In the realm of modern manufacturing, Sheet Molding Compound (SMC) molding has emerged as a revolutionary process that offers unparalleled advantages. SMC molding, a technique widely used in the production of various composite materials, has transformed the landscape of manufacturing industries. This article delves into the intricacies of SMC molding and its numerous benefits.
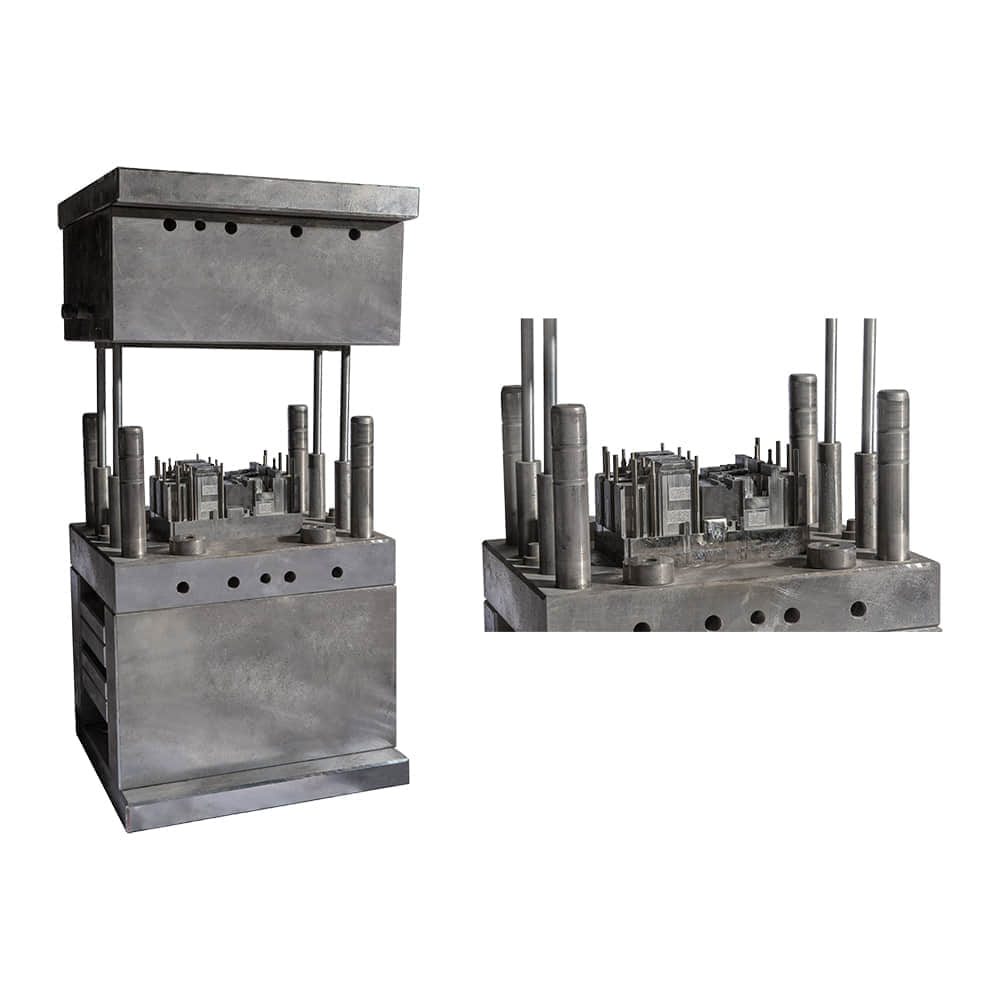
SMC molding involves combining long-fiber reinforcement materials with a thermoset resin matrix to create a composite material that boasts remarkable strength, durability, and versatility. The process begins with the impregnation of the reinforcement fibers with the resin, forming a semi-liquid mixture. This mixture is then transferred into a mold, which is subsequently closed and heated to promote curing. The result is a solid, high-strength composite part that can be tailored to meet specific design requirements.
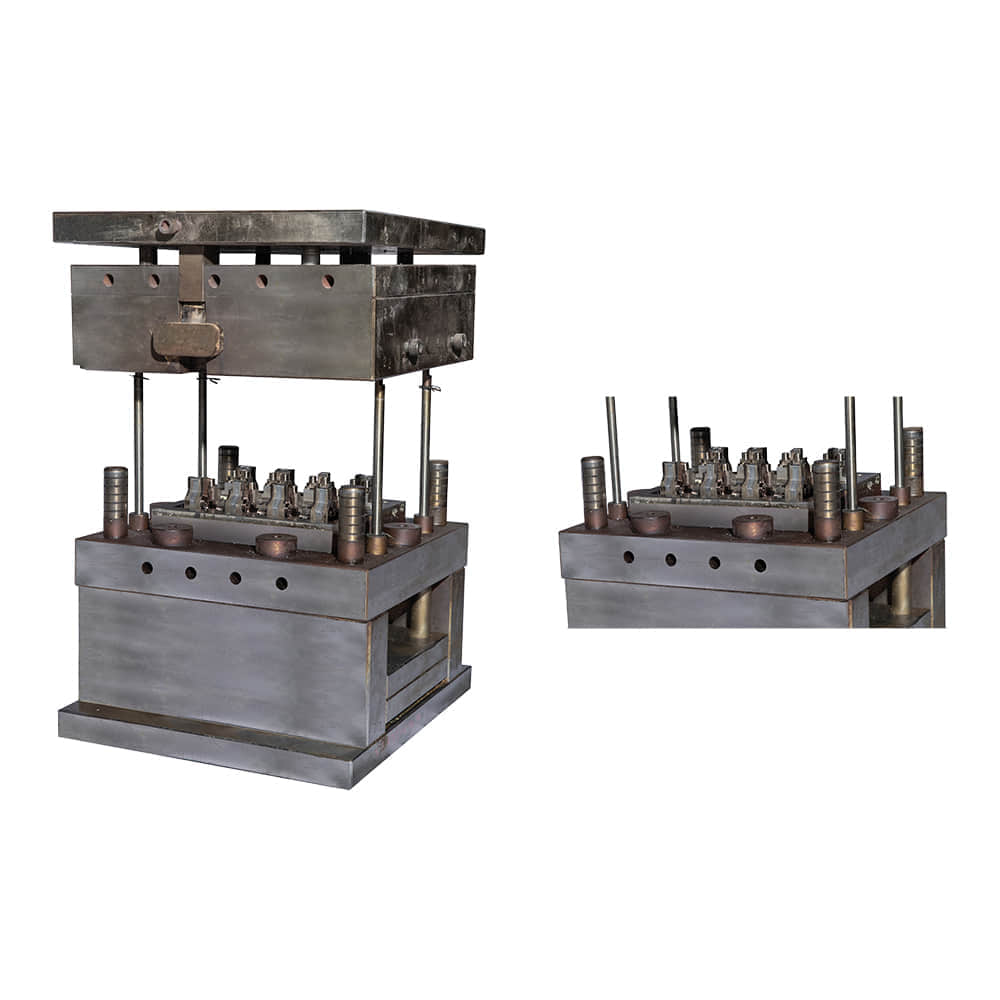
One of the key advantages of SMC molding is its exceptional mechanical properties. The incorporation of long-fiber reinforcements endows the final product with impressive tensile, flexural, and impact strength. This makes SMC-molded components ideal for applications requiring structural integrity and load-bearing capabilities, such as automotive panels, construction elements, and electrical enclosures. Moreover, SMC molding enables intricate design flexibility. The mold can be crafted to accommodate complex geometries, intricate patterns, and fine details that might be challenging to achieve using traditional manufacturing methods. This flexibility allows for the creation of parts that are not only strong but also aesthetically pleasing, expanding the realm of possibilities for designers and engineers. The corrosion resistance of SMC-molded parts adds another layer of appeal, particularly in industries where exposure to harsh environmental conditions is common. Unlike metals, which are susceptible to rust and degradation, SMC components exhibit remarkable resistance to corrosion, extending the lifespan of the end product and reducing maintenance costs. Weight reduction is a paramount concern across industries seeking to enhance energy efficiency and overall performance. SMC molding addresses this concern effectively, as the lightweight nature of the composite material contributes to the reduction of the overall weight of the final product. This is of utmost importance in automotive and aerospace applications, where lighter components can lead to improved fuel efficiency and enhanced maneuverability. Furthermore, SMC molding stands out for its efficient production process. The semi-liquid nature of the material allows for quick and consistent filling of complex molds. The curing process can be precisely controlled, leading to shorter cycle times and higher production rates compared to traditional methods like hand lay-up. This efficiency not only accelerates the manufacturing timeline but also lowers production costs. In conclusion, Sheet Molding Compound (SMC) molding has ushered in a new era of manufacturing possibilities. Its exceptional mechanical properties, design flexibility, corrosion resistance, weight reduction benefits, and efficient production process make it a compelling choice for industries ranging from automotive to construction. As technology continues to advance, SMC molding is likely to further evolve, bringing even more innovations to the world of composite materials and manufacturing.
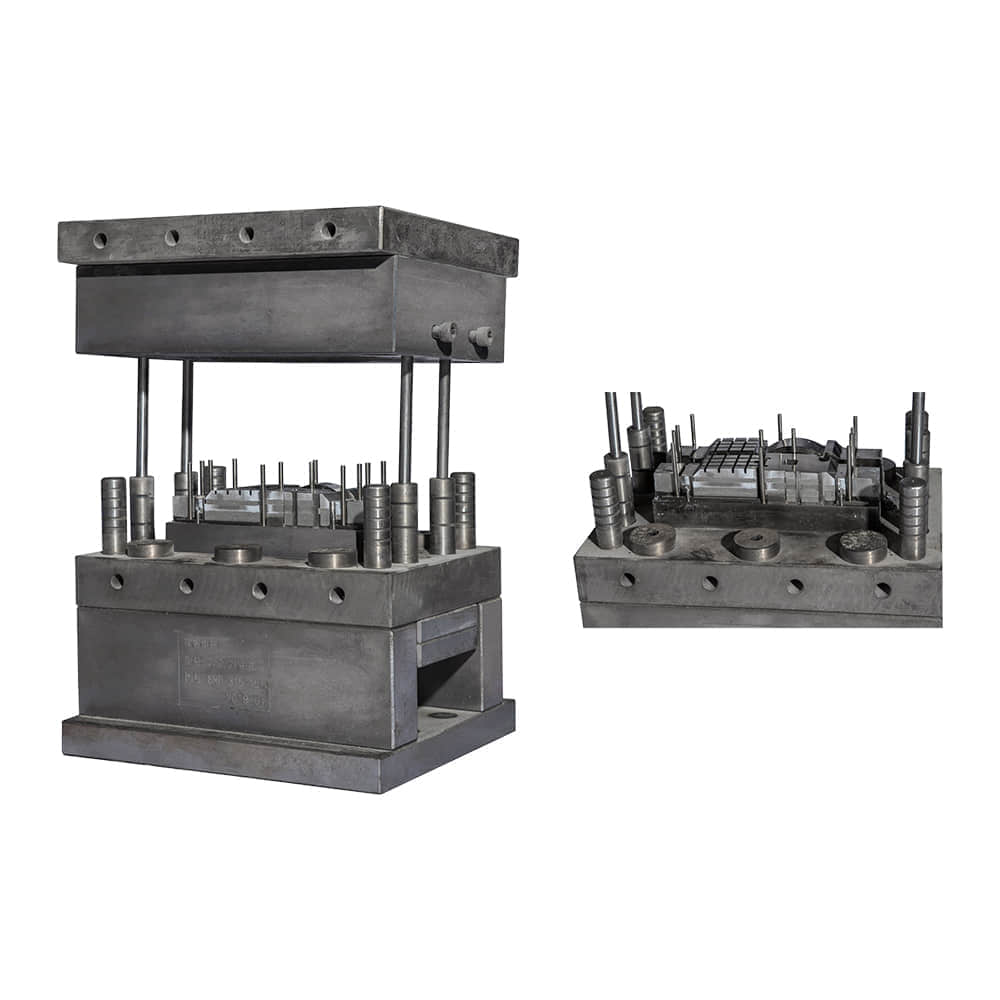