Introduction
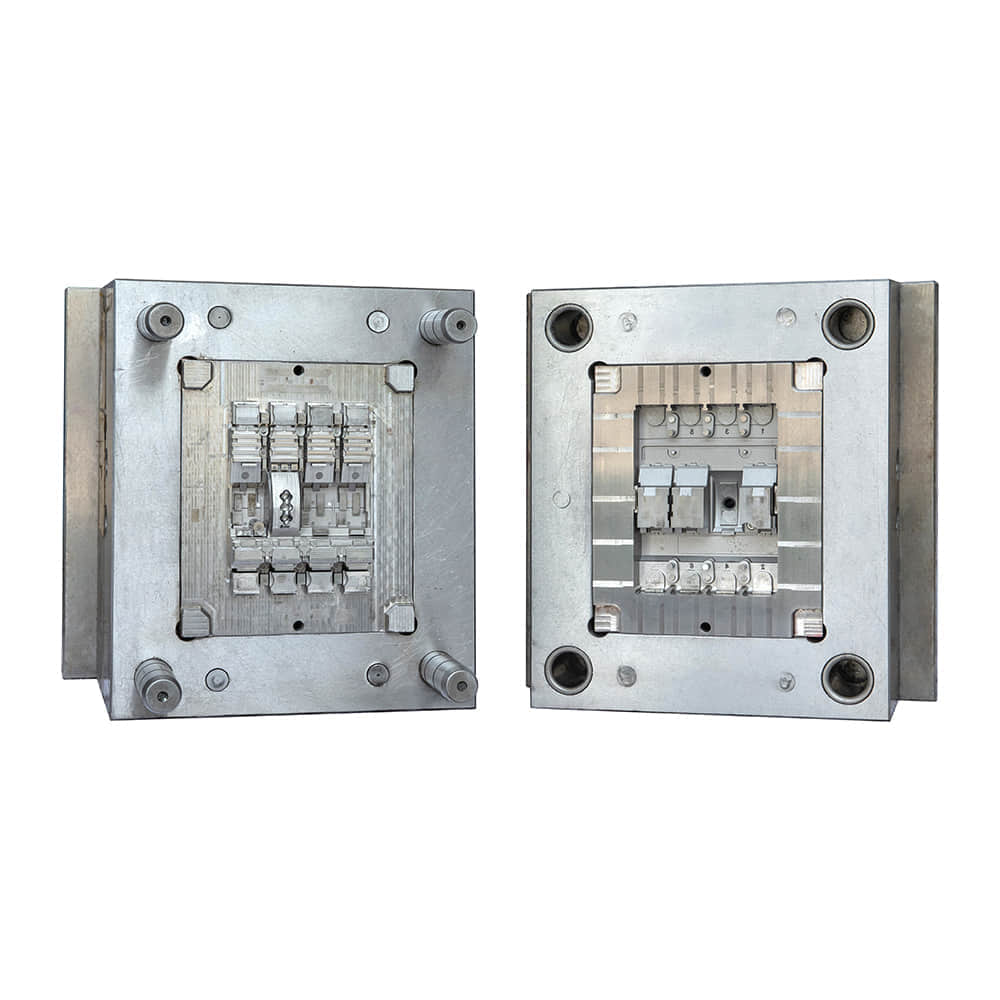
In the dynamic world of manufacturing, innovation is a driving force that continually reshapes industries. One such innovation that has revolutionized the production process is thermoplastic injection molding. This versatile technique has gained prominence due to its ability to create complex shapes with precision and efficiency. This article delves into the advancements and applications of thermoplastic injection molds, highlighting their significance in modern manufacturing.
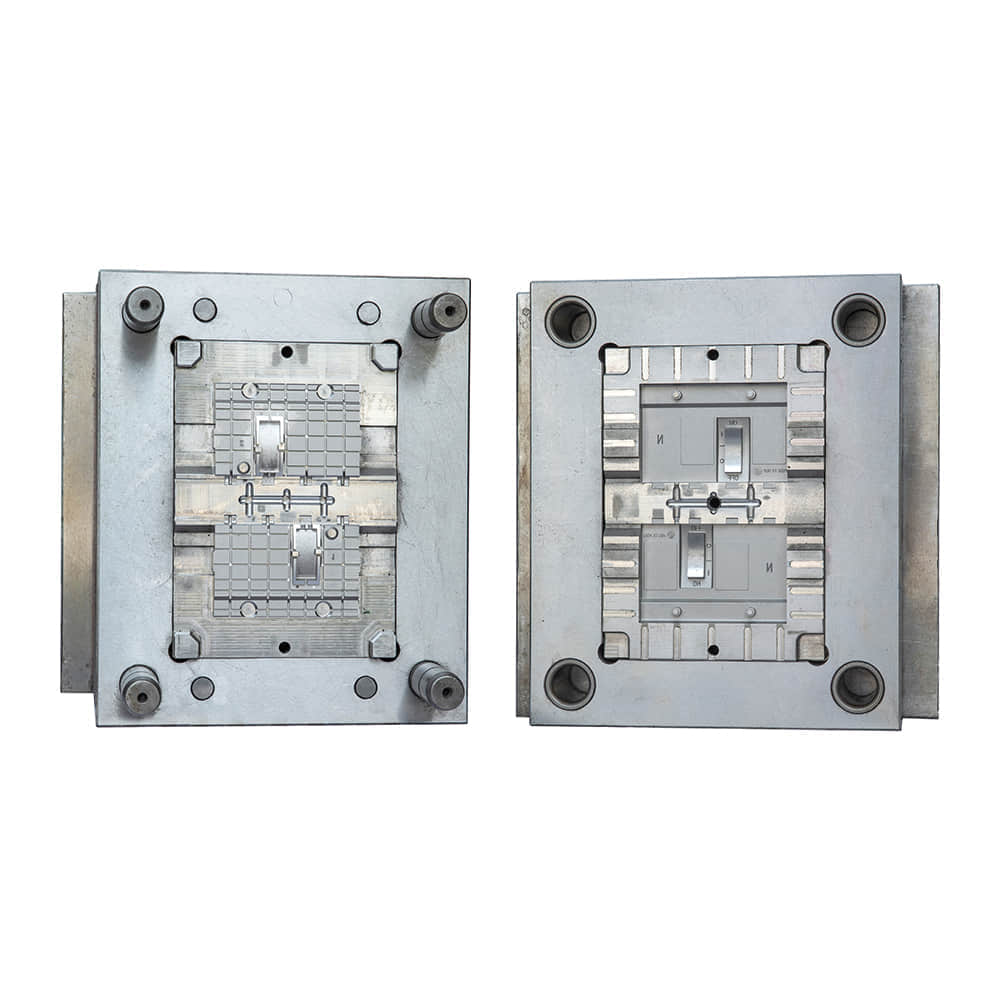
The Evolution of Thermoplastic Injection Molds Thermoplastic injection molding has a rich history, dating back to the late 19th century. Over the years, technological advancements have refined the process, making it an indispensable tool in various industries. Traditional molds were limited in terms of design complexity and material options. However, contemporary molds are crafted with meticulous precision, utilizing computer-aided design (CAD) and computer-aided manufacturing (CAM) technologies. This evolution has expanded the possibilities of thermoplastic injection molding, enabling the production of intricate parts that were once deemed unattainable. Advancements in Material Compatibility One of the remarkable aspects of thermoplastic injection molds is their compatibility with a wide range of materials. Initially restricted to a handful of plastics, today’s molds accommodate an extensive array of thermoplastics, each possessing distinct properties. Engineers can select materials based on factors such as strength, flexibility, chemical resistance, and heat tolerance. This versatility has led to the creation of products that can endure diverse environments, from medical devices to automotive components. Precision Engineering and Reduced Waste Modern manufacturing demands precision, and thermoplastic injection molds deliver exactly that. The intricate design capabilities, coupled with advanced molding machines, result in high-quality products that adhere to tight tolerances. This precision not only ensures product consistency but also reduces waste by minimizing defects and rejects. The efficiency of the process, combined with the ability to recycle excess material, contributes to a more sustainable manufacturing ecosystem. Complex Geometries and Cost Efficiency Thermoplastic injection molds excel at producing parts with complex geometries. The molds can incorporate undercuts, overhangs, and intricate details, allowing designers to unleash their creativity without compromising functionality. Additionally, the efficiency of the injection molding process translates to cost savings. The rapid cycle times and minimal post-processing requirements make it an economically viable choice for both large-scale production and prototyping. Applications Across Industries The applications of thermoplastic injection molds span numerous industries. In the medical field, these molds are instrumental in crafting precise components for medical devices and equipment. The automotive sector benefits from the molds’ ability to produce lightweight, durable parts that enhance fuel efficiency and safety. Consumer goods, electronics, and packaging industries also rely on thermoplastic injection molds to create products that are ergonomic, functional, and visually appealing. Challenges and Future Prospects While thermoplastic injection molds offer myriad advantages, challenges such as material selection, tooling costs, and design complexities remain. However, ongoing research and technological innovations are addressing these challenges. Additive manufacturing techniques, improved mold materials, and simulation software are paving the way for more efficient and cost-effective mold production. Conclusion Thermoplastic injection molds have transformed the landscape of modern manufacturing. Their evolution from rudimentary tools to sophisticated precision instruments highlights the dynamic nature of innovation. With the ability to accommodate diverse materials, intricate designs, and various industries, these molds continue to shape the products we use daily. As technology advances and challenges are overcome, the future of thermoplastic injection molds looks promising, promising even greater precision, efficiency, and sustainability in manufacturing processes.
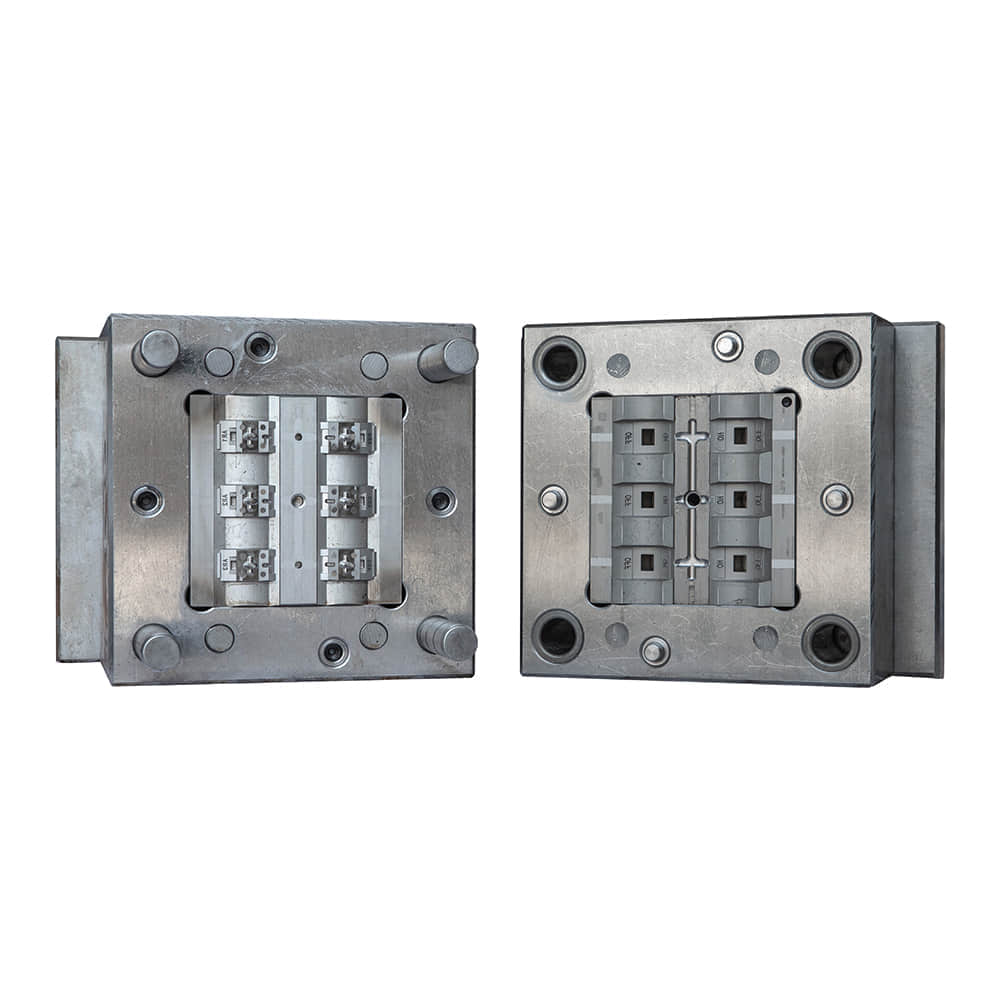