Metal stamping dies play a pivotal role in the manufacturing industry, enabling the efficient production of a wide range of products that we use in our daily lives. These intricate tools are designed and produced by specialized manufacturers who possess a deep understanding of metalworking, precision engineering, and innovative techniques. In this article, we delve into the realm of metal stamping die manufacturers, exploring their significance, the manufacturing process, and the evolving landscape of this industry.
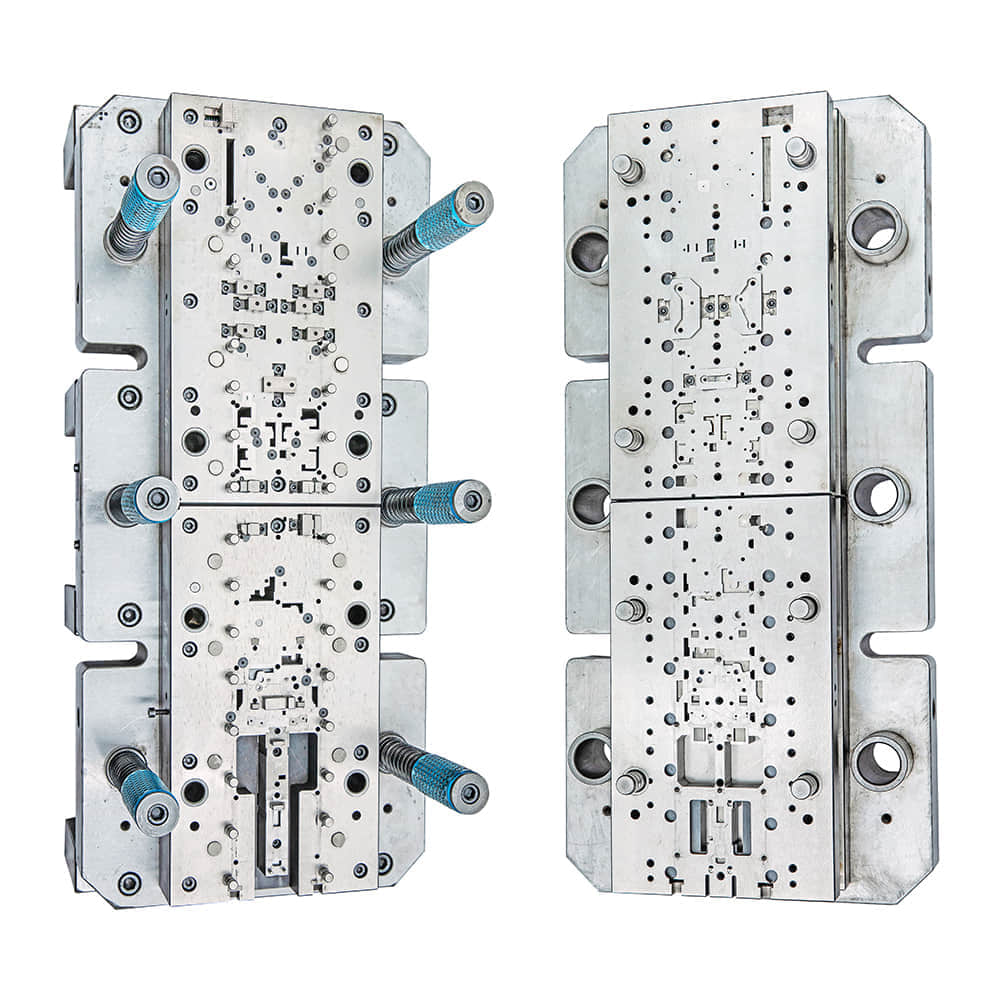
The Significance of Metal Stamping Die Manufacturers
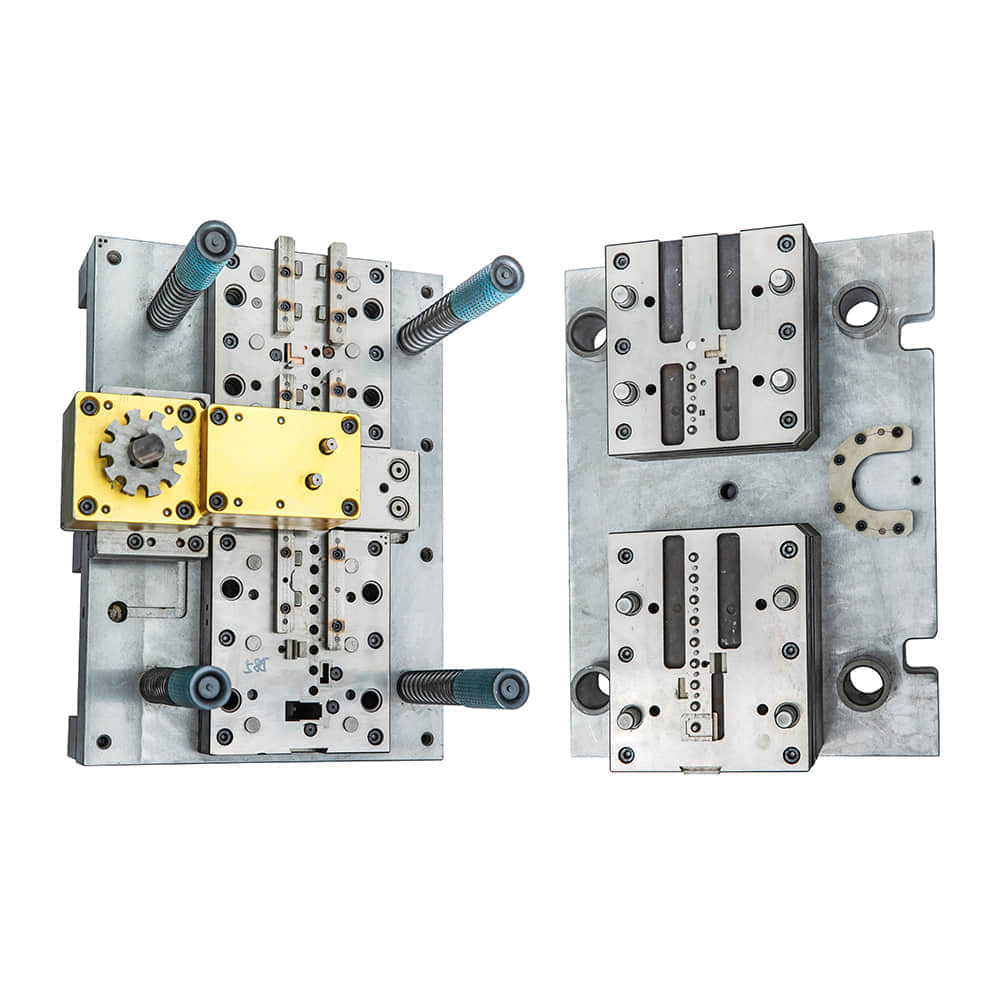
Metal stamping dies are instrumental in the production of various metal components, from simple household items to complex automotive parts. These dies essentially serve as molds, shaping metal sheets into specific forms through a process known as stamping. The accuracy, durability, and intricacy of the final product heavily rely on the precision and quality of the metal stamping dies used. The Manufacturing Process The creation of metal stamping dies is a meticulous and multi-step process that demands both expertise and technological sophistication. Here’s a glimpse into the typical manufacturing process: Design and Engineering: Manufacturers collaborate with engineers and designers to conceptualize the die’s structure. Advanced software is employed to create detailed designs, considering factors such as material properties, die lifespan, and production volume. Material Selection: The choice of materials for the die is crucial. Tool steels, due to their hardness and wear resistance, are commonly used. The selection is based on factors like the type of metal being stamped, the expected production volume, and the die’s complexity. Machining and Tooling: Precision machining techniques, including CNC (Computer Numerical Control) milling and electrical discharge machining (EDM), are employed to shape the die components. These processes ensure that even the most intricate details are accurately transferred to the final product. Heat Treatment: To enhance the die’s hardness and durability, heat treatment processes like quenching and tempering are applied. This step significantly extends the die’s lifespan, making it capable of withstanding high pressures during the stamping process. Assembly and Testing: The various components of the die are meticulously assembled. The die is then rigorously tested for accuracy and durability using test stampings. Any necessary adjustments are made at this stage to ensure the die functions flawlessly. Surface Finishing: Post-assembly, the die’s surface is treated to resist corrosion and wear. This step further prolongs the die’s lifespan and ensures consistent performance over time. Continuous Improvement: Manufacturers often collect data from the stamping process and analyze the die’s performance. This information is used for ongoing refinement and optimization of the die’s design and production process. The Evolving Landscape The field of metal stamping die manufacturing is not immune to technological advancements and industry trends. Manufacturers are embracing automation and robotics to enhance precision and production efficiency. Computer simulations and virtual prototyping are being used to refine designs before physical production begins, saving both time and resources. Moreover, sustainability is gaining prominence in the manufacturing industry, including metal stamping die production. Manufacturers are exploring eco-friendly materials and energy-efficient processes to reduce the environmental impact of their operations. Conclusion Metal stamping die manufacturers play an integral role in shaping modern manufacturing. Their expertise, innovation, and commitment to quality contribute to the production of a wide array of products that we rely on daily. As technology continues to advance, we can expect these manufacturers to push the boundaries of what’s possible, delivering even more precise, efficient, and sustainable solutions for the industries they serve.
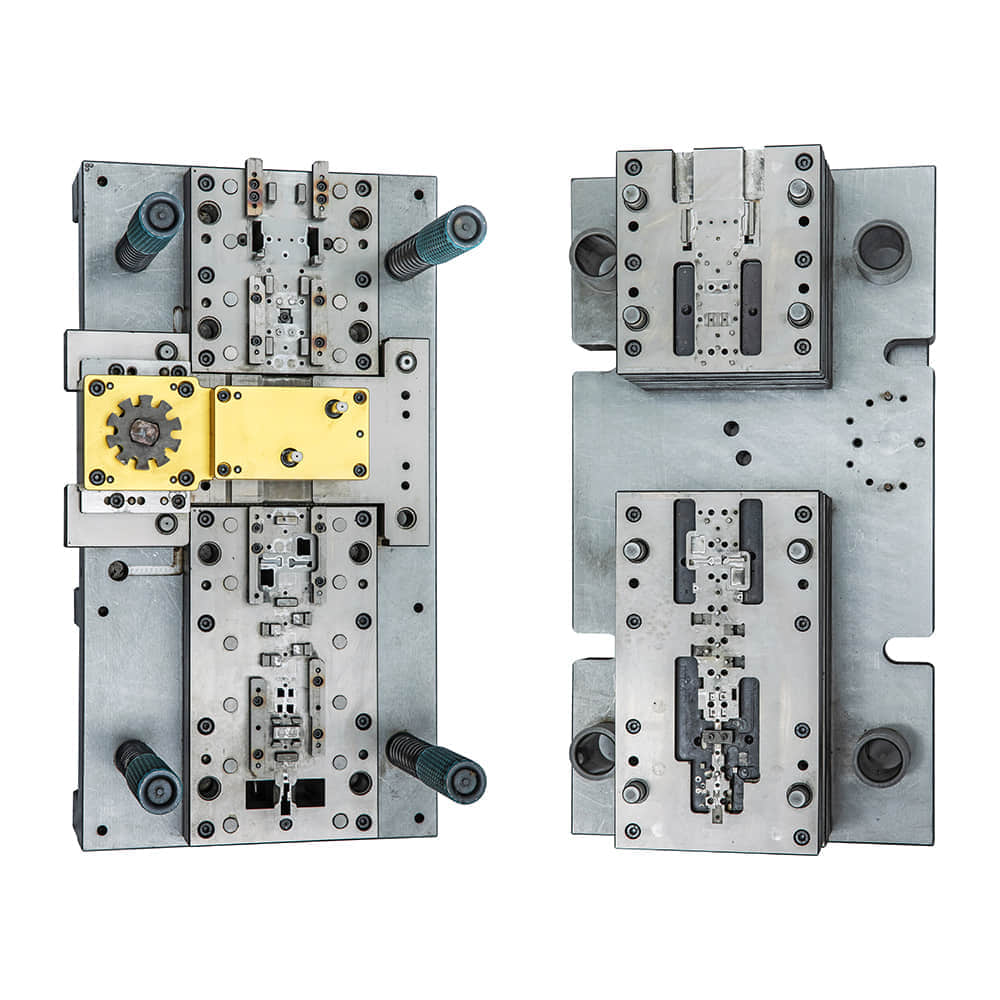