In the realm of industrial automation, the pneumatic actuator stands as a pivotal component, enabling precise and reliable control over various industrial processes. This article aims to delve into the intricacies of the pneumatic actuator, exploring its working principles, types, applications, and the benefits it brings to modern industrial setups.
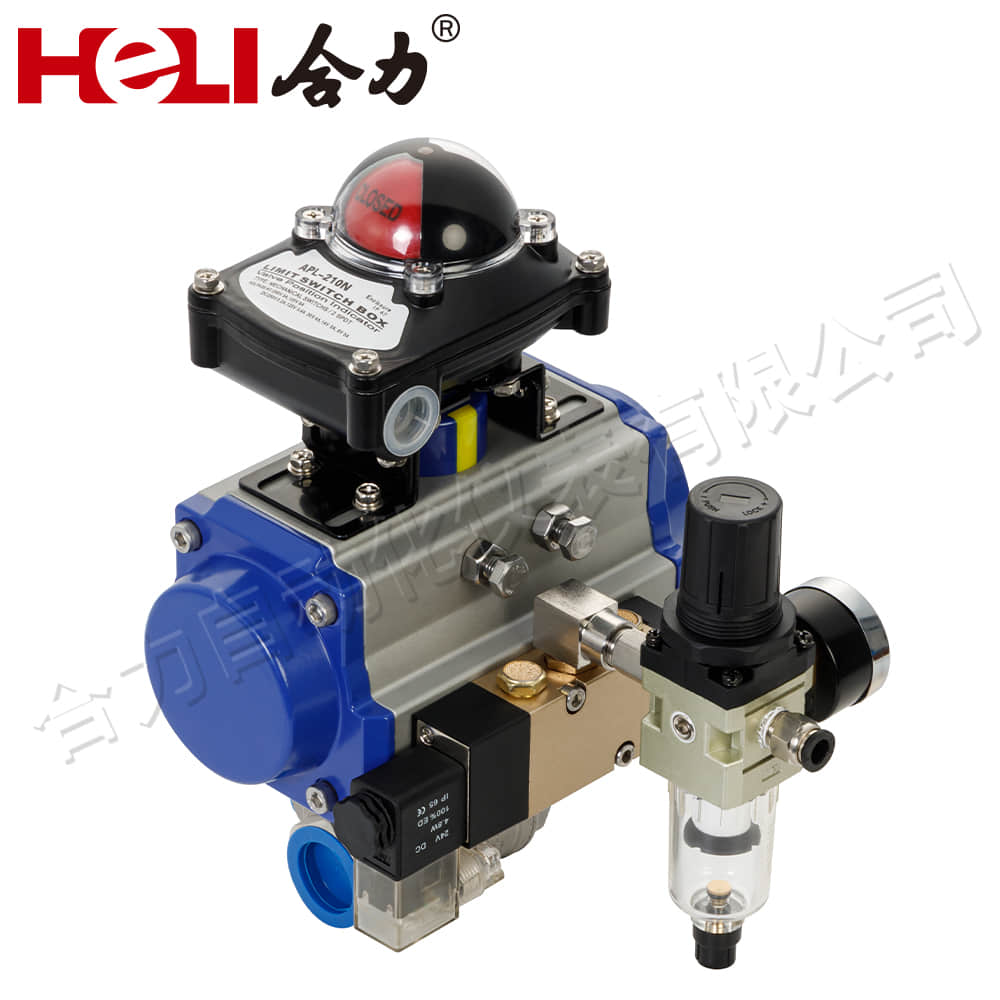
Fundamentally, a pneumatic actuator is a device that converts compressed air or gas into mechanical motion. It operates on the principle of pneumatic power, utilizing the force generated by compressed air to perform tasks such as opening and closing valves, moving levers, or rotating shafts. The key advantage of pneumatic actuators lies in their simplicity, reliability, and speed of response.
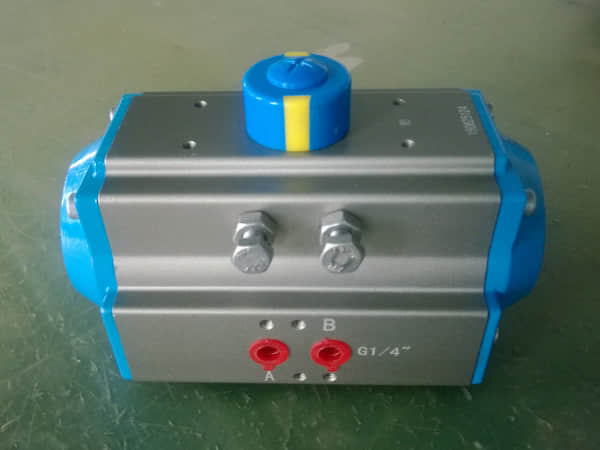
There are several types of pneumatic actuators, each designed for specific applications. The most common types include diaphragm actuators, piston actuators, and rack-and-pinion actuators. Diaphragm actuators are suitable for low-force applications due to their compact design and smooth operation. Piston actuators, on the other hand, offer higher forces and longer strokes, making them ideal for heavier-duty tasks. Rack-and-pinion actuators provide a high torque output, enabling precise control over rotational movements. The working principle of a pneumatic actuator is straightforward. Compressed air is supplied to one or more chambers within the actuator, creating a pressure differential that drives the actuator’s moving parts. The direction of motion is controlled by the routing of the compressed air, typically through the use of valves and solenoids. This system allows for precise and repeatable movements, making pneumatic actuators a reliable choice for automation tasks.
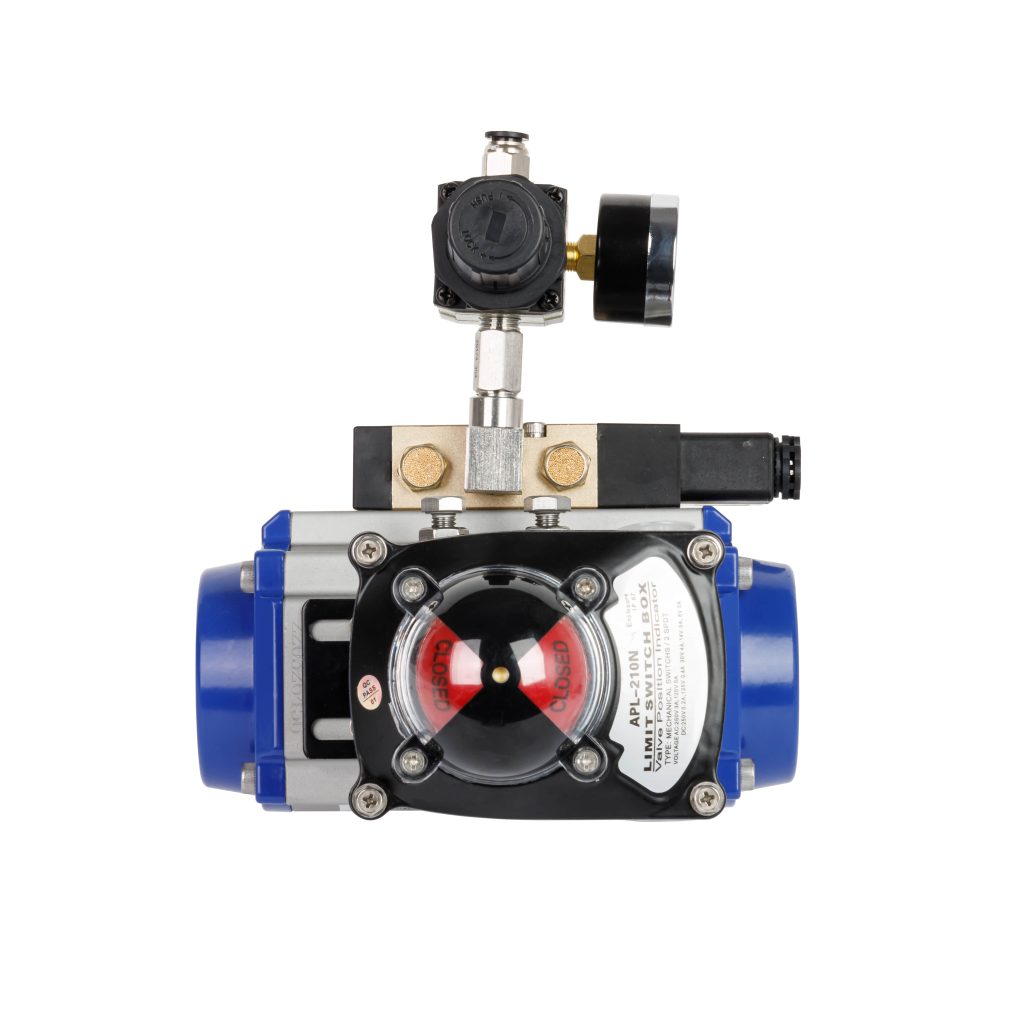