In the ever-evolving world of automotive engineering, the significance of electrical systems in vehicles cannot be overstated. With the increasing number of electronic components in modern cars, from safety systems to comfort features, the role of automotive relay manufacturers has become critical. Automotive relays, which are integral components in vehicle electrical systems, play a crucial role in controlling and managing electrical circuits. These small yet powerful devices ensure the smooth operation of a wide range of automotive functions. This article explores the importance of automotive relay manufacturers, the technologies they employ, and their impact on the future of automotive systems.
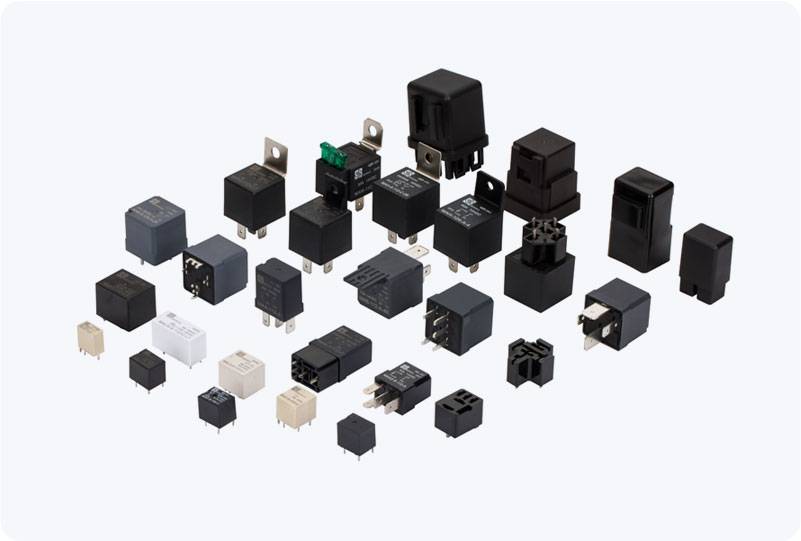
Understanding Automotive Relays Automotive relays are electrically operated switches used to control various electrical circuits within a vehicle. They are typically used in low-current circuits to control high-current devices like motors, lights, and other electrical components. A relay consists of a coil, contacts, and an armature. When an electric current flows through the coil, it generates a magnetic field that moves the armature, closing or opening the contacts. This action allows the relay to control power to other parts of the vehicle. For instance, relays are commonly used to control the starter motor, air conditioning system, power windows, and lighting systems in cars. They act as an intermediary between the low-power control circuits and the high-power circuits, preventing the need for large switches and simplifying the electrical design.