In modern industrial applications, valves play a pivotal role in controlling the flow of fluids, gases, and other substances through pipelines. Among various types of valves, the stainless steel electric three eccentric butterfly valve is increasingly popular due to its superior performance, durability, and adaptability to different conditions. These valves are especially valued in industries such as oil and gas, water treatment, chemical processing, and power generation. Among the leading manufacturers of such advanced systems, Helix Automation stands out for its exceptional innovation and precision engineering, delivering state-of-the-art solutions for automated flow control.
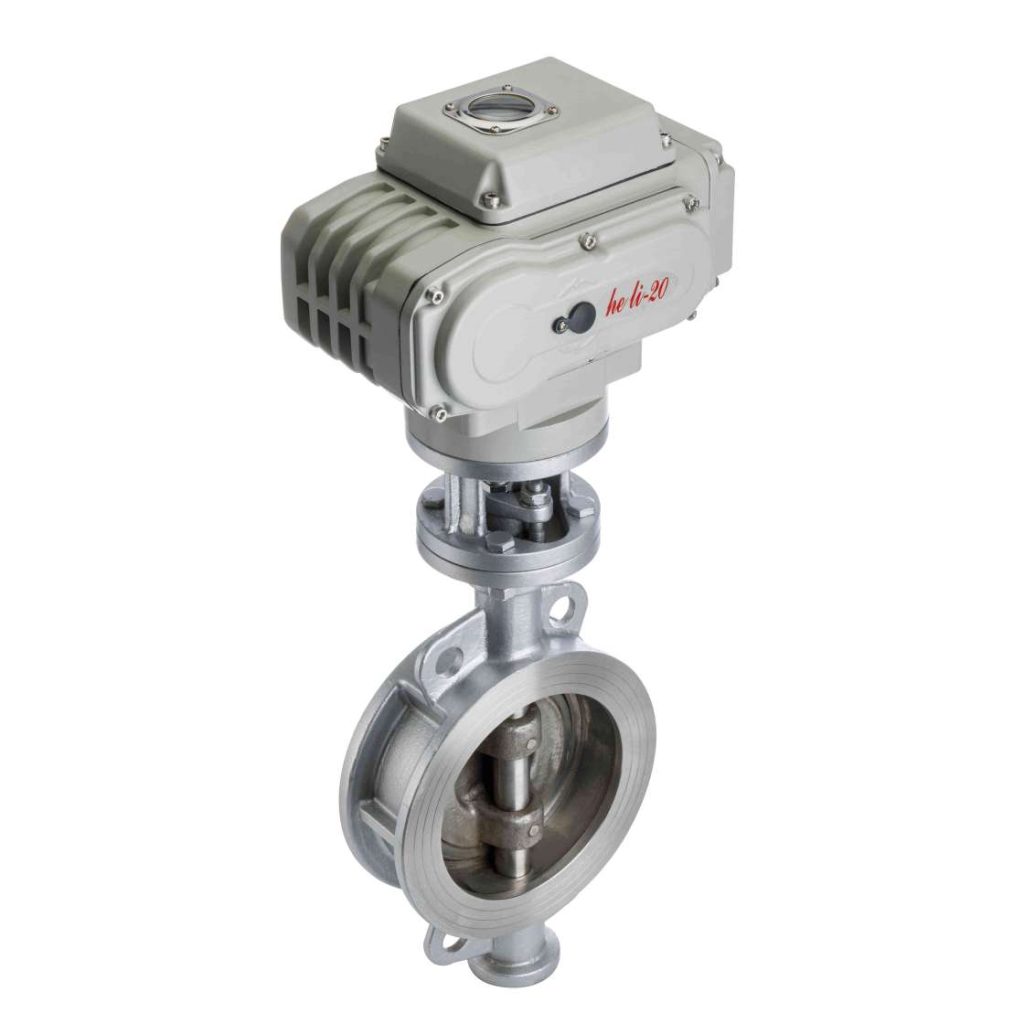
What is a Stainless Steel Electric Three Eccentric Butterfly Valve?
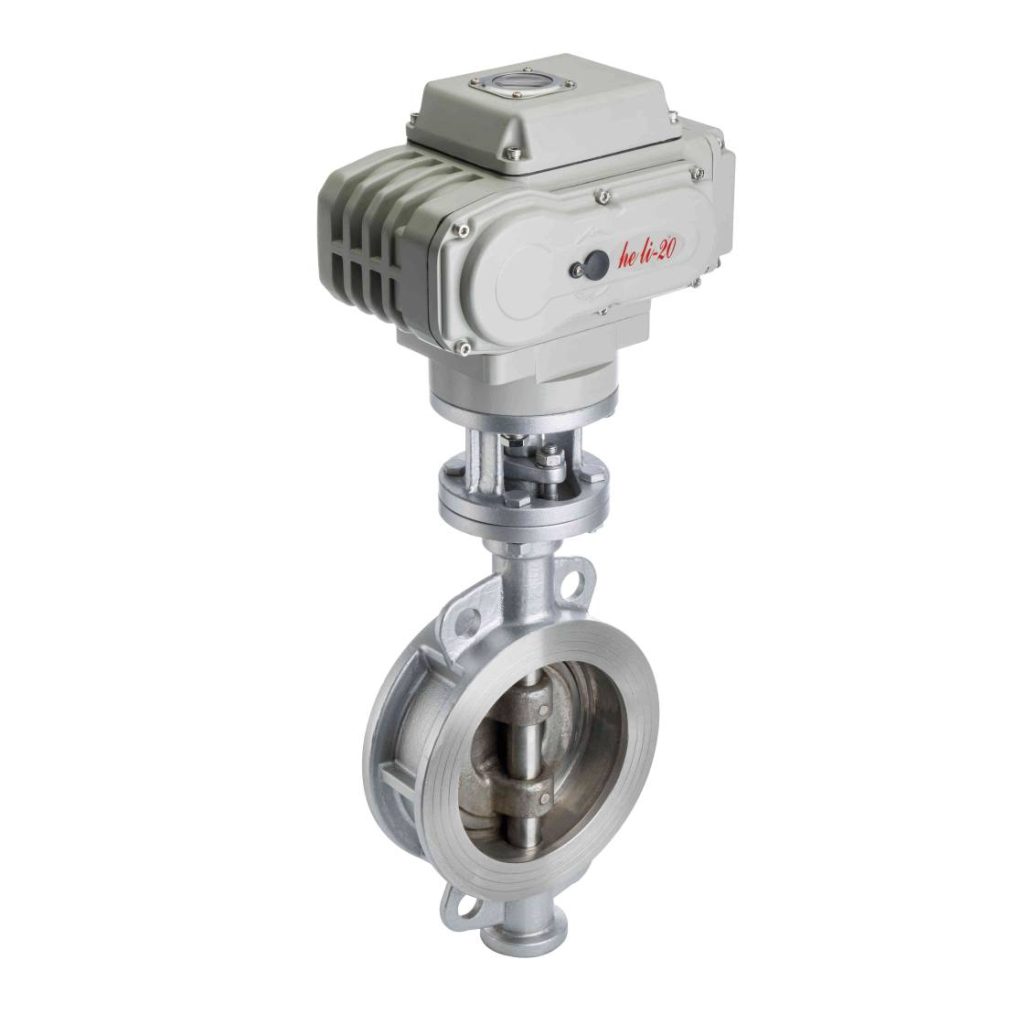
The stainless steel electric three eccentric butterfly valve is a specialized valve designed to regulate the flow of media in pipelines with high efficiency and minimal leakage. The term “three eccentric” refers to the unique design of the valve, which incorporates three offsets in its construction—this includes the offset between the valve stem and the sealing surface, the offset between the centerline of the valve seat and the shaft center, and the third offset in the body of the valve. These three eccentricities make the valve’s sealing action smoother and more reliable, reducing wear and tear, and improving overall performance.
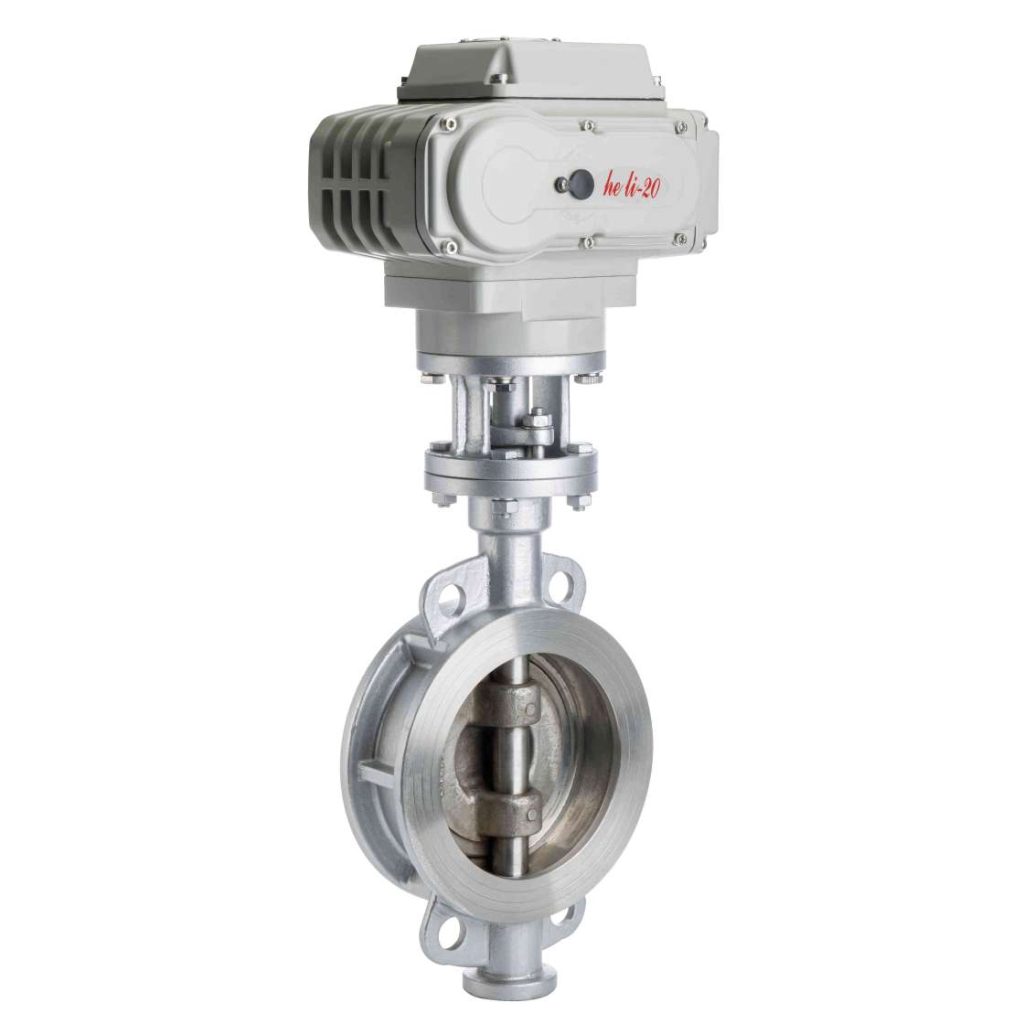