Injection Molded Parts: Precision and Versatility in Manufacturing

In the realm of modern manufacturing, where precision and efficiency are paramount, injection molded parts have emerged as an integral component. This ingenious manufacturing process has revolutionized the production of intricate and functional components across various industries, ranging from automotive to electronics, from healthcare to consumer goods.
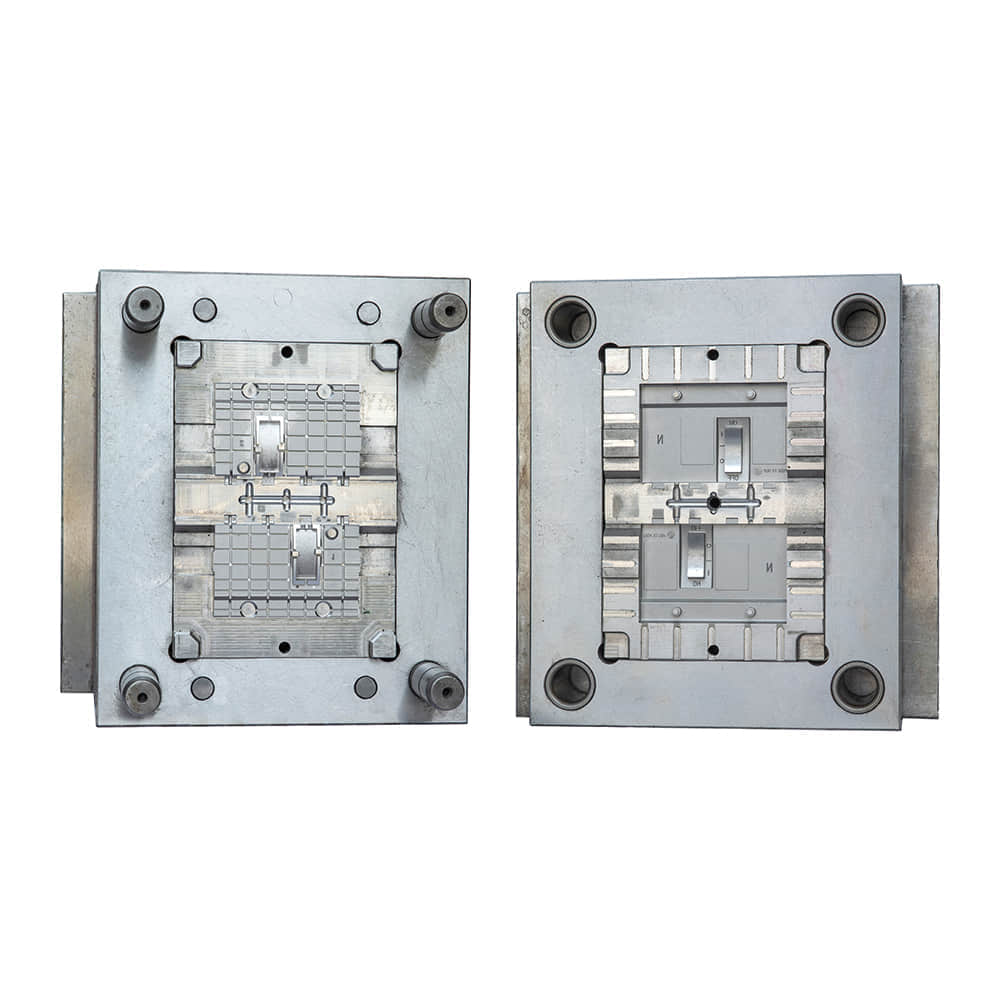
The Injection Molding Process Injection molding is a manufacturing technique that involves injecting molten material, typically plastic polymers, into a mold cavity. Once the material cools and solidifies, the mold is opened, and the finished part is ejected. This process allows for the creation of complex shapes with fine details, making it an ideal choice for producing parts that demand both precision and intricacy. Advantages of Injection Molded Parts Precision and Consistency: Injection molded parts are renowned for their accuracy and consistency. The molds used are precisely crafted, ensuring that each part produced is an exact replica of the design. This level of precision is particularly critical in industries such as aerospace and medical, where even the slightest deviation can have significant consequences. Cost-Efficiency: While the initial tooling and mold creation can be relatively expensive, injection molding proves highly cost-effective in high-volume production runs. The rapid cycle times and minimal post-processing requirements contribute to lower overall production costs over time. Design Flexibility: Injection molding offers unparalleled design flexibility. Engineers and designers can experiment with various shapes, sizes, and materials, all while maintaining the integrity of the final product. Complex geometries that would be challenging to achieve through other methods can be effortlessly realized in injection molded parts. Material Variety: The range of materials available for injection molding is vast, including different types of plastics, elastomers, and even certain metals. This versatility allows manufacturers to choose materials that offer the required mechanical, thermal, and chemical properties for specific applications. Reduced Waste: Modern injection molding processes incorporate advanced technologies to minimize material waste. The closed-loop system ensures that excess material is recycled and reused, contributing to a more sustainable manufacturing process. Applications Across Industries The impact of injection molded parts extends across numerous industries: Automotive: Injection molded parts are found in various automotive components, from intricate interior details to essential under-the-hood parts. Their durability, precision, and cost-effectiveness make them a staple in this industry. Electronics: The electronics sector benefits from injection molded parts in the production of casings, connectors, and other intricate components. The ability to incorporate features such as snap fits and intricate cable routing directly into the design is a significant advantage. Medical: In the medical field, where precision and hygiene are paramount, injection molded parts are integral to the production of devices, equipment housings, and disposable items. Consumer Goods: Injection molding is behind the seamless and polished look of many everyday items, from packaging to toys, offering manufacturers the ability to produce consistent, high-quality products. Challenges and Future Prospects Despite its many advantages, injection molding does face challenges. Designing intricate molds can be time-consuming and expensive, especially for prototypes or low-volume runs. Additionally, some materials may have limitations in terms of heat resistance, chemical resistance, or other specific properties. Looking ahead, advancements in material science, mold-making techniques, and automation are set to further enhance the injection molding process. 3D printing technologies are being integrated into mold-making, reducing lead times and allowing for more complex mold designs. Furthermore, the industry’s increased emphasis on sustainability is driving the development of bio-based and recycled materials suitable for injection molding. Conclusion Injection molded parts have undoubtedly transformed the landscape of modern manufacturing. Their precision, versatility, and wide-ranging applications make them a cornerstone of industries around the world. As technology continues to evolve, injection molding is poised to retain its significance, offering a harmonious blend of accuracy, efficiency, and innovation.
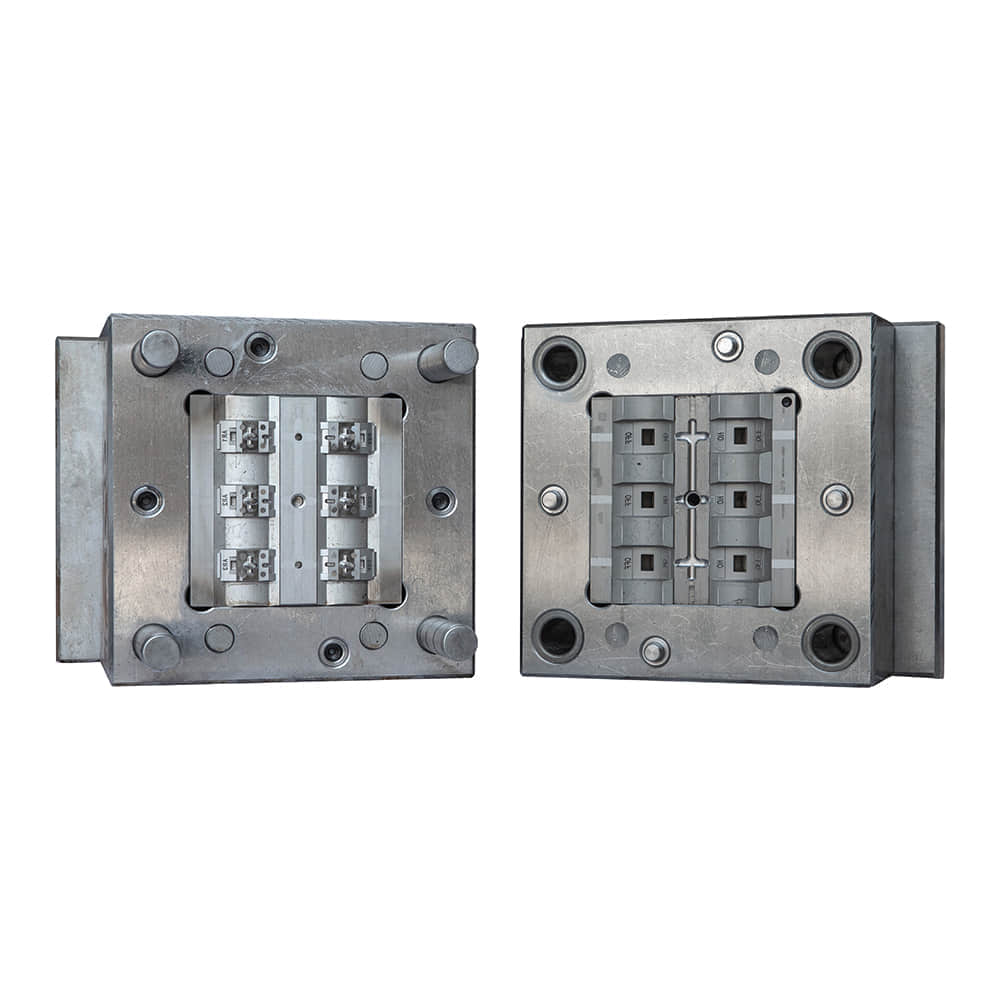