In today’s rapidly evolving manufacturing landscape, the role of advanced technologies and materials is paramount in shaping the way products are designed and produced. Bulk Molding Compounds (BMC) have emerged as a remarkable solution, offering versatility, durability, and design freedom. At the heart of this revolution are BMC molding manufacturers, who play a pivotal role in transforming raw materials into exceptional finished products.
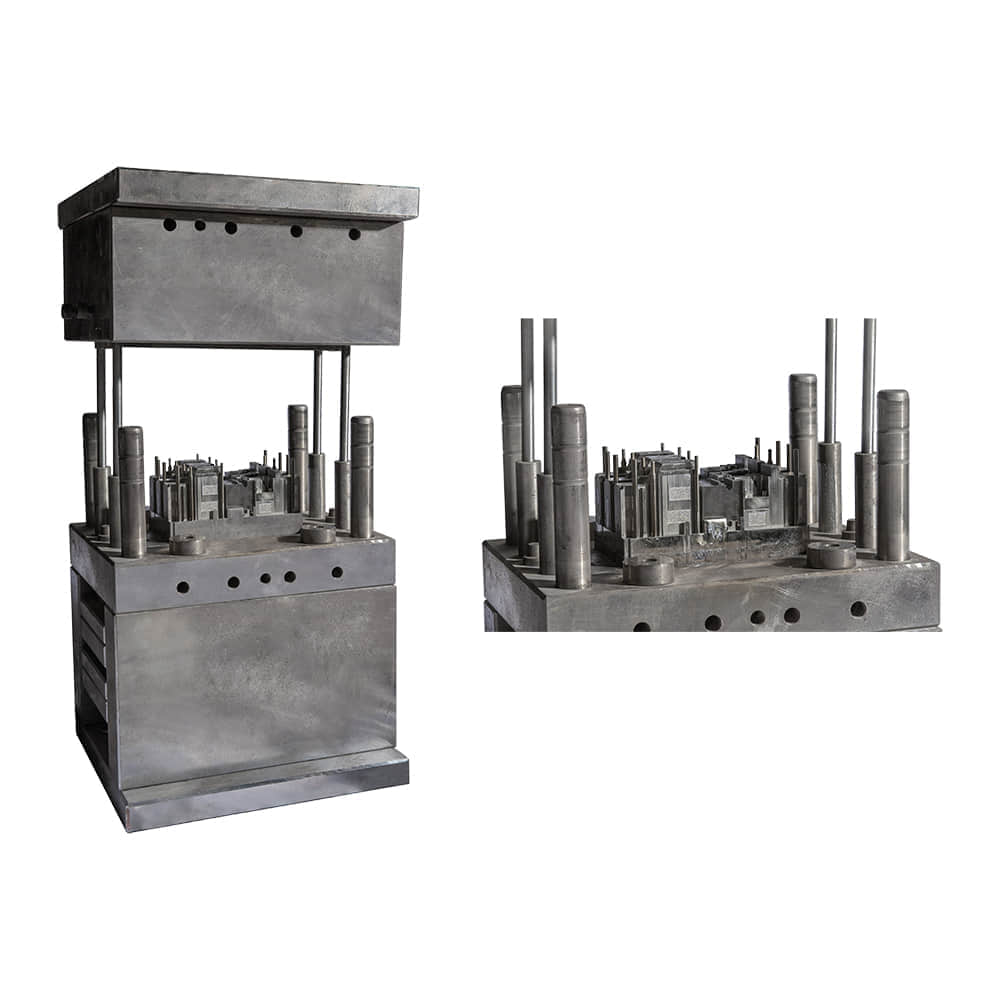
BMC, a composite material consisting of a blend of thermosetting resins, chopped glass fibers, mineral fillers, and additives, has gained immense popularity across various industries. It boasts an impressive range of attributes, including high dimensional stability, excellent electrical insulation, corrosion resistance, and remarkable flame-retardant properties. BMC’s adaptability makes it ideal for manufacturing intricate and complex shapes that are otherwise challenging to produce using conventional materials.
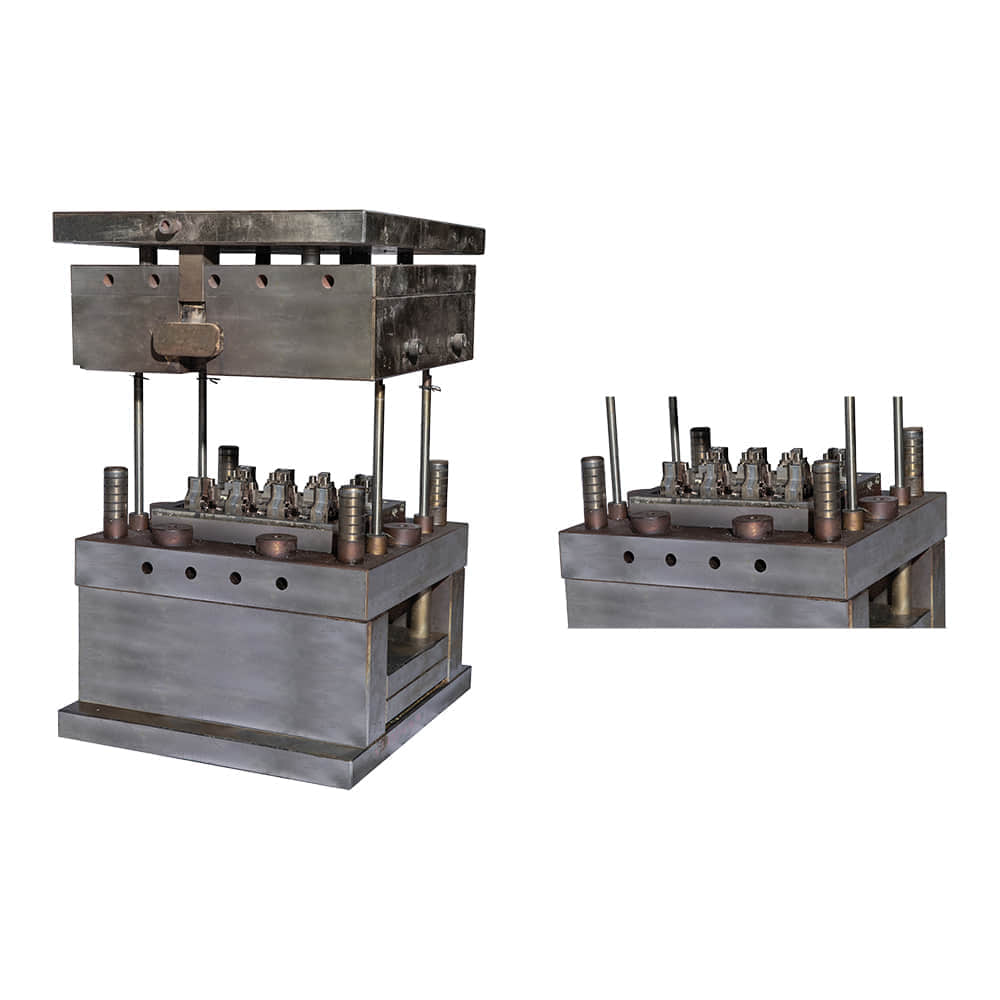
BMC molding manufacturers are the driving force behind this transformational material. These manufacturers specialize in the production of BMC components by utilizing advanced techniques such as injection molding and compression molding. The process begins with the careful selection and blending of raw materials to create a homogenous compound. This compound is then heated and injected into molds with precision and expertise, ensuring that even the most intricate details are captured. One of the key advantages of BMC molding manufacturers is their ability to create parts that are not only mechanically robust but also aesthetically pleasing. The inherent fluidity of BMC during molding allows for the production of parts with smooth finishes and intricate designs, eliminating the need for extensive post-production finishing. This efficiency not only reduces production time but also contributes to a more sustainable manufacturing process. The applications of BMC molded products span a wide spectrum of industries. In the automotive sector, BMC components are increasingly utilized for their lightweight yet strong characteristics, contributing to improved fuel efficiency and overall vehicle performance. In the electrical and electronics industry, BMC’s exceptional insulating properties make it an ideal choice for producing switchgears, connectors, and housings for various devices. Furthermore, the construction industry benefits from BMC’s corrosion resistance and durability, employing it in products such as electrical junction boxes and infrastructure components. The collaboration between product designers, engineers, and BMC molding manufacturers is crucial in harnessing the full potential of this remarkable material. Manufacturers not only bring technical expertise to the table but also contribute valuable insights into material capabilities and limitations. This synergy ensures that designs are not only innovative but also feasible to produce efficiently and cost-effectively. As industries continue to push the boundaries of innovation, BMC molding manufacturers find themselves at the forefront of this exciting evolution. Their ability to translate conceptual designs into tangible, high-quality products makes them indispensable partners for businesses across various sectors. With a focus on sustainability, efficiency, and performance, BMC molding manufacturers are shaping a future where intricate designs meet unparalleled functionality. In conclusion, the world of manufacturing is undergoing a transformative journey, with BMC molding manufacturers as catalysts for change. Through harnessing the power of BMC, these manufacturers are turning visions into reality, creating products that redefine industry standards. As technology advances and new frontiers are explored, the collaboration between industries and BMC molding manufacturers will undoubtedly continue to yield innovations that leave a lasting impact.
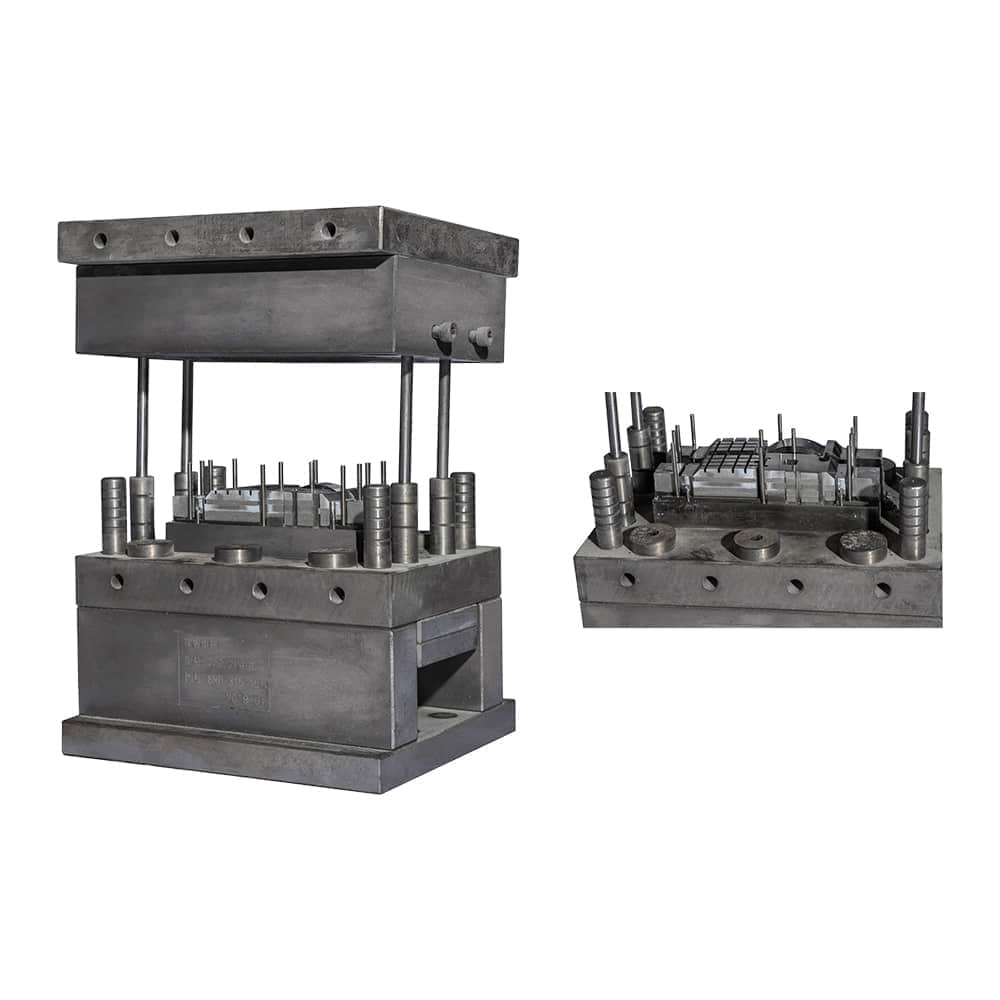