In the realm of engineering and manufacturing, precision and durability are paramount. One integral component that embodies these qualities is the Molded Case Part (MCP). Molded Case Parts are essential elements used in a wide array of industries, contributing significantly to the functionality and safety of various applications. This article delves into the world of Molded Case Parts, shedding light on their significance, manufacturing process, and diverse applications.
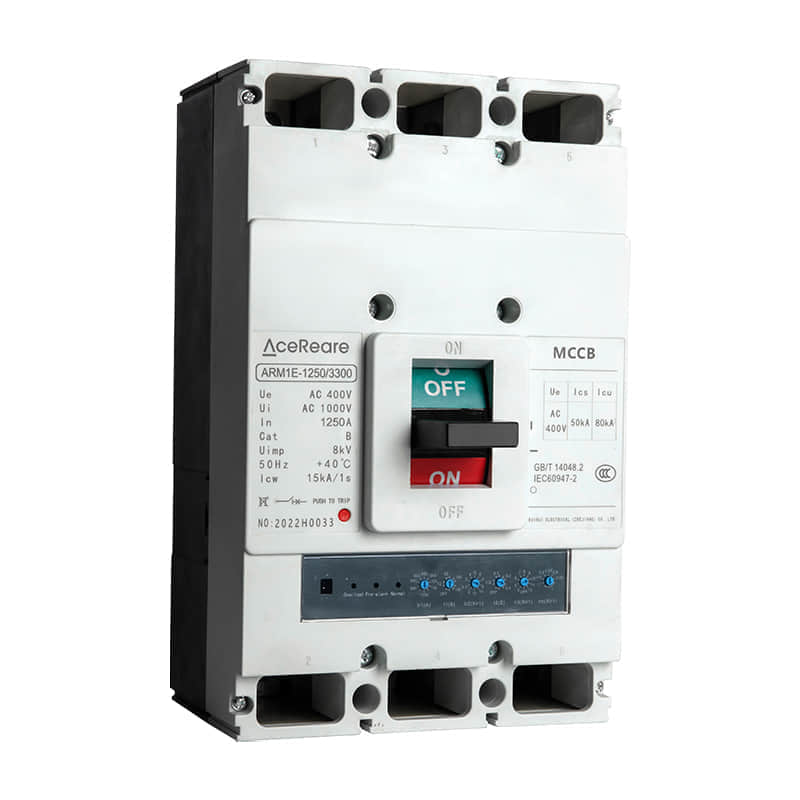
Understanding Molded Case Parts
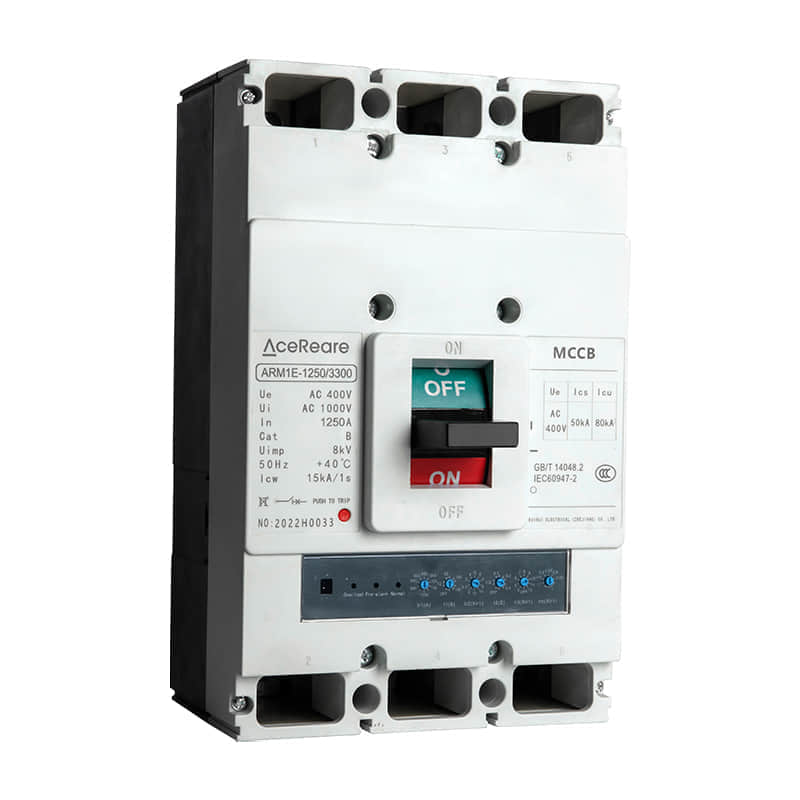
Molded Case Parts refer to components that are manufactured through a molding process, wherein a material is injected or poured into a mold to obtain a specific shape. The molding process allows for intricate designs and complex geometries to be achieved with remarkable precision. These parts are typically made from thermoplastics, thermosetting plastics, or even metals, depending on the desired properties and application requirements. The Manufacturing Process The process of creating Molded Case Parts begins with the design phase. Engineers meticulously create detailed designs using computer-aided design (CAD) software, taking into consideration factors such as material selection, structural integrity, and functionality. Once the design is finalized, the mold is created. This mold, usually made from steel or aluminum, is the negative of the desired part. The molding process itself involves heating the chosen material until it becomes malleable, then injecting it into the mold. After the material cools and solidifies, the mold is opened, revealing the finished part. The part is then subjected to quality checks, such as dimensional accuracy and material strength tests, to ensure it meets the required specifications. Diverse Applications Molded Case Parts find applications across a spectrum of industries, playing a vital role in enhancing performance and safety. In the automotive sector, MCPs are used in various components, including engine parts, interior elements, and electrical connectors. These parts offer high heat resistance and durability, making them essential for the demanding conditions within a vehicle. In the realm of electronics, Molded Case Parts are used in the production of circuit breakers, switches, and connectors. The precision achievable through the molding process ensures consistent performance and reliable connections, critical for electronic devices. Moreover, the aerospace industry benefits from the lightweight yet robust nature of MCPs. These parts are used in aircraft components, contributing to the overall fuel efficiency and structural integrity of the aircraft. Advantages of Molded Case Parts The utilization of Molded Case Parts offers several advantages. Firstly, the precision achievable through the molding process leads to consistent quality across large production volumes. Secondly, the ability to mold intricate designs ensures that even complex geometries can be replicated with remarkable accuracy. Thirdly, MCPs are known for their durability and resistance to environmental factors, contributing to the longevity of the final product. Challenges and Future Trends While Molded Case Parts bring numerous benefits, there are challenges to overcome. Designing the mold itself requires careful consideration to avoid defects and ensure efficient manufacturing. Moreover, selecting the appropriate material is crucial, as it directly impacts the performance and longevity of the part. Looking ahead, advancements in materials science and manufacturing technology are likely to shape the future of Molded Case Parts. The development of new materials with enhanced properties, such as higher heat resistance or greater flexibility, will expand the potential applications of MCPs. Additionally, innovations in molding techniques, including additive manufacturing and improved automation, will further streamline the production process. Conclusion Molded Case Parts stand as a testament to the fusion of engineering precision and manufacturing excellence. Their role in various industries, from automotive to electronics to aerospace, underscores their significance in modern technology and infrastructure. As technology continues to evolve, Molded Case Parts are poised to evolve alongside, driving innovation and progress across diverse sectors.
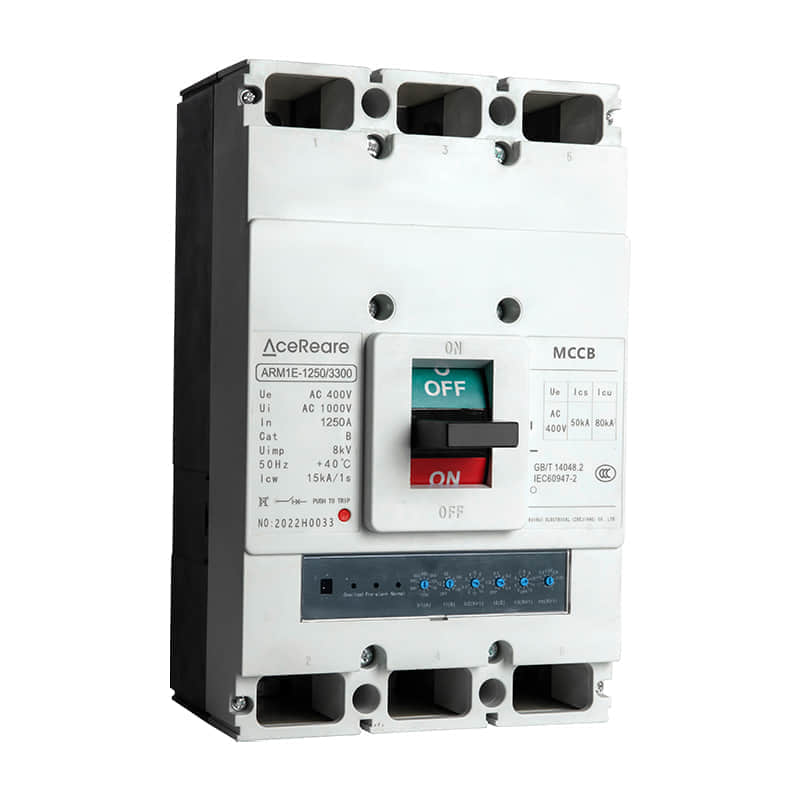