In the realm of modern manufacturing, DMC thermosetting materials have emerged as a cornerstone of innovation, enabling the creation of durable and high-performance parts across diverse industries. This article delves into the world of DMC thermosetting material parts manufacturers, exploring their vital role in shaping the present and future of engineering.
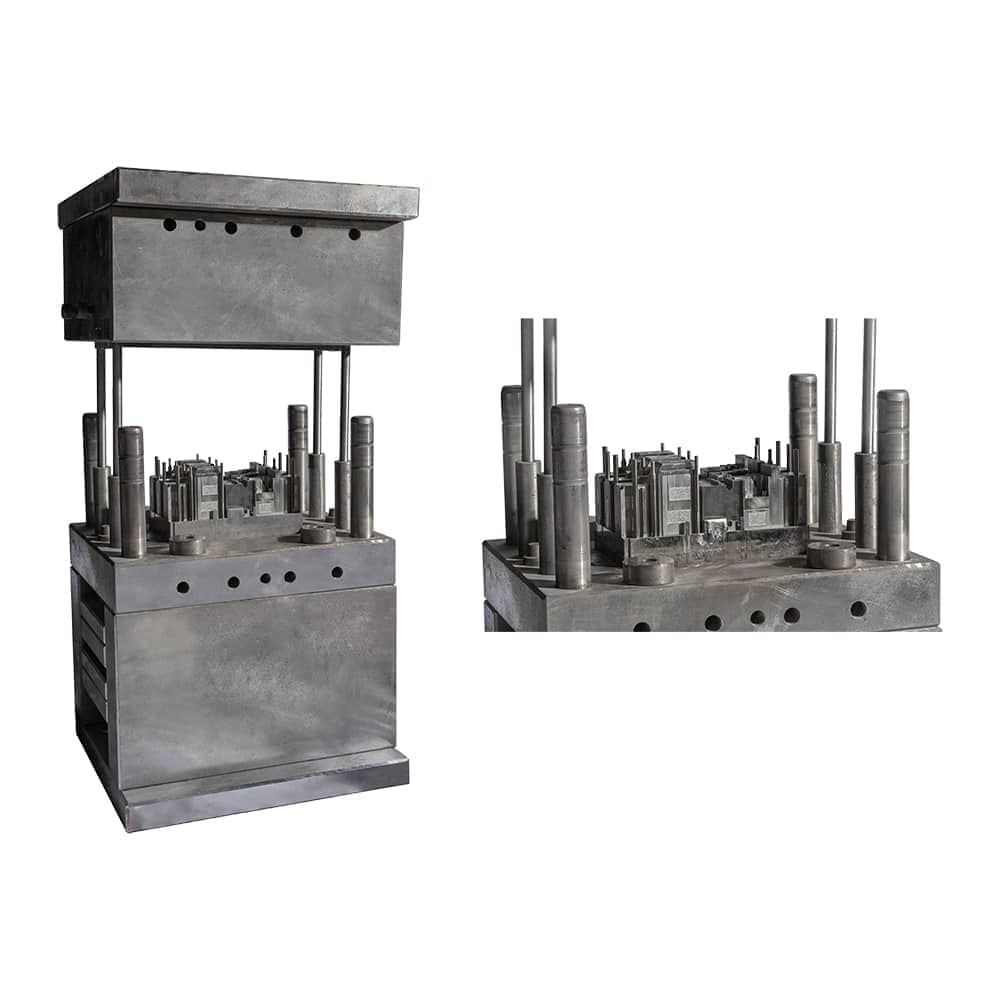
DMC (Dough Molding Compound) thermosetting materials are a class of composite materials that consist of a blend of resins, fillers, and reinforcing fibers. These materials possess exceptional heat resistance, mechanical strength, and dimensional stability, making them an ideal choice for manufacturing parts that endure demanding conditions. From automotive components to electrical enclosures, DMC parts manufacturers have demonstrated their prowess in producing components that meet stringent performance requirements.
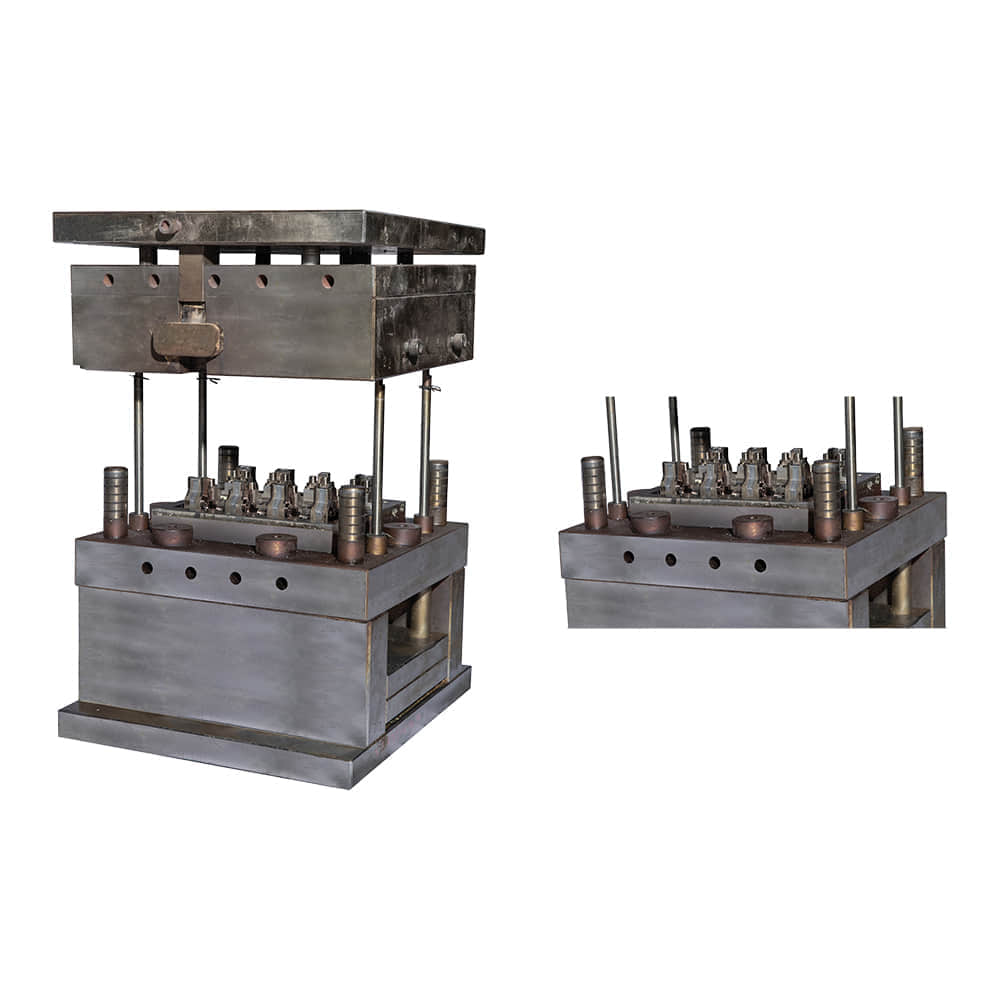
One of the key advantages of DMC thermosetting materials is their adaptability. Manufacturers can precisely tailor the composition of DMC to achieve specific mechanical, electrical, or thermal properties, ensuring that the final product aligns with the intended application. This versatility has led to DMC materials being employed in a wide array of industries such as aerospace, telecommunications, and consumer electronics. In the automotive sector, DMC thermosetting material parts have revolutionized vehicle design. Bumper supports, engine components, and interior panels manufactured from DMC materials exhibit enhanced impact resistance and temperature tolerance compared to traditional materials. Moreover, the lightweight nature of DMC parts contributes to improved fuel efficiency, aligning with the automotive industry’s drive towards sustainability. Electrical systems have also reaped the benefits of DMC thermosetting materials. Switchgear enclosures and insulating components manufactured using DMC materials offer excellent electrical insulation and fire resistance. These qualities are crucial for ensuring the safety and reliability of electrical infrastructure, especially in high-voltage applications. The success of DMC thermosetting material parts manufacturers can be attributed to their mastery of production processes. The dough-like mixture of resins and fillers allows for complex molding and shaping, enabling the creation of intricate and customized parts. Compression molding and injection molding are common techniques employed by manufacturers to achieve precision and consistency in part production. Quality control and testing are paramount in the DMC manufacturing process. Manufacturers adhere to rigorous testing standards to ensure that the final parts meet or exceed performance expectations. This commitment to quality has solidified the reputation of DMC thermosetting materials as a dependable choice for critical applications. Looking ahead, DMC thermosetting material parts manufacturers are poised to play a pivotal role in the ongoing technological advancements. As industries continue to demand materials that can withstand harsh conditions, offer improved efficiency, and enable miniaturization, DMC materials are expected to rise to the challenge. In conclusion, DMC thermosetting material parts manufacturers are at the forefront of engineering excellence. Their ability to harness the unique properties of DMC materials and transform them into reliable and high-performance components has revolutionized industries ranging from automotive to electronics. With a commitment to innovation and quality, these manufacturers are shaping a future where durability and efficiency go hand in hand.
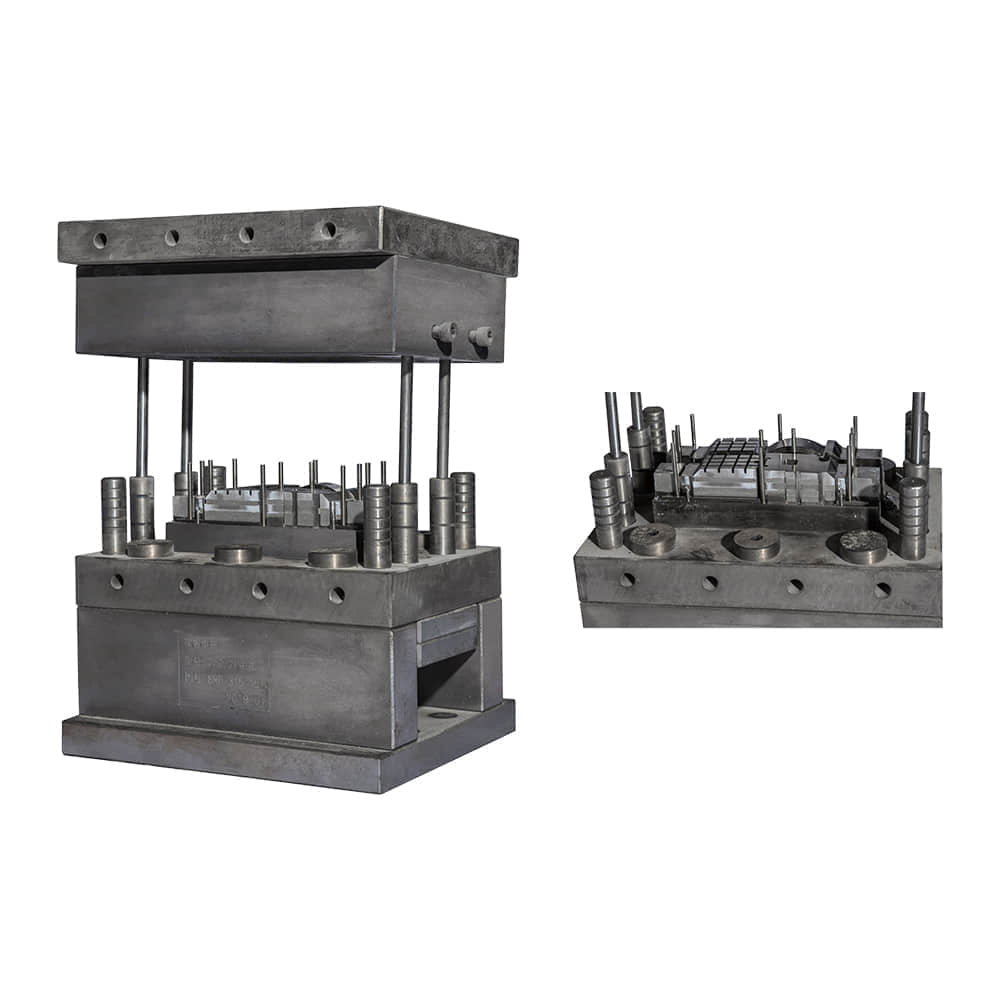