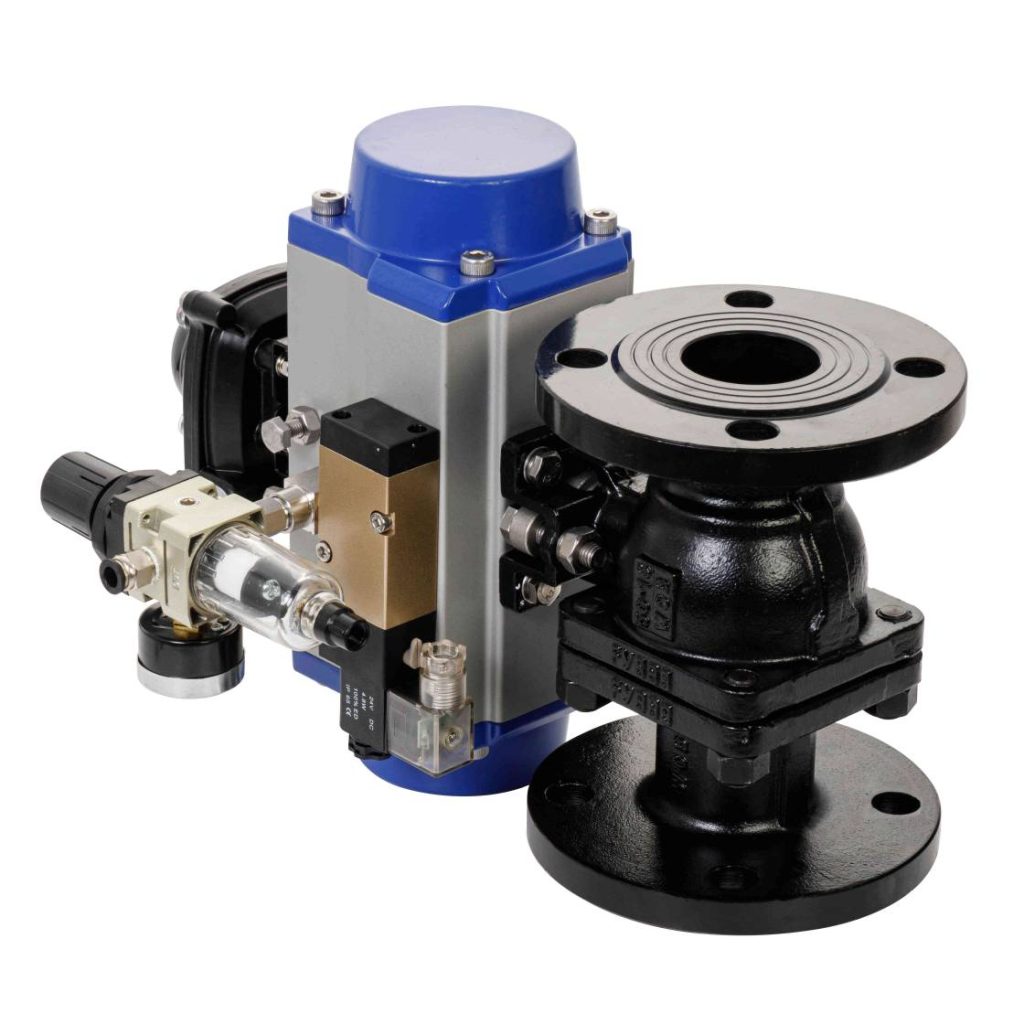