In the realm of modern manufacturing, technological advancements continue to reshape the landscape of efficiency, precision, and productivity. One innovation that stands out is the progressive die, a marvel of engineering that has revolutionized metalworking processes. This article delves into the intricacies and benefits of progressive dies, highlighting their vital role in shaping various industries.
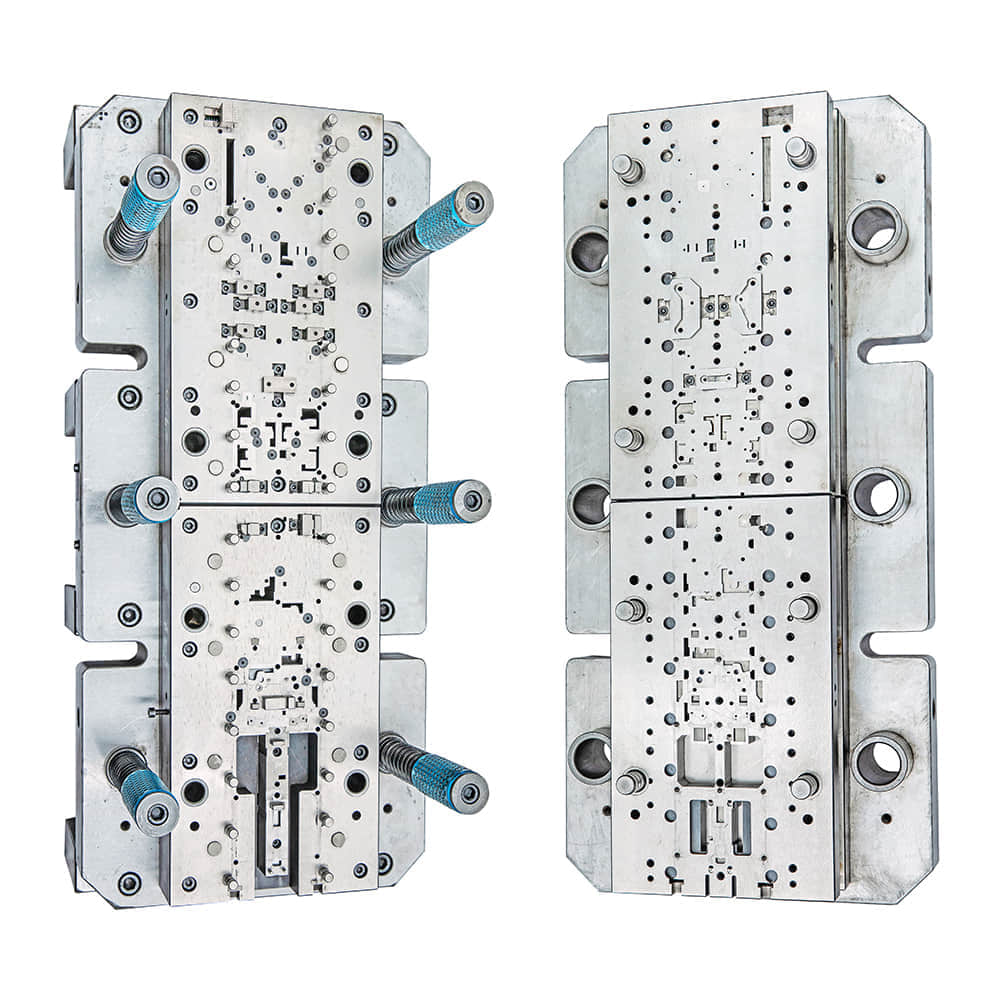
Understanding Progressive Dies:A progressive die is a specialized tool used in sheet metal forming processes, particularly in mass production scenarios. It functions as a series of interconnected dies, each performing a specific task in a sequence, progressively shaping a metal workpiece into its final form. The workpiece advances through the various dies in a continuous manner, undergoing cutting, bending, punching, and other operations until it emerges as a fully formed product.
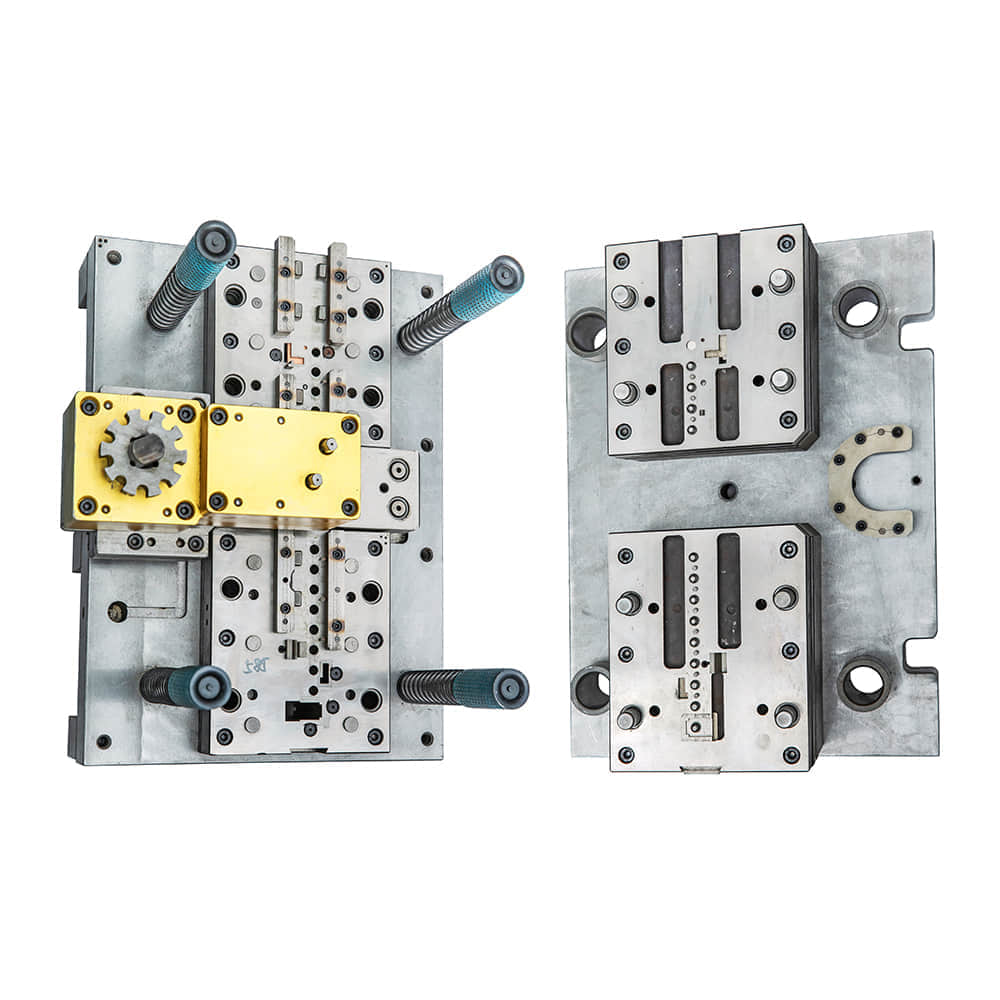
The Mechanism Behind the Innovation:Progressive dies operate on the principle of efficiency and precision. Unlike traditional methods where separate operations are performed on different machines, progressive dies condense multiple steps into a single, seamless process. This not only reduces the time required but also minimizes material waste and human intervention. The dies are meticulously designed using Computer-Aided Design (CAD) software, allowing engineers to simulate the entire manufacturing process before actual production begins. Advantages of Progressive Dies: Enhanced Efficiency:The continuous flow of workpieces through various dies minimizes idle time, optimizing production rates and reducing lead times. Cost Savings:With fewer manual interventions, labor costs are reduced. Additionally, the material wastage is minimized due to the precise nature of the process. Consistent Precision:Progressive dies ensure consistent, high-quality products as each step is controlled and monitored within tight tolerances. Complex Geometries:These dies can handle intricate shapes and complex geometries that might be challenging for traditional manufacturing methods. Versatility:Progressive dies can be tailored to various materials, including metals, plastics, and even composite materials. Scalability:From small components to larger parts, progressive dies can be adapted for different sizes without extensive modifications. Reduced Floor Space:Since multiple operations are integrated into a single setup, the floor space required for manufacturing is significantly reduced. Applications Across Industries:Progressive dies find applications in a wide range of industries, including automotive, electronics, appliances, and more. In the automotive sector, these dies are instrumental in crafting intricate parts such as brackets, clips, and connectors. In electronics, they aid in producing components like connectors and casings with precision. The appliance industry benefits from progressive dies to manufacture items like metal panels and hinges. Pushing the Boundaries:Advancements in materials, lubrication techniques, and die design software continue to push the boundaries of what progressive dies can achieve. High-strength materials that were once considered challenging to process are now within the scope of these innovative tools. Additionally, improved simulation capabilities help in identifying potential issues before they arise, leading to more streamlined production processes. Conclusion:The world of manufacturing is in a perpetual state of evolution, and progressive dies stand as a testament to human ingenuity in enhancing efficiency and precision. From automotive parts to intricate electronic components, these dies have become indispensable in the realm of mass production. As technology continues to advance, one can only anticipate further refinements in the design and application of progressive dies, propelling industries toward even greater levels of productivity and innovation.
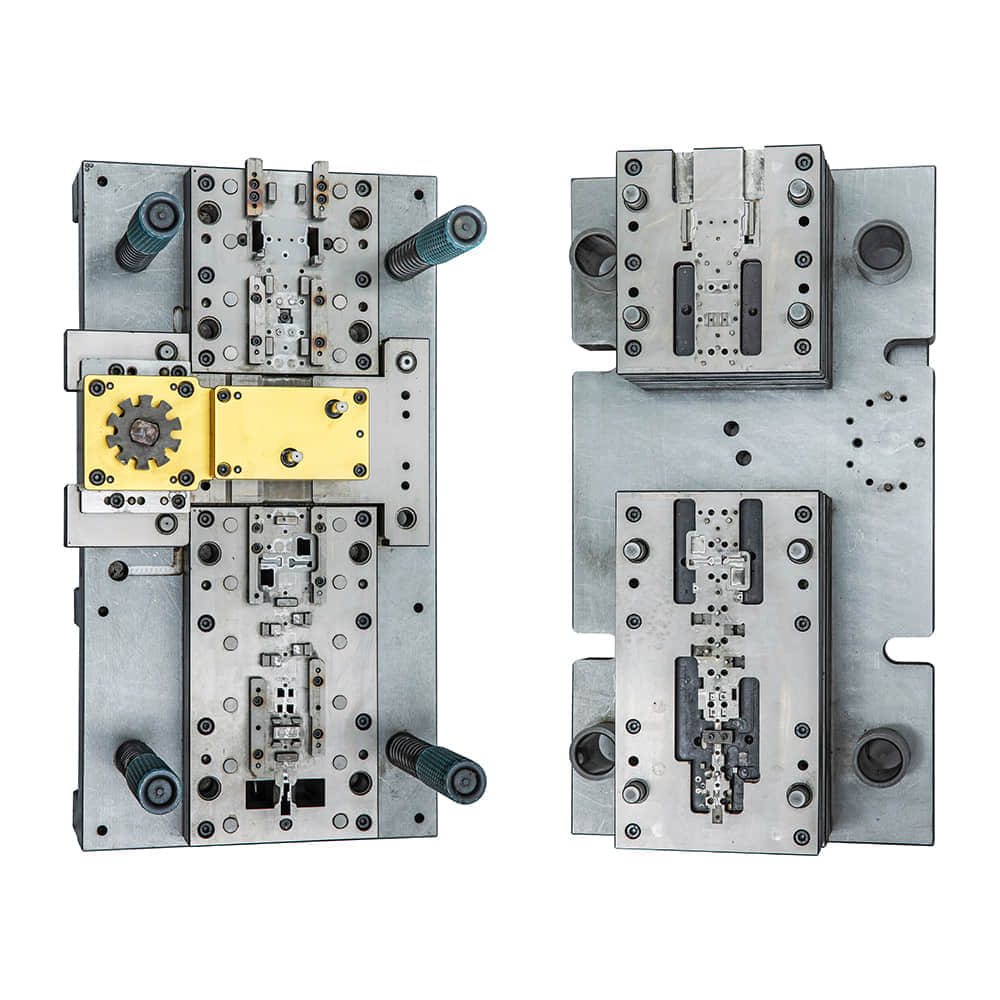