Blanking Dies: The Cornerstone of Precision Manufacturing
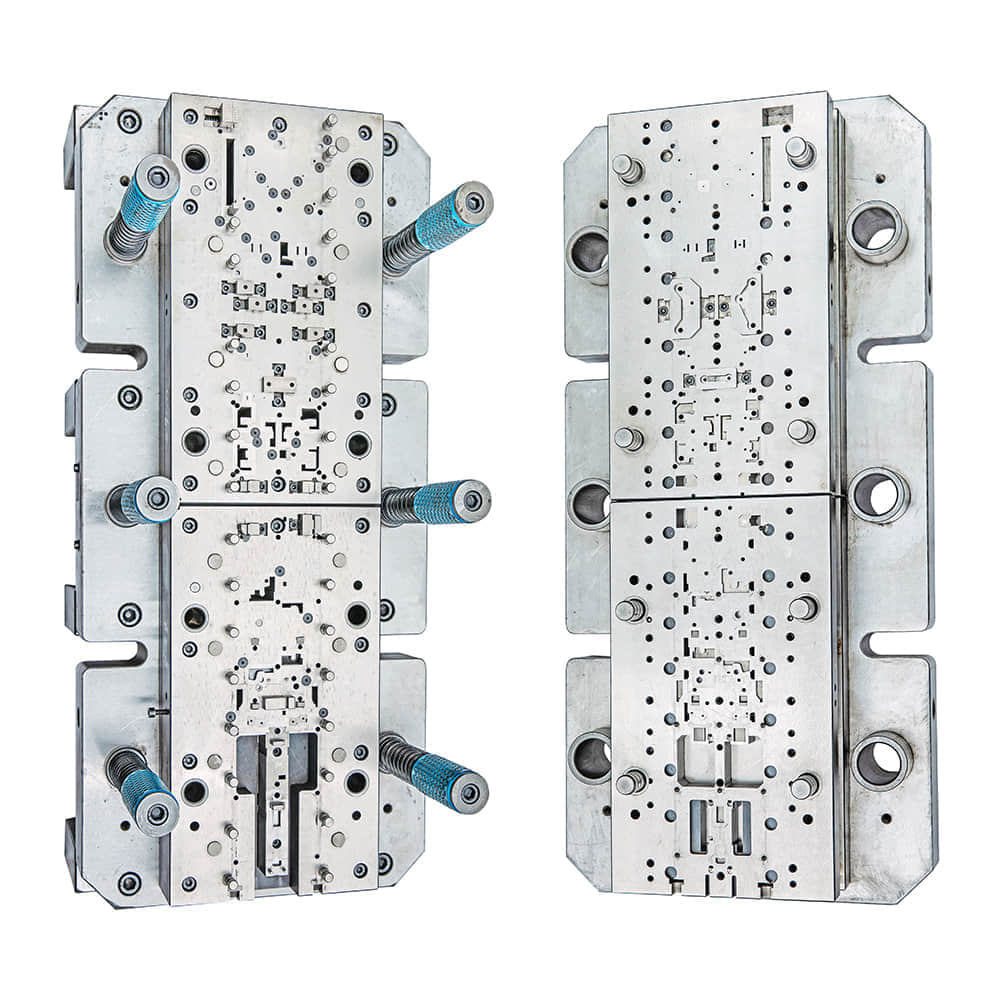
In the realm of precision manufacturing, where every millimeter matters and quality reigns supreme, the role of blanking dies cannot be overstated. These unassuming tools are the unsung heroes behind the creation of countless intricate metal and non-metal components that form the backbone of modern industries. In this article, we will delve into the world of blanking dies, exploring their types, functions, and the pivotal role they play in shaping the products we rely on daily.
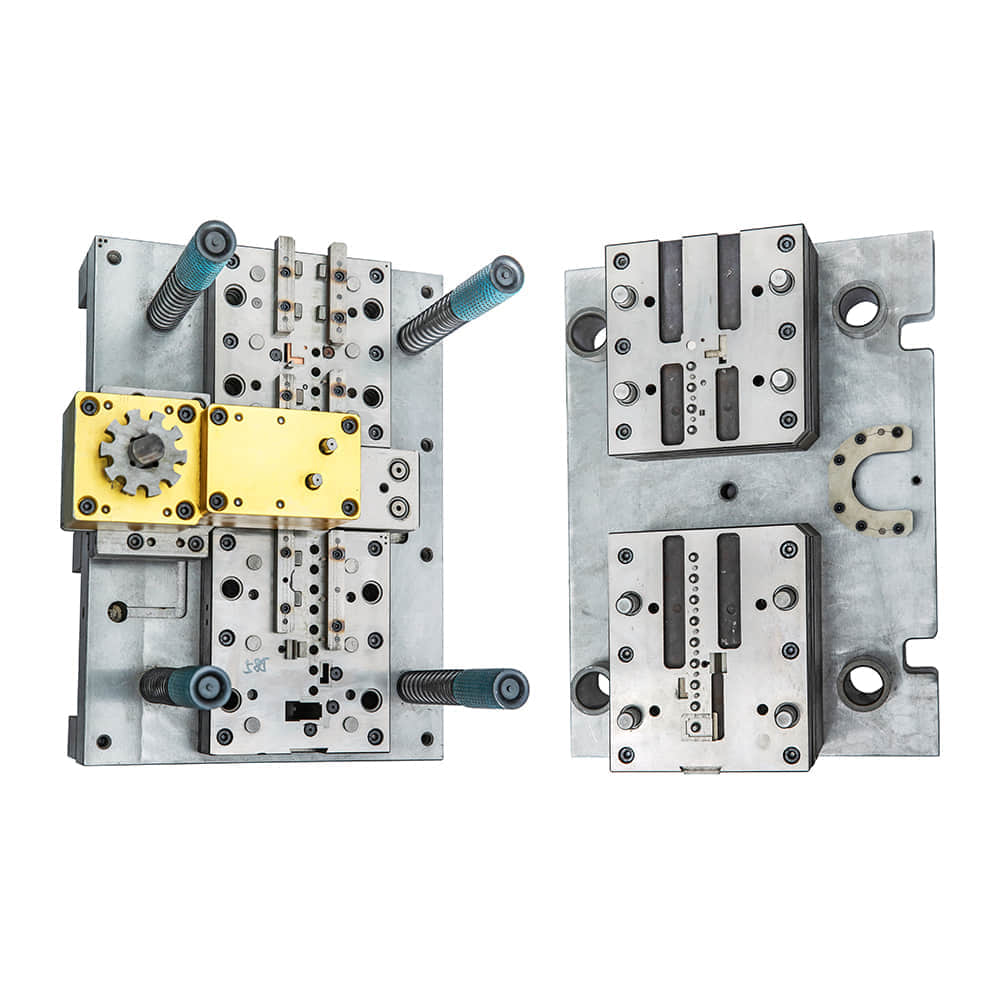
What Are Blanking Dies? Blanking dies are specialized cutting tools used in metalworking and other industries to precisely cut and shape raw materials into specific forms, often referred to as “blanks.” These blanks serve as the building blocks for various products, from automobile components and electronics to kitchen appliances and medical devices. Blanking dies are typically made of high-strength steel and come in a variety of shapes and sizes to accommodate diverse manufacturing needs. Types of Blanking Dies Shearing Blanks: Shearing blanks are one of the most common types of blanking dies. They employ a straightforward cutting process, where a sharp-edged punch descends onto the material, forcing it through the die cavity to create the desired blank. This process is highly efficient for producing simple shapes and is widely used in mass production. Piercing Blanks: Piercing blanks are used when intricate internal cutouts or holes are required within the blank. The punch, in this case, features a cutout or a protruding shape that corresponds to the desired hole or internal feature. As the punch descends, it pierces through the material, creating the blank with the necessary internal features. Notching Blanks: Notching blanks are used to create notches or tabs in the material. These notches are often used for interlocking components or creating structural features. Notching dies have a punch and die cavity specifically designed for cutting out these shapes with precision. Compound Blanking Dies: Compound blanking dies are a versatile type that combines multiple cutting operations into a single die set. They can simultaneously cut, pierce, and notch the material, streamlining the production process and increasing efficiency. The Function of Blanking Dies The primary function of blanking dies is to transform a flat sheet or coil of material into a precise blank with the required shape and dimensions. This blank can then be further processed or assembled to create finished products. Here’s a simplified overview of the blanking process: Material Feeding: The raw material, usually in the form of a sheet or coil, is fed into the blanking press. Die Alignment: The blanking die and the material are precisely aligned to ensure accurate cutting. Cutting Operation: When the press is activated, the punch descends into the die cavity, cutting the material into the desired shape. Blank Removal: The freshly cut blank is removed from the die, often with the help of automated systems. The Importance of Precision One of the key attributes of blanking dies is their ability to consistently produce blanks with high precision. In industries where tight tolerances are critical, such as aerospace and medical manufacturing, even the slightest deviation can lead to product failure. Blank dies are engineered with meticulous attention to detail, and they are routinely maintained and inspected to ensure they meet the strictest quality standards. Conclusion Blanking dies are the unsung heroes of precision manufacturing. They take raw materials and transform them into the precise blanks that form the basis of countless products. From simple shearing to complex compound operations, these dies are versatile tools that enable the creation of intricate components with the utmost precision. In a world where quality and precision are paramount, blanking dies are the cornerstones of modern manufacturing.
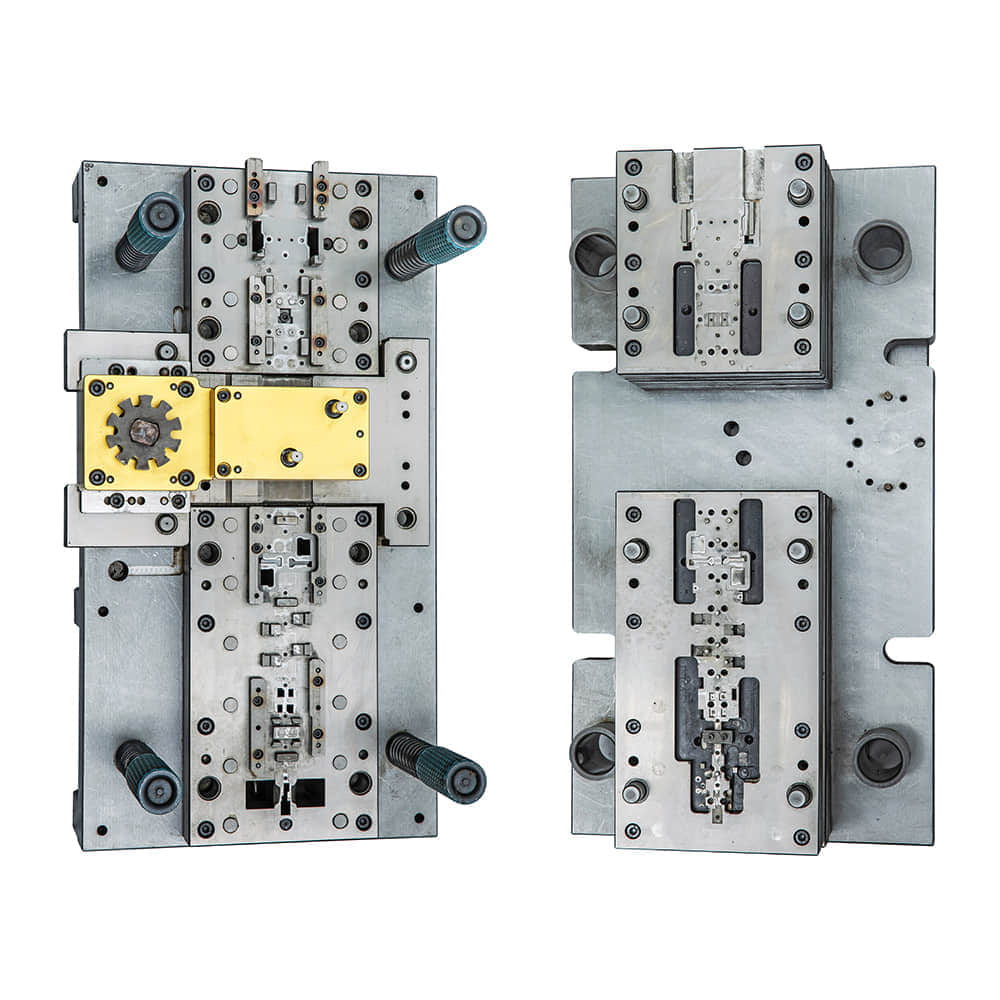