In the realm of electrical engineering, the intricate components that make up a circuit breaker play a crucial role in ensuring safety, reliability, and efficient energy distribution. Among these components, the MCCB (Molded Case Circuit Breaker) base cover stands as a vital element that safeguards the inner mechanisms and facilitates smooth operations. This article delves into the realm of MCCB base cover parts manufacturers, shedding light on their significance, manufacturing processes, and their contributions to modern electrical systems.
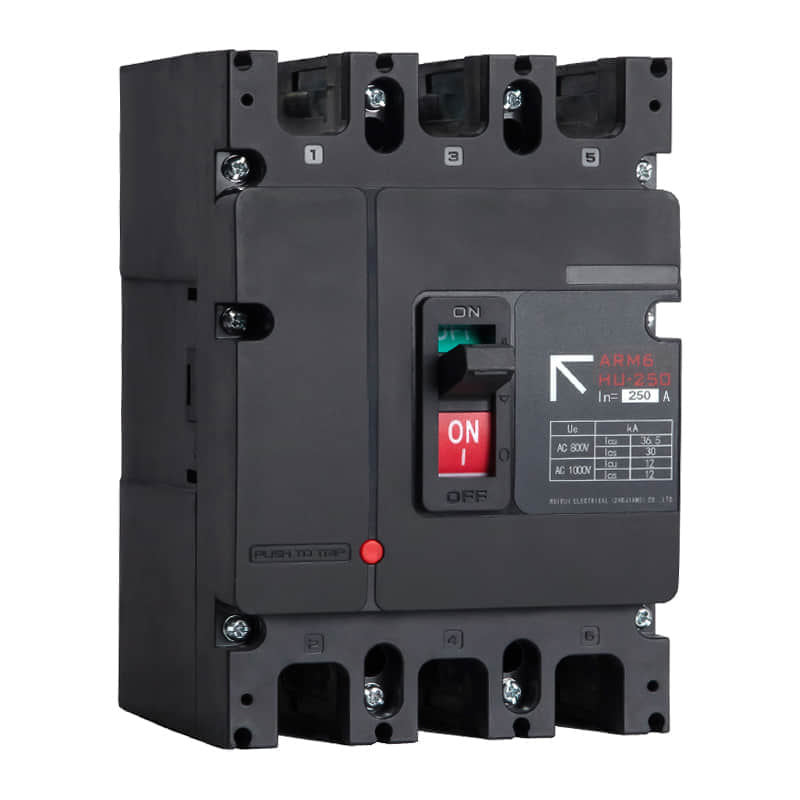
Significance of MCCB Base Cover Parts:
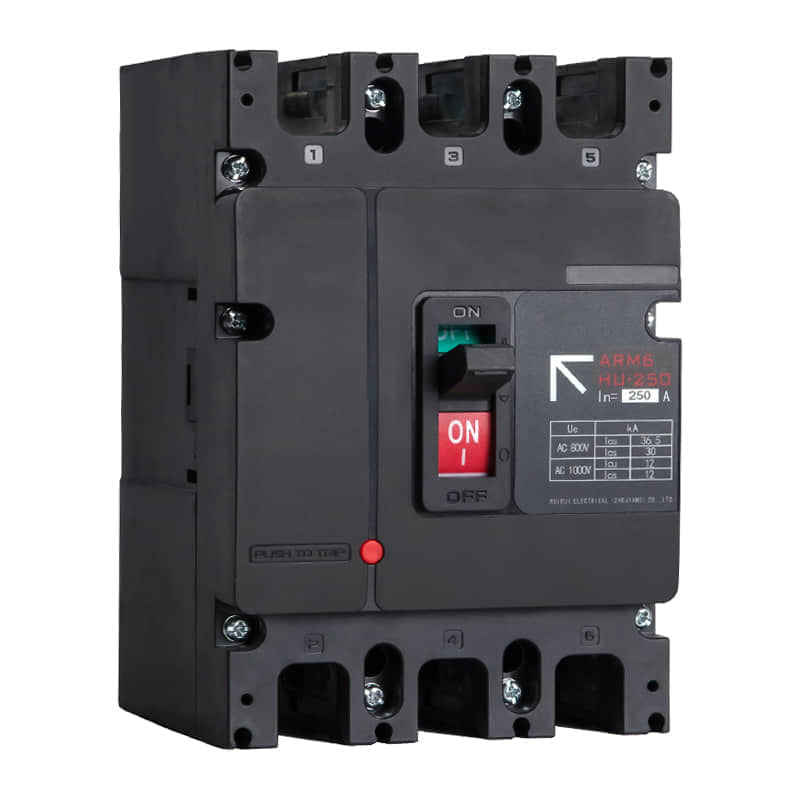
MCCBs are pivotal in safeguarding electrical systems by interrupting the flow of electricity when an overload or short circuit occurs. The base cover, often made of durable materials like thermoplastics or thermosetting resins, encases the internal components of the MCCB, protecting them from external factors such as dust, moisture, and physical damage. Furthermore, it also aids in the thermal management of the circuit breaker by dissipating heat generated during operation. This makes the MCCB base cover an essential part of the overall design, contributing to the breaker’s longevity and reliability. Manufacturing Process: The production of MCCB base cover parts involves a series of precise and intricate steps to ensure the final product meets the required standards. The process typically includes: Material Selection:Manufacturers carefully choose materials that exhibit high thermal resistance, mechanical strength, and resistance to environmental factors. Thermoplastic materials like polycarbonate or ABS (Acrylonitrile Butadiene Styrene) and thermosetting resins like epoxy are commonly employed due to their favorable characteristics. Injection Molding:Injection molding is the predominant technique for creating MCCB base covers. It involves melting the chosen material and injecting it into a mold cavity with the desired shape and dimensions. Once cooled and solidified, the cover is removed from the mold, often requiring secondary operations like trimming and finishing. Surface Treatment:Post-molding, the base covers might undergo surface treatments such as painting, coating, or texturing. These treatments enhance the cover’s aesthetics, protection against UV radiation, and resistance to environmental degradation. Quality Control:Rigorous quality checks are conducted at various stages of manufacturing to ensure dimensional accuracy, material integrity, and adherence to safety standards. This involves inspections, measurements, and functional tests to guarantee that the MCCB base covers perform effectively in demanding operational conditions. Contributions to Modern Electrical Systems: MCCB base cover parts manufacturers play a significant role in shaping the landscape of modern electrical systems. Their commitment to producing high-quality, reliable base covers contributes to the overall safety and performance of circuit breakers. These components are not only used in industrial settings but also in residential and commercial installations, ensuring the protection of both property and human life. The use of advanced materials and precision manufacturing techniques results in base covers that can withstand harsh conditions and enable the efficient functioning of electrical networks. Conclusion: The realm of MCCB base cover parts manufacturers is one that intertwines engineering precision with material science to create components that form the backbone of electrical safety and efficiency. These manufacturers provide the foundation upon which modern electrical systems operate, enhancing their reliability and longevity. As technology advances and demands for energy distribution evolve, the contributions of MCCB base cover parts manufacturers remain crucial, continually driving the progress of the electrical industry towards safer and more effective solutions.
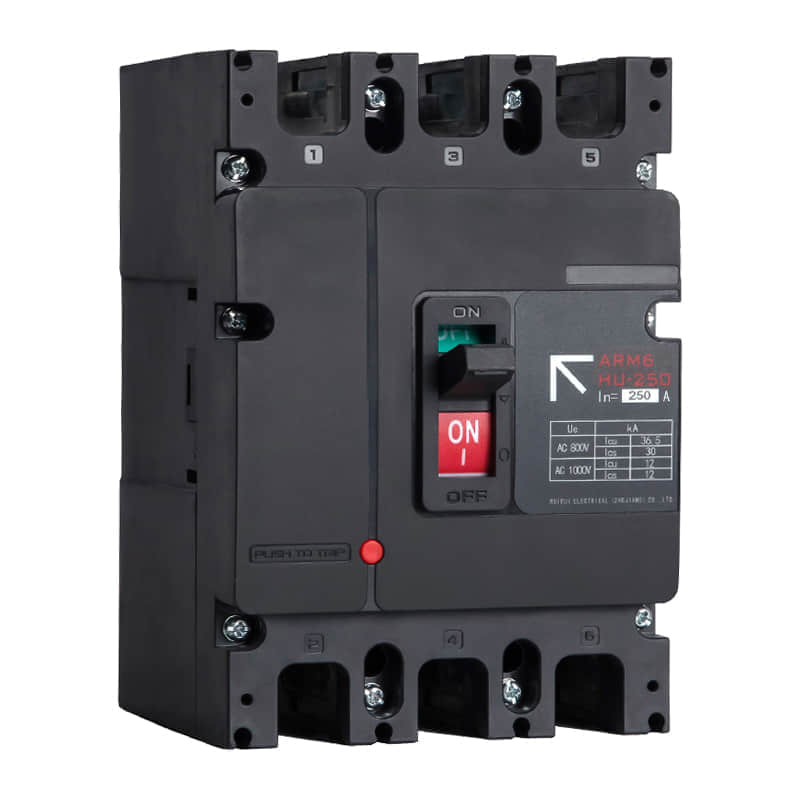