In the intricate realm of manufacturing, thermosetting molds play a pivotal role in shaping products that encompass various industries, from automotive to electronics, and beyond. These molds, carefully crafted by skilled manufacturers, facilitate the production of durable and heat-resistant products. This article delves into the fascinating world of thermosetting mold manufacturers, shedding light on their significance, processes, and contributions to modern manufacturing.
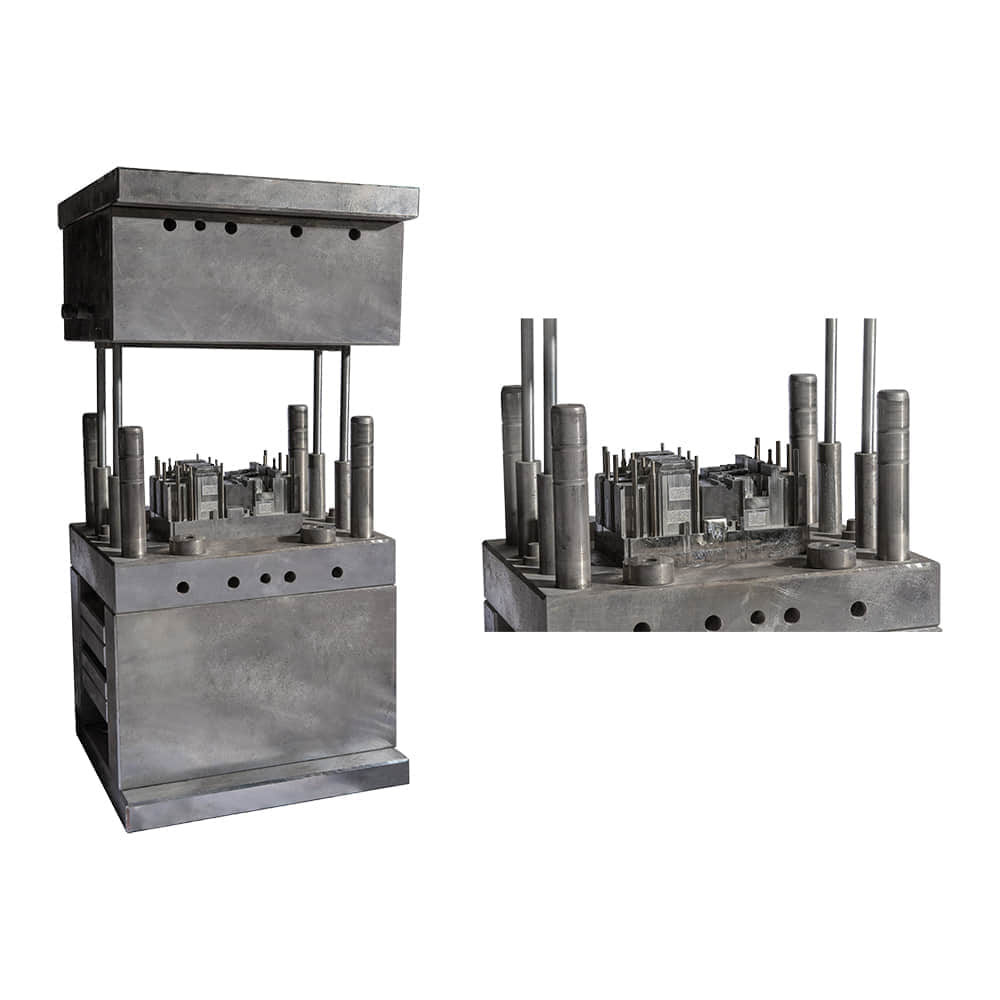
The Significance of Thermosetting Molds
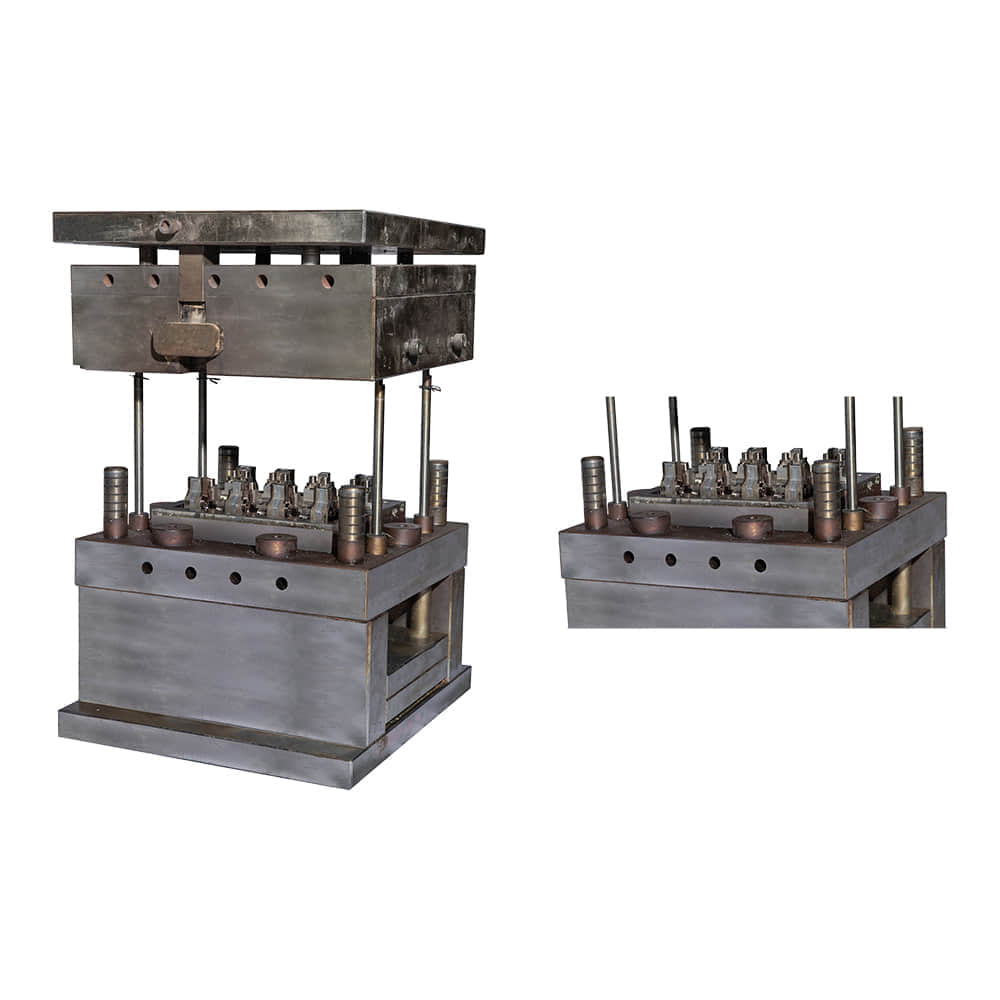
Thermosetting molds are an indispensable component of modern manufacturing. Unlike thermoplastics, which can be melted and reshaped multiple times, thermosetting plastics undergo a chemical reaction during the molding process. This reaction irreversibly sets the plastic, giving it enhanced strength, heat resistance, and dimensional stability. This unique property makes thermosetting plastics and their corresponding molds crucial for applications where durability and resistance to high temperatures are paramount. The Craftsmanship Behind Thermosetting Mold Manufacturing Creating thermosetting molds is a meticulous process that requires a blend of expertise, precision, and innovation. Manufacturers begin by designing the mold, taking into account the intricacies of the final product. Computer-aided design (CAD) software plays a pivotal role in this phase, enabling engineers to conceptualize intricate mold designs with precision. Subsequently, the mold-making process kicks off with the selection of suitable materials. Thermosetting molds are often crafted from metals such as aluminum, steel, or bronze due to their excellent heat transfer properties and durability. The chosen material is carefully machined, shaped, and polished to create the desired mold structure. Manufacturing Techniques Thermosetting mold manufacturers employ various techniques to create molds tailored to specific applications. One common method is compression molding, where thermosetting materials are placed into an open mold cavity. The mold is then closed, and heat and pressure are applied, causing the material to take the desired shape. Injection molding is another prevalent technique, involving the injection of molten thermosetting material into a closed mold at high pressure. This method ensures intricate detailing and consistency in the final product’s dimensions. Additionally, manufacturers might employ transfer molding, a process that combines features of compression and injection molding to create complex products with precise detailing. Contributions to Modern Manufacturing The products that emerge from thermosetting molds have a far-reaching impact across industries. In the automotive sector, thermosetting plastics molded into components like engine parts and interior panels provide enhanced heat resistance and structural integrity. The electronics industry benefits from thermosetting molds by producing insulating materials for circuit boards that can withstand elevated temperatures without deforming. Moreover, thermosetting mold manufacturers contribute significantly to sustainable manufacturing practices. By crafting molds with longevity and durability in mind, these manufacturers reduce the need for frequent replacements, minimizing waste and conserving resources. Innovation and Future Trends As technology continues to advance, thermosetting mold manufacturers find themselves at the crossroads of innovation. Additive manufacturing, also known as 3D printing, has begun to make its mark in the realm of mold manufacturing. This technology offers the potential to create complex geometries and prototypes with reduced lead times. Furthermore, manufacturers are exploring novel materials that exhibit enhanced thermal and mechanical properties, expanding the capabilities of thermosetting molds even further. With the integration of IoT devices and sensors, molds can potentially provide real-time data on temperature and pressure during the molding process, enabling tighter quality control. Conclusion Thermosetting mold manufacturers are the unsung heroes behind the scenes, shaping the products that propel our modern world forward. Their craftsmanship, innovation, and dedication to producing durable and heat-resistant molds have led to advancements in industries ranging from automotive to electronics. As technology continues to evolve, so too will the techniques and materials employed by these manufacturers, ushering in a new era of precision molding and sustainable production.
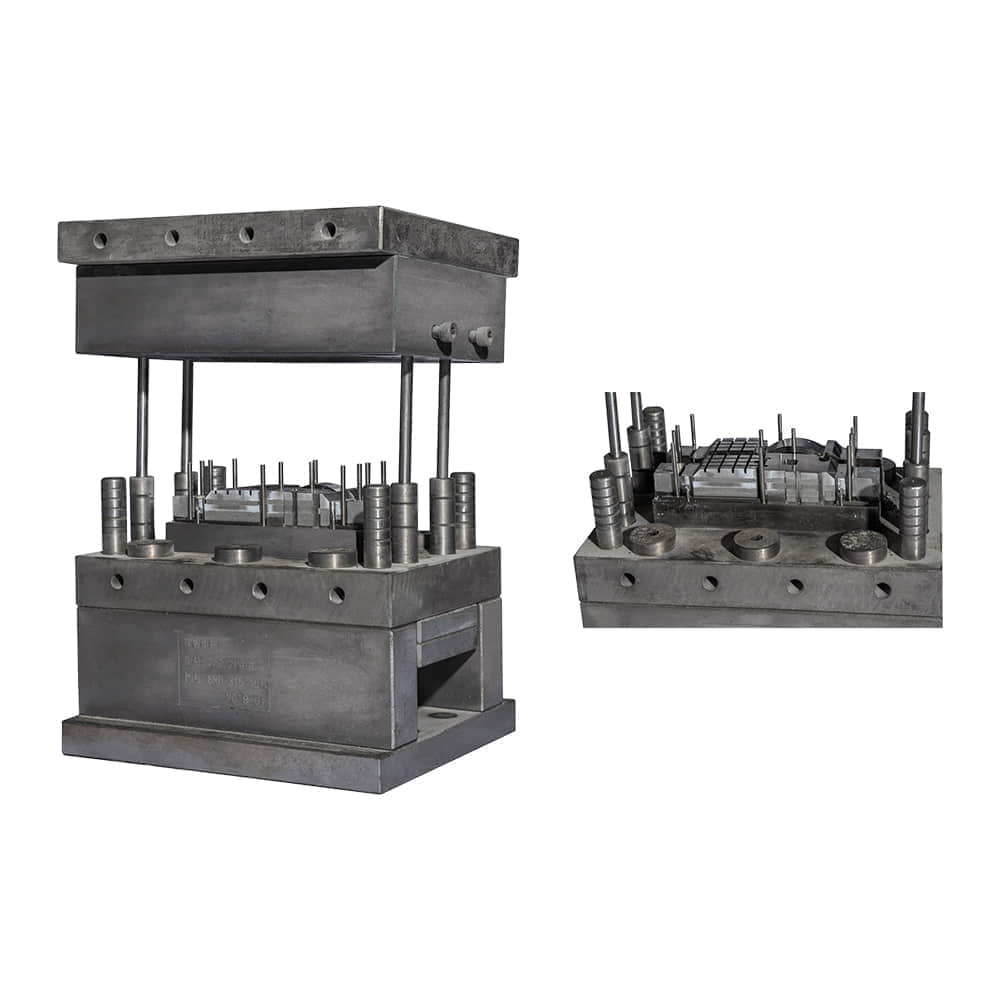