Introduction
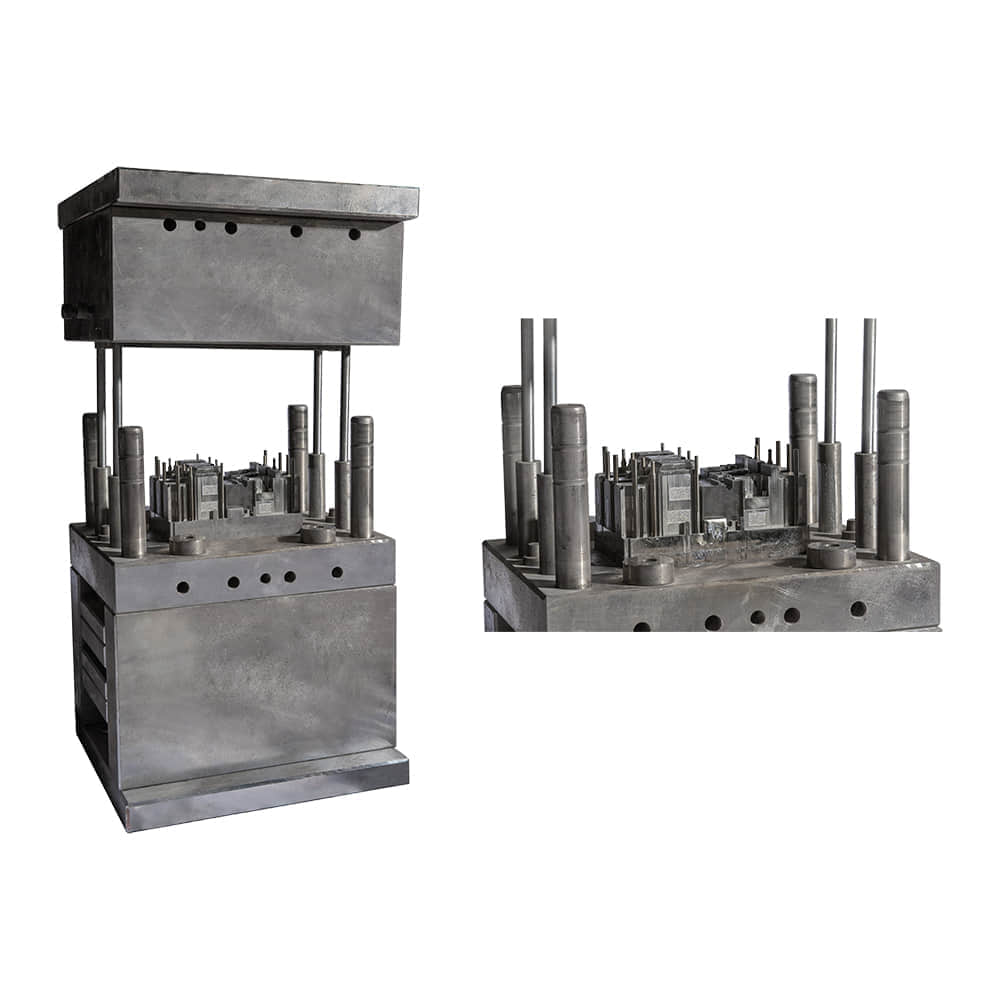
In the realm of modern manufacturing, innovative technologies continue to reshape industries, enhancing both efficiency and precision. One such groundbreaking advancement is the development of Direct Metal Casting (DMC) injection technology. This cutting-edge technique has revolutionized the way metal components are produced, offering unparalleled benefits to various sectors.
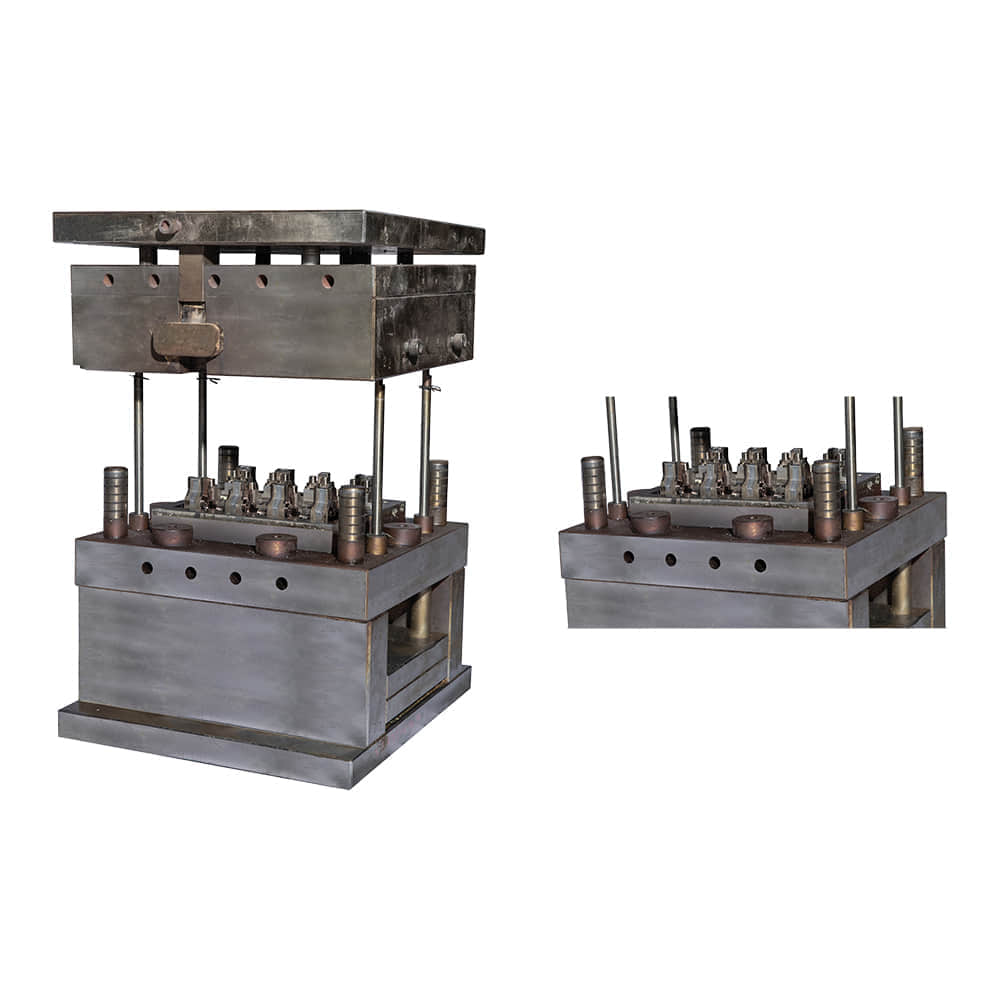
The Essence of DMC Injection DMC injection, a fusion of additive manufacturing and traditional casting, has emerged as a powerful technique for fabricating intricate metal parts with extraordinary precision. Unlike conventional casting methods, DMC injection relies on the controlled injection of molten metal into molds, bringing unprecedented intricacy to designs. This process facilitates the production of components with intricate geometries and internal structures that were once deemed unfeasible. Advantages over Conventional Manufacturing Complex Geometry Realization: One of the primary advantages of DMC injection is its ability to produce parts with complex geometries. Traditional manufacturing methods often struggle with intricate designs, leading to the compromise of part functionality. DMC injection eliminates such constraints, enabling the realization of highly intricate components with fine details and internal features. Reduced Material Waste: Traditional manufacturing methods often result in significant material wastage due to subtractive processes. DMC injection, on the other hand, follows an additive approach, adding material only where necessary. This reduction in material waste not only contributes to cost savings but also aligns with sustainable manufacturing practices. Enhanced Mechanical Properties: DMC injection technology allows for precise control over the microstructure of the produced parts. This controlled microstructure leads to enhanced mechanical properties, such as improved strength, durability, and thermal resistance. Industries like aerospace and automotive benefit greatly from components with superior performance characteristics. Shortened Lead Times: The integration of computer-aided design (CAD) and computer-aided manufacturing (CAM) in DMC injection expedites the design-to-production timeline. Rapid prototyping and reduced setup times mean that companies can bring products to market faster, gaining a competitive edge in today’s fast-paced business environment. Applications Across Industries Aerospace: The aerospace industry demands lightweight yet robust components. DMC injection allows the creation of intricate, high-strength parts that meet these criteria. From turbine blades to structural elements, DMC injection contributes to improved fuel efficiency and overall performance. Medical: In the medical field, precision and customization are paramount. DMC injection enables the fabrication of patient-specific implants and medical devices with complex geometries, enhancing both comfort and functionality. Automotive: Automotive manufacturers leverage DMC injection to produce lightweight, high-performance parts that enhance vehicle efficiency and safety. From engine components to chassis elements, DMC injection’s benefits are wide-ranging. Conclusion The advent of DMC injection technology marks a significant milestone in modern manufacturing. Its ability to combine intricate design possibilities with enhanced material properties and reduced lead times has transformed the landscape of various industries. As this technology continues to evolve, we can anticipate even more innovative applications and a future where complex metal components are limited only by the bounds of imagination.
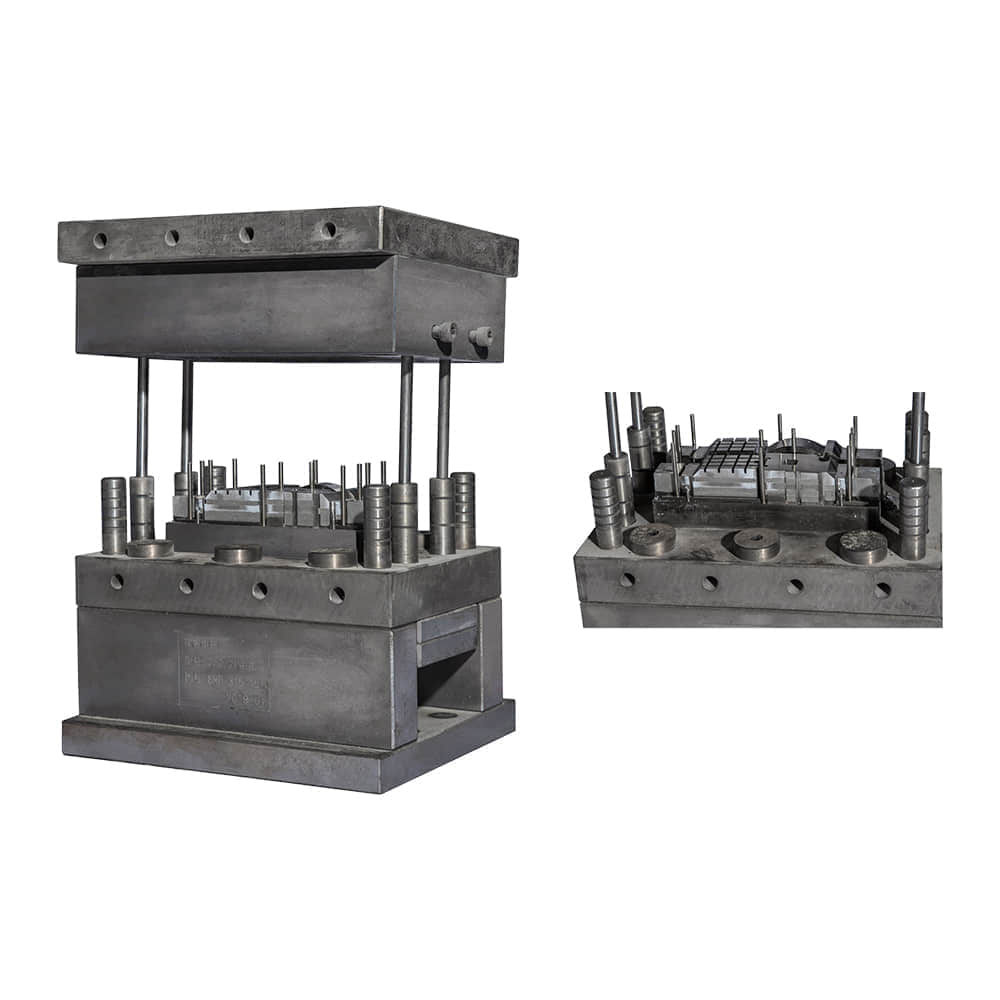