In today’s highly demanding industrial landscape, ensuring long-lasting and efficient operation of critical systems is paramount. For industries dealing with aggressive chemicals, high temperatures, and extreme pressures, the need for durable, reliable valves is essential. Among the most effective solutions to address these challenges are electric anti-corrosion ball valves, which are widely used in various sectors such as chemical processing, water treatment, oil and gas, and power generation. This article delves into the role of electric anti-corrosion ball valves, their benefits, and why manufacturers in this field are integral to industrial success.
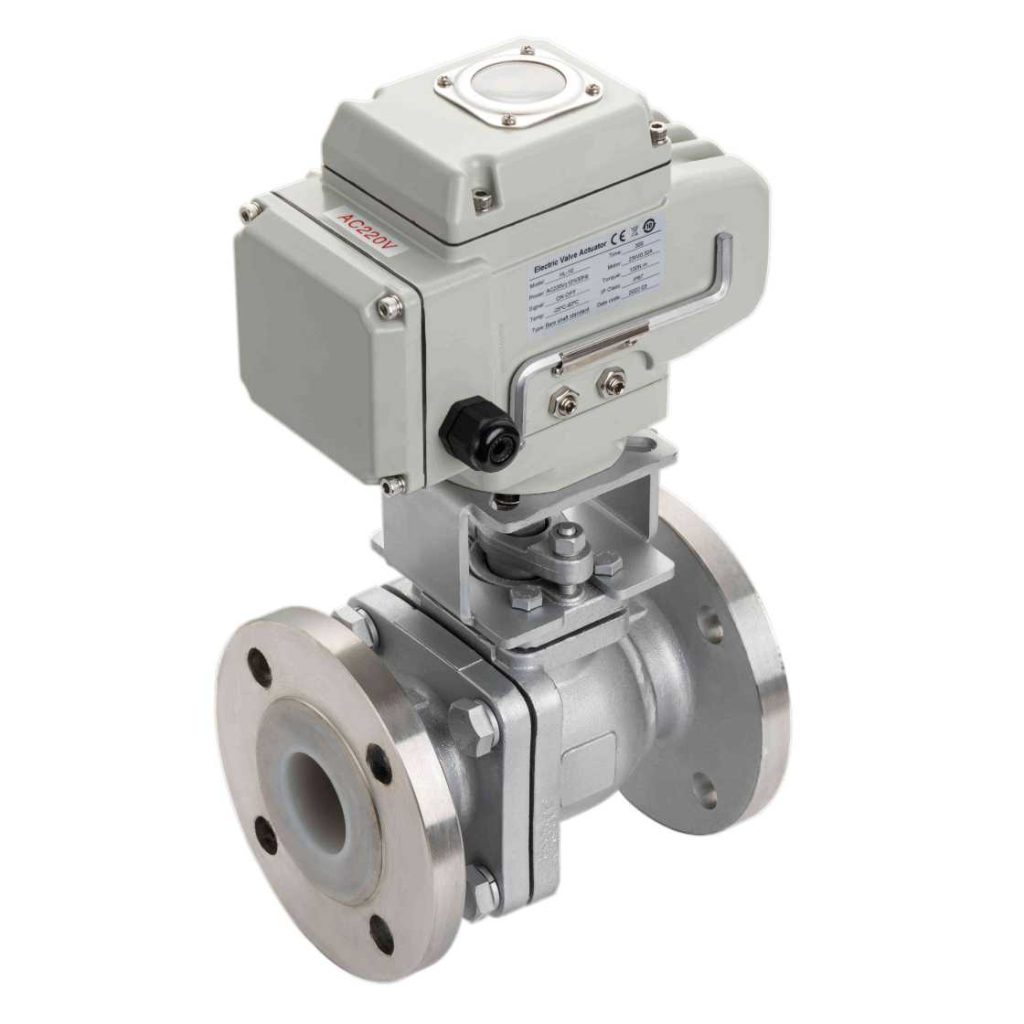
The Role of Electric Anti-Corrosion Ball Valves
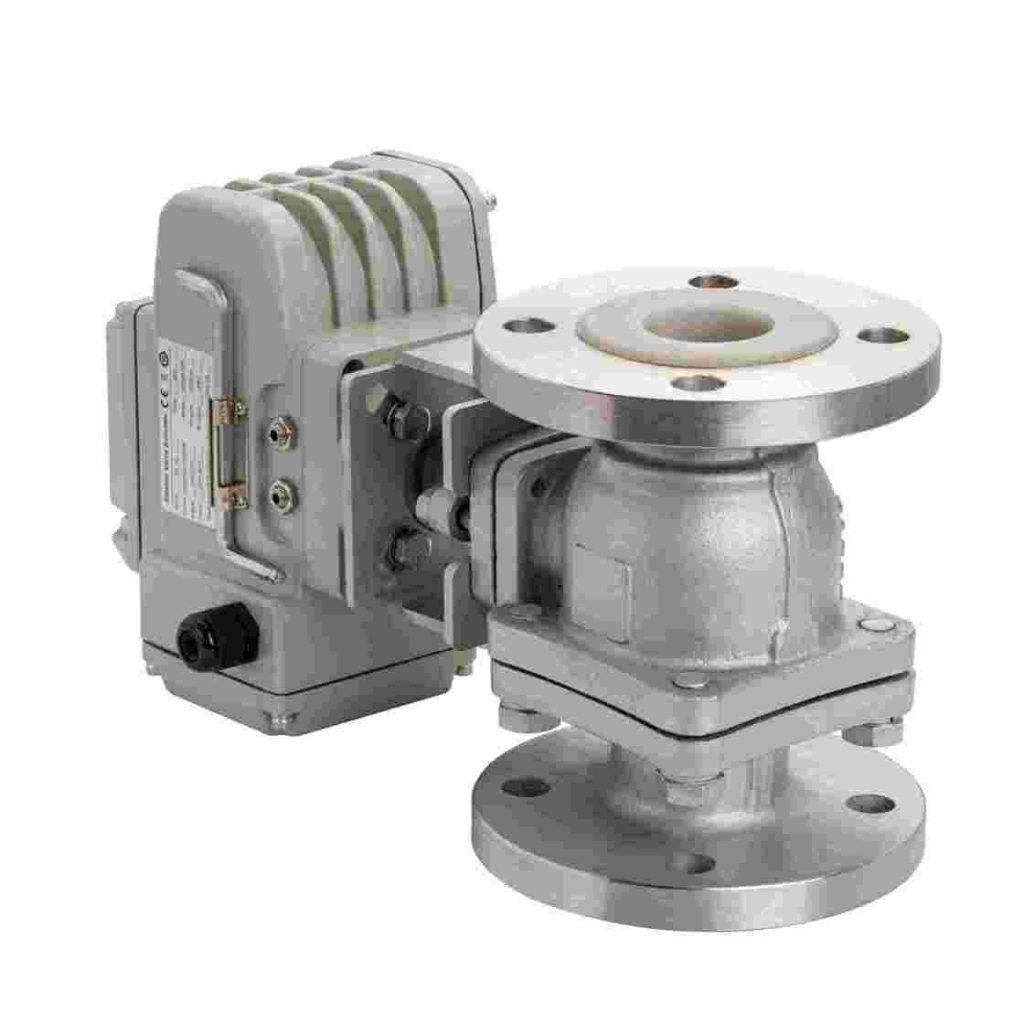
Electric anti-corrosion ball valves are essential components in fluid control systems, where they regulate the flow of liquids, gases, or slurries. Unlike traditional manual or pneumatic valves, electric ball valves are automated and operated by electric actuators, which allow for precise control over the valve’s opening and closing. The term “anti-corrosion” refers to the special materials and coatings used to protect the valve from the damaging effects of corrosive substances, thus extending the valve’s life and ensuring reliable operation under harsh conditions. These valves typically feature a spherical closure mechanism, or “ball,” with a hole through its center. The ball can be rotated 90 degrees to either allow or block the flow of the medium passing through it. The key advantage of the electric actuator is that it provides remote control capabilities, enabling operators to manage valve positions without direct human intervention, thereby improving safety, efficiency, and convenience in operations.
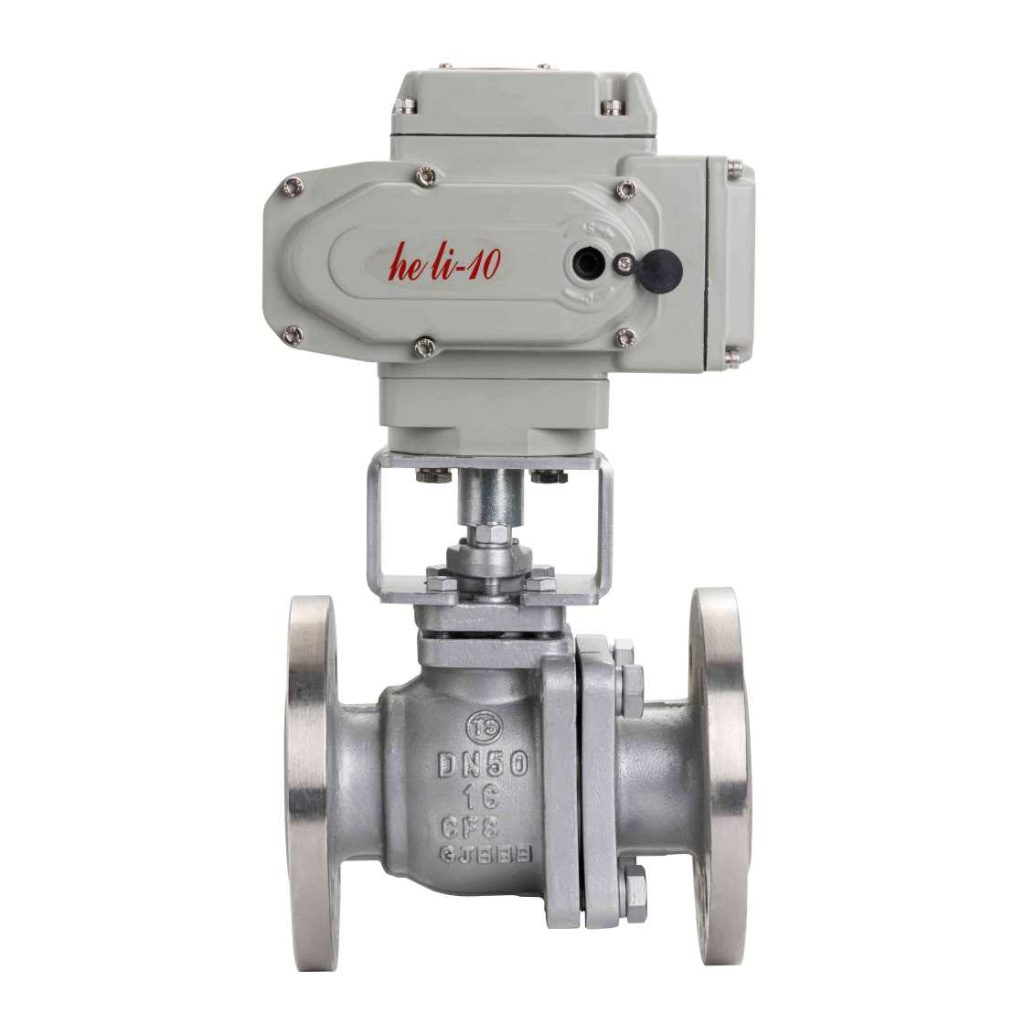