In modern electrical systems, relays are indispensable components used to control circuits by opening and closing contacts in response to electrical signals. However, a critical issue that arises in relay operation is the phenomenon of contact welding, which occurs when the relay’s contact points experience excessive heat due to high electrical currents. This issue can significantly affect the performance, reliability, and lifespan of the relay. Power Relay Contact Welding Solutions aim to mitigate these challenges by focusing on strategies to reduce or prevent welding and damage to contact points. This article explores the root causes of contact welding, its consequences, and potential solutions to improve relay performance.
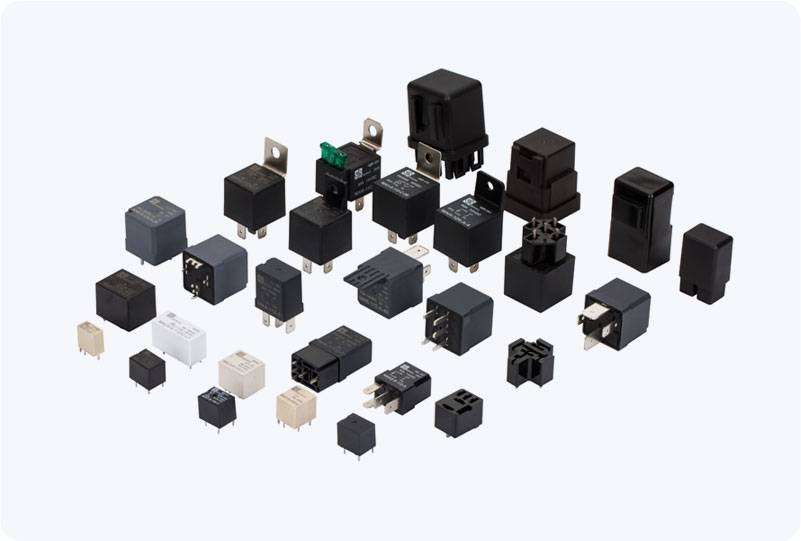
The Root Causes of Power Relay Contact Welding High Electrical Current: One of the most common causes of contact welding is when a relay operates under high electrical currents. When the current passing through the contacts exceeds their rated capacity, the excessive heat generated can cause the contact surfaces to melt and fuse together. This is particularly problematic in relays used in high-power circuits or those that handle large electrical loads. Arc Formation: Another contributing factor is the formation of an electric arc when the contacts separate. As the contacts open, if the current is still flowing, it can create an electric arc between the contacts. The arc produces extreme temperatures that can damage or weld the