Power relays play a critical role in various electrical systems by controlling the flow of electricity between different components. These relays are integral to the proper functioning of devices ranging from industrial machinery to household appliances. However, one of the most significant issues encountered in power relays is contact welding, which can lead to system failures and reduce the overall lifespan of the relay. In this article, we will explore the causes of contact welding in power relays and present solutions to prevent this issue, ensuring reliable and long-lasting performance.
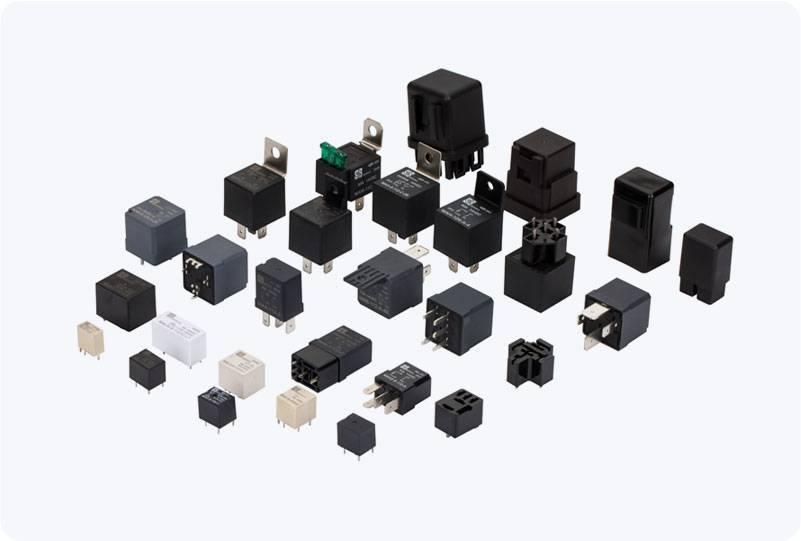
Understanding Contact Welding in Power Relays Contact welding in a power relay occurs when the relay’s electrical contacts become fused together due to excessive heat generated by high current or electrical arcing. This can happen when the contacts are subjected to conditions beyond their rated capacity, causing the metal surfaces to adhere to one another. Once welded, the contacts are unable to open or close properly, which can result in the failure of the relay and the connected system. This problem is particularly prevalent in high-power applications, where large currents are involved. The continuous cycling of the relay between open and closed states, combined with the electrical arcing that occurs during these transitions, can further exacerbate the issue of contact welding. In some cases, the welding can be so severe that the relay is permanently damaged, necessitating costly replacements.