In the ever-evolving landscape of manufacturing, innovative techniques continually emerge, reshaping industries and enhancing production processes. Sheet Molding Compound (SMC) molding is one such revolutionary method that has garnered significant attention for its remarkable advantages. SMC molding combines versatility, cost-efficiency, and environmental consciousness, making it a preferred choice for many manufacturers across the globe.
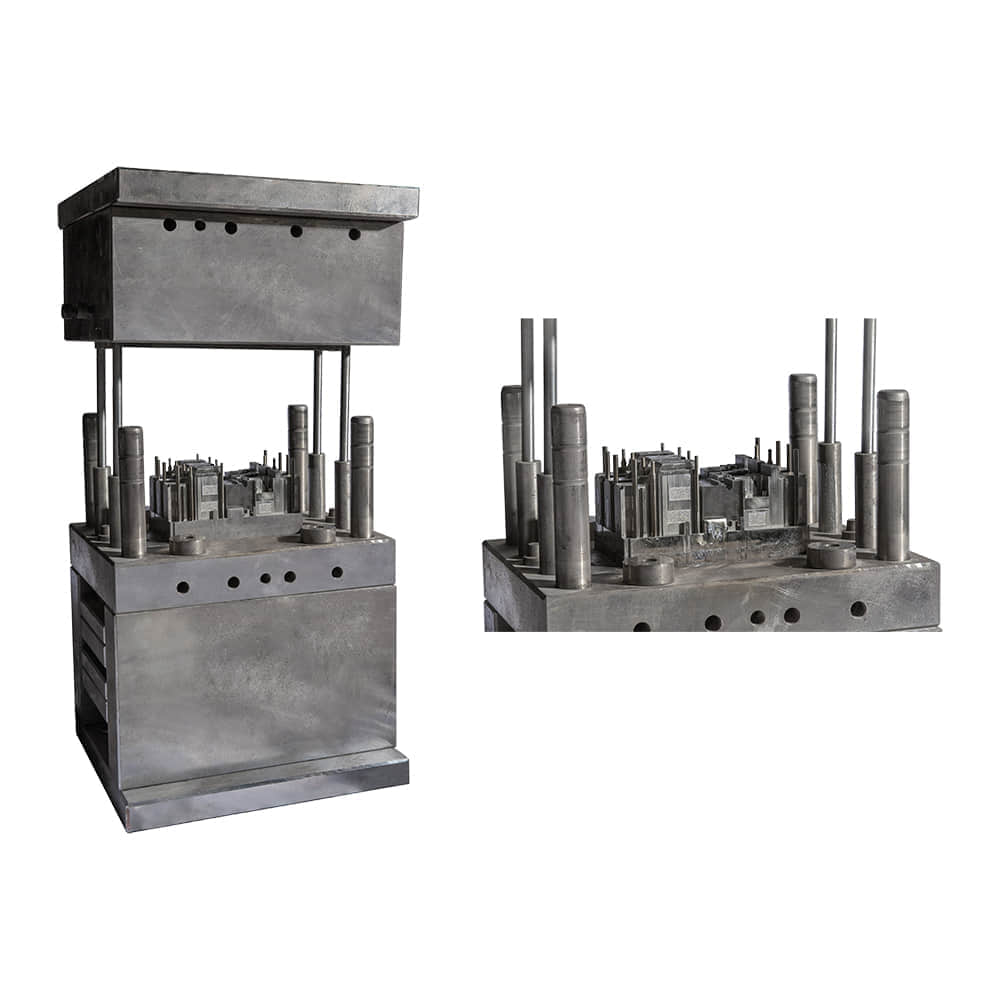
SMC molding involves the creation of composite materials by compressing and curing various components, including resins, fibers, and additives. The resulting SMC sheets are highly moldable and can be shaped into intricate forms with precision. This inherent versatility opens doors to countless design possibilities, enabling the creation of complex parts and products that would be otherwise challenging to produce using traditional methods.
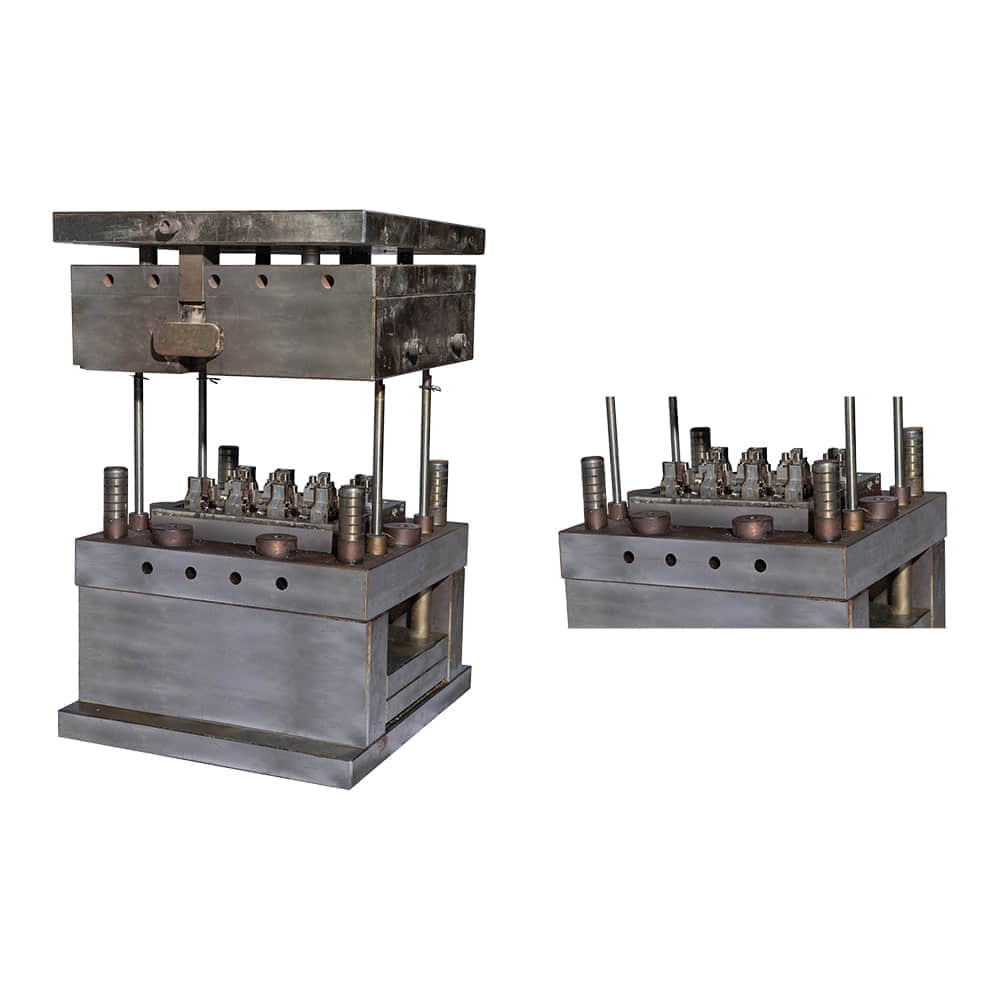
One of the most significant advantages of SMC molding is its cost-effectiveness. The efficient process of creating SMC sheets, along with the ability to mold large and intricate parts in a single step, drastically reduces labor and production costs. Additionally, the minimal material waste generated during the molding process contributes to overall cost savings, making SMC molding financially viable for both small-scale manufacturers and large industrial operations. Environmental sustainability is a paramount concern in modern manufacturing, and SMC molding aligns perfectly with this ethos. The process generates little waste, as excess material can be easily recycled and used for future SMC production. Moreover, the lightweight nature of SMC products translates to reduced energy consumption during transportation and usage. As a result, manufacturers can significantly lower their carbon footprint and contribute to a more sustainable future. The exceptional mechanical properties of SMC-molded products further demonstrate the technique’s superiority. SMC materials exhibit high strength, excellent dimensional stability, and resistance to corrosion, making them ideal for a wide range of applications across industries. From automotive components to electrical enclosures, and from construction panels to consumer goods, SMC-molded products consistently outperform their counterparts made through traditional methods. The inherent design freedom offered by SMC molding is a game-changer for industries that demand intricate and customized products. Manufacturers can craft parts with varying thicknesses, complex geometries, and integrated features, all in a single molding process. This eliminates the need for secondary operations and assembly, streamlining the production timeline and enhancing product consistency. Furthermore, SMC molding’s ability to efficiently integrate functional elements into the product during the molding process is a key advantage. This not only reduces assembly requirements but also ensures better precision and reliability in the final product. Such integrated features can include threaded inserts, fastening points, and mounting bosses, enhancing the usability and durability of the end product. In conclusion, Sheet Molding Compound (SMC) molding stands as a testament to the constant evolution of manufacturing techniques. Its versatility, cost-effectiveness, and eco-friendly characteristics make it a compelling choice for manufacturers looking to optimize their production processes and contribute to sustainable practices. As industries continue to embrace innovation, SMC molding is at the forefront, reshaping the way we create intricate, durable, and customized products for a wide array of applications.
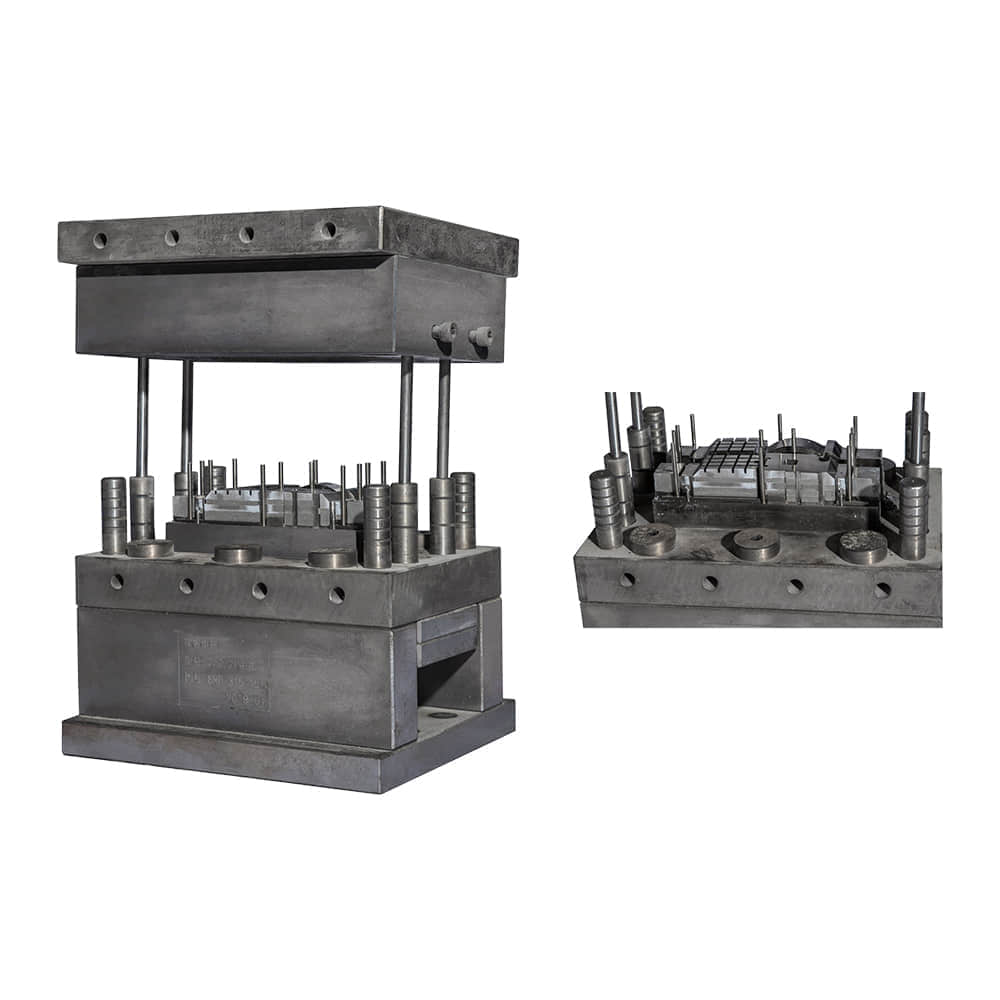