Metal stamping, a versatile manufacturing process, has revolutionized industries by providing cost-effective and efficient solutions for producing intricate metal parts. The process involves using specialized tools to shape, cut, and form metal sheets into desired configurations, catering to a wide range of applications across various sectors.
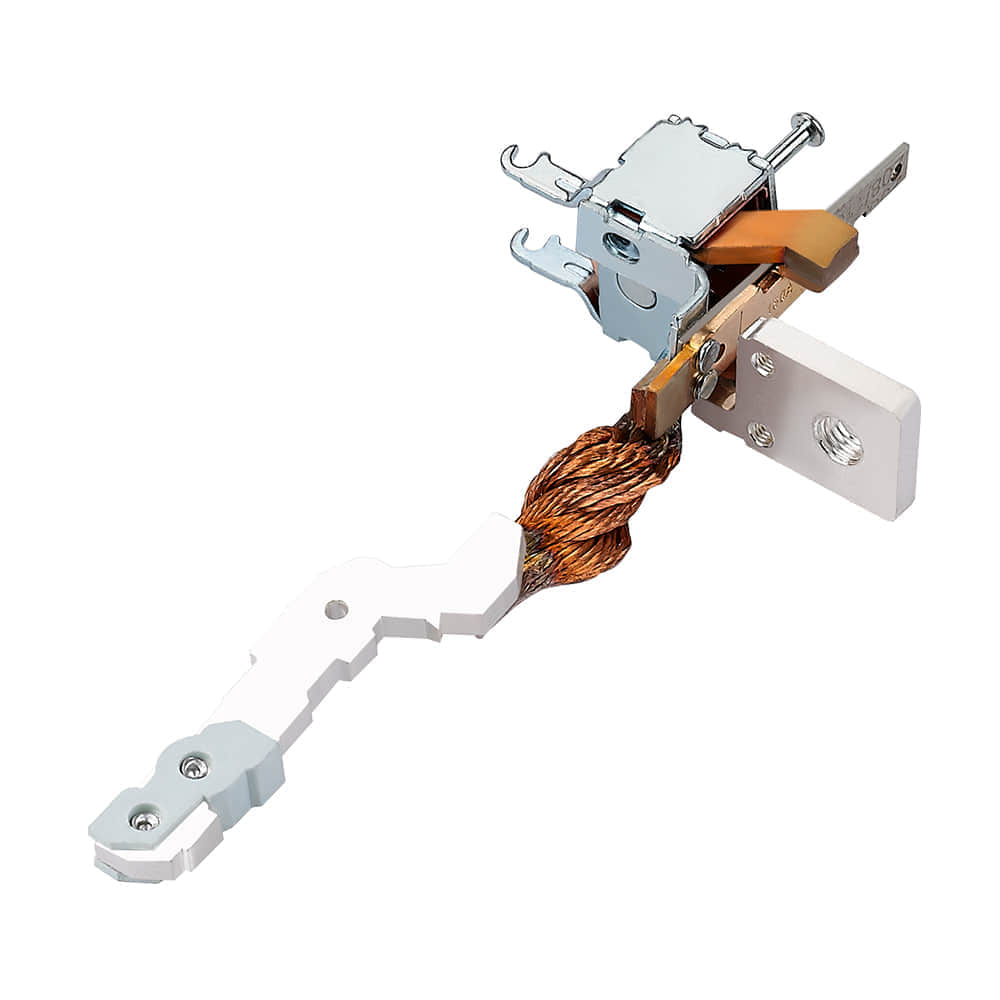
The Advancements in Metal Stamping Technology: Over the years, metal stamping technology has undergone significant advancements, driven by innovations in materials, machinery, and automation. Computer Numerical Control (CNC) systems now govern the precision and complexity of stamping operations, enhancing the consistency and quality of the final products. Additionally, simulation software allows manufacturers to visualize the stamping process digitally, optimizing designs before physical production begins.
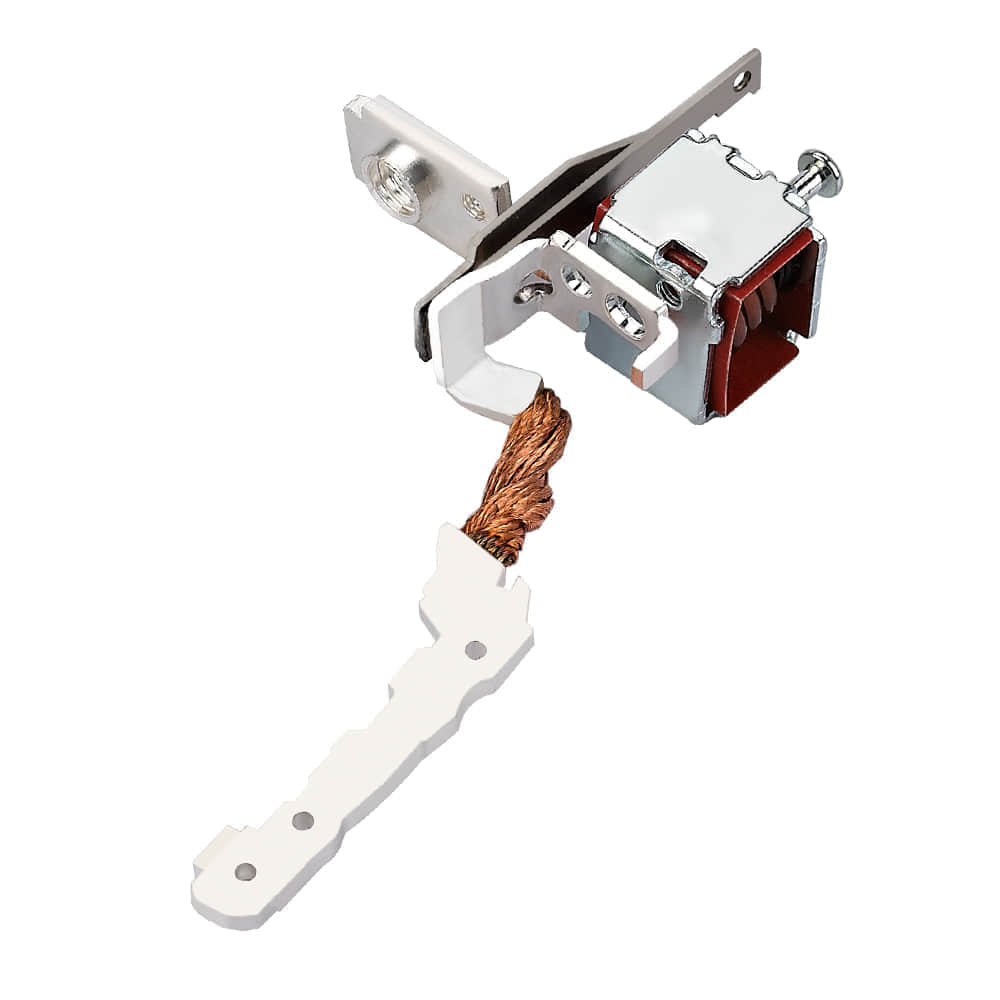
Materials Diversity and Application Versatility: Metal stamping supports an extensive array of materials, including stainless steel, aluminum, copper, and various alloys. This diversity in materials contributes to the versatility of the process, making it suitable for manufacturing components in industries such as automotive, electronics, aerospace, and even consumer goods. From intricate electronic connectors to robust automotive parts, metal stamping fulfills diverse needs across the manufacturing spectrum. Automotive Industry Transformation: The automotive industry has greatly benefited from metal stamping, with various engine and body components being manufactured using this process. Its ability to create complex and lightweight parts has contributed to improved fuel efficiency and overall vehicle performance. Moreover, the precision and speed of metal stamping facilitate the production of safety-critical parts, ensuring the reliability of vehicles on the road. Electronics and Beyond: In the electronics sector, the demand for smaller, more intricate components has driven the development of micro-stamping techniques. This sub-field of metal stamping enables the production of tiny parts used in electronic devices, such as connectors, terminals, and sensors. The high-volume production capabilities of metal stamping make it a cost-effective choice for the electronics industry, meeting the needs of a tech-driven world. Aerospace and Aviation Applications: Metal stamping finds its place in the aerospace and aviation industries, where safety and precision are paramount. Aircraft rely on numerous metal components, and stamping ensures that these parts meet stringent quality standards while remaining lightweight. The ability to work with diverse materials further cements metal stamping’s significance in this field, contributing to the construction of both commercial and military aircraft. Challenges and Future Prospects: While metal stamping has come a long way, challenges remain, particularly in the realm of sustainability. Efforts are being made to reduce waste and energy consumption during the manufacturing process. Additionally, advancements in machine learning and AI are being integrated into metal stamping systems to enhance efficiency and predictive maintenance. In conclusion, metal stamping parts have revolutionized modern manufacturing across industries, enabling the production of intricate components with unmatched precision and efficiency. With ongoing technological advancements and the ability to work with a diverse range of materials, metal stamping continues to shape the products that define our world. As sustainability and automation become increasingly important, the future of metal stamping holds the promise of even greater innovation and impact.
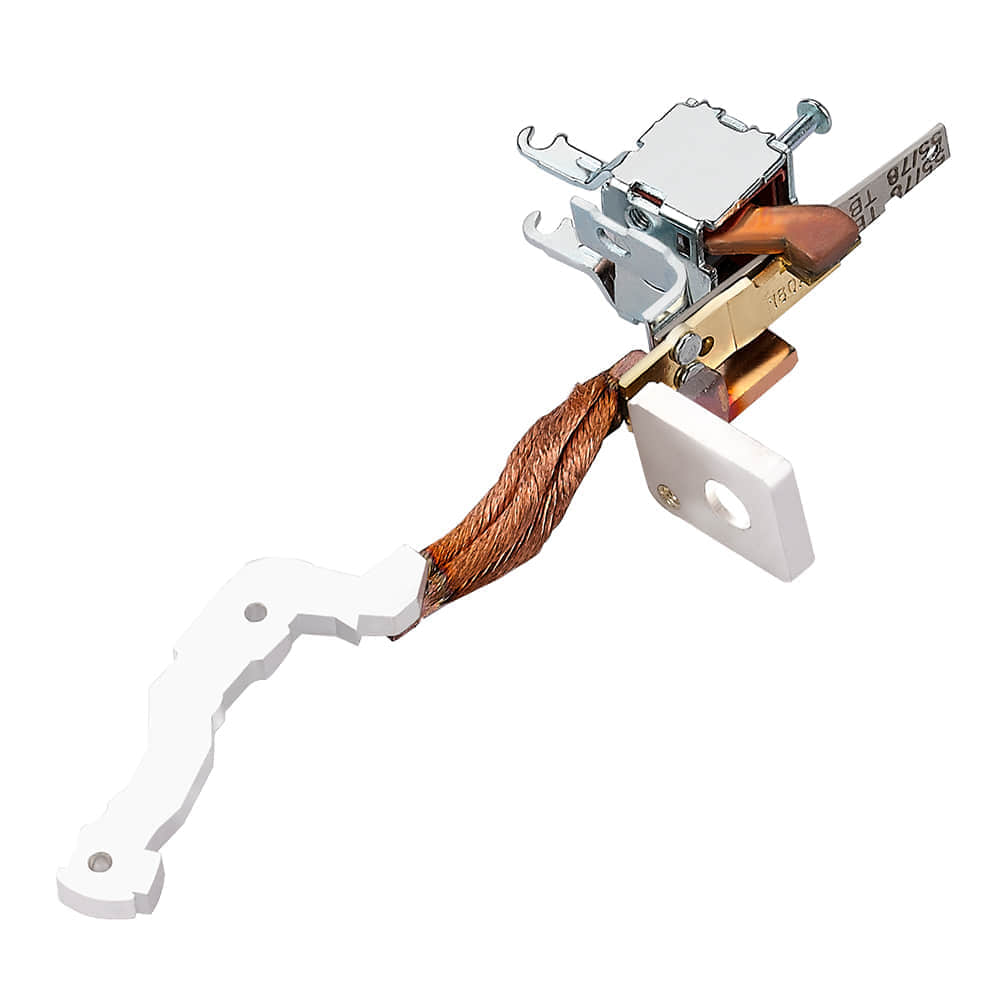