In the intricate world of manufacturing and engineering, a critical component that often goes unnoticed but plays a significant role is molded case parts. These unassuming elements are essential in various industries, from electrical engineering to automotive manufacturing. In this article, we will delve into the fascinating realm of molded case parts, exploring their importance, applications, and the processes involved in their creation.
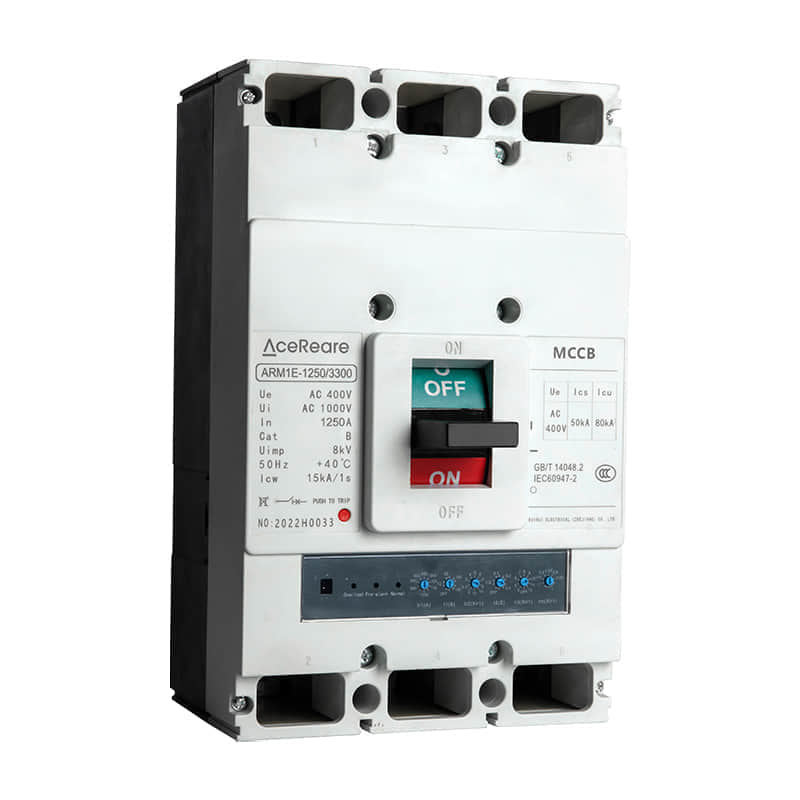
The Essence of Molded Case Parts
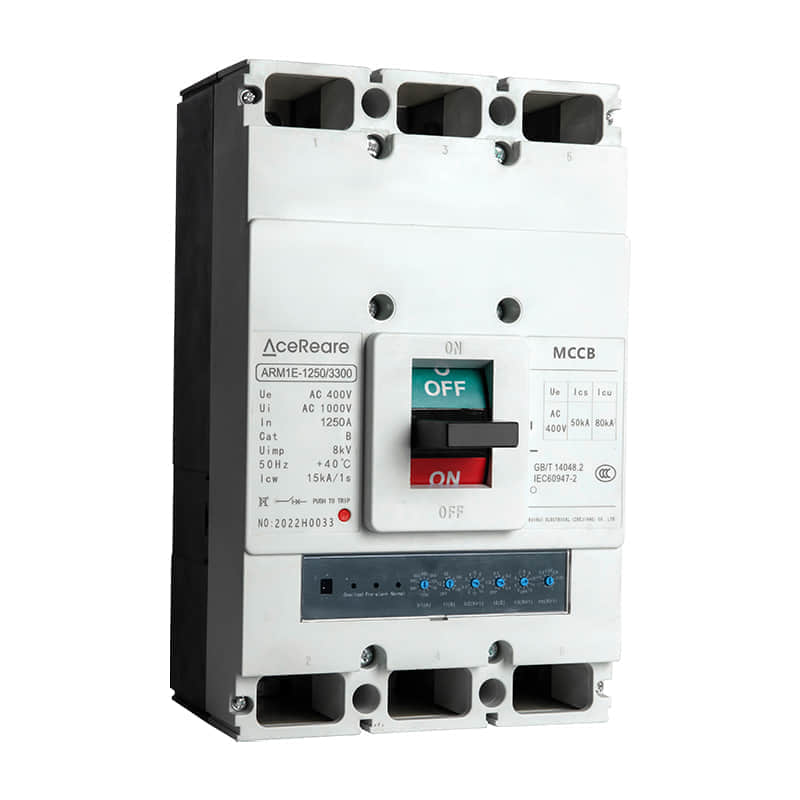
Molded case parts are precisely what their name suggests: parts that are formed through a molding process. This process involves the use of molds or dies to shape materials, typically plastics or metals, into specific forms. The resulting parts are known for their durability, consistency, and cost-effectiveness. Applications Galore The applications of molded case parts span across multiple industries, each benefiting from their unique characteristics. Electrical Engineering: In the realm of electrical distribution, molded case circuit breakers are indispensable. These breakers are responsible for protecting electrical circuits from overloads and short circuits, ensuring safety in both residential and industrial settings. Automotive Industry: Molded plastic components are widely used in vehicles. From interior trim pieces to intricate under-the-hood parts, these components contribute to the overall aesthetics and functionality of automobiles. Consumer Goods: Household appliances, toys, and electronic gadgets often incorporate molded case parts. These components provide the necessary structure and design elements while keeping production costs in check. Medical Devices: In the medical field, molded case parts are used in devices ranging from diagnostic equipment to prosthetic limbs. The precision and consistency of these parts are critical for patient safety and device effectiveness. Aerospace: Aircraft and spacecraft rely on lightweight, high-strength materials, many of which are molded to create complex shapes. These parts must withstand extreme conditions, making the reliability of the molding process paramount. The Manufacturing Process The creation of molded case parts involves a series of intricate steps: Material Selection: The choice of material depends on the specific application. Plastics, such as ABS, PVC, and polycarbonate, are common for their versatility, while metals like aluminum and steel offer durability and strength. Design and Tooling: Engineers design the mold or die that will shape the material. The mold’s precision directly impacts the final product’s quality. Molding Process: The selected material is heated until it becomes pliable, then injected or pressed into the mold. It is cooled and solidified within the mold’s shape. Quality Control: Rigorous testing ensures that each molded case part meets the required standards for dimensions, strength, and aesthetics. Finishing: Parts may undergo secondary processes, such as trimming, painting, or assembly, depending on the application. Advantages of Molded Case Parts Cost-Efficiency: Mass production techniques make molded case parts cost-effective, especially when compared to machining or other fabrication methods. Consistency: The molding process ensures uniformity, reducing the risk of defects and failures. Design Flexibility: Complex shapes can be achieved, allowing for innovative designs that might be challenging with other manufacturing methods. Durability: Many molded case parts are known for their longevity and resistance to wear and tear. Challenges and Innovations While molded case parts offer numerous advantages, there are challenges to overcome, such as material waste and environmental concerns. Innovations in materials, recycling processes, and sustainable practices are addressing these issues, making molded case parts more environmentally friendly. Conclusion Molded case parts are the unsung heroes of various industries, contributing to the functionality and efficiency of products we use daily. From circuit breakers to car components and beyond, these unassuming parts play a vital role in modern manufacturing. As technology advances and sustainability becomes increasingly important, the world of molded case parts continues to evolve, promising even more innovative solutions for the future.
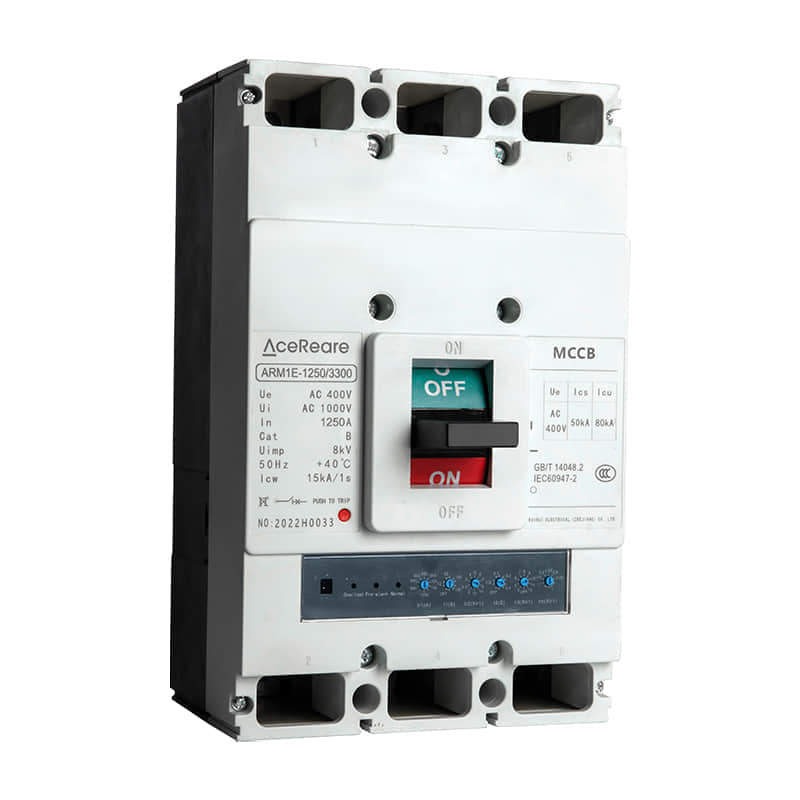