As the world embraces sustainable energy solutions, solar power has emerged as a prominent player in the race towards a greener future. Photovoltaic (PV) systems, which convert sunlight into electricity, have gained immense popularity. To ensure the safety and efficiency of these systems, the innovation of Photovoltaic DC circuit breakers by various brands has taken center stage. In this article, we delve into the advancements brought about by these circuit breaker brands in the realm of solar energy.
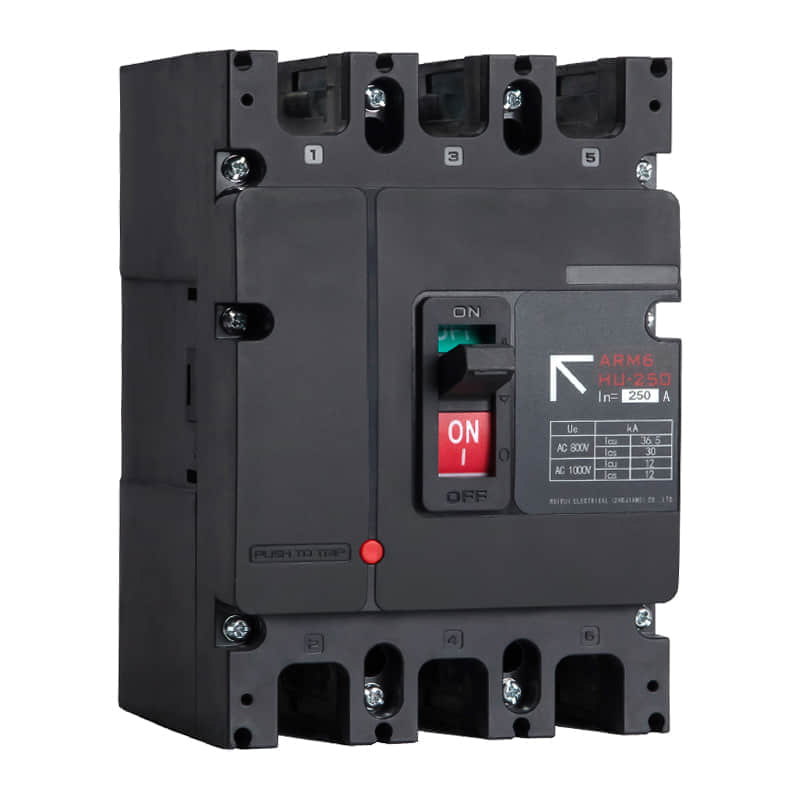
Photovoltaic DC circuit breakers are essential components in solar installations, as they safeguard the system from overcurrents and faults. Brands have been continuously investing in research and development to enhance the functionality and reliability of these circuit breakers. One of the prominent advancements lies in the incorporation of smart technologies. Modern PV DC circuit breakers are equipped with intelligent features such as remote monitoring, real-time data analysis, and the ability to communicate with other system components. This allows for swift identification of issues and remote control, minimizing downtime and maintenance costs.
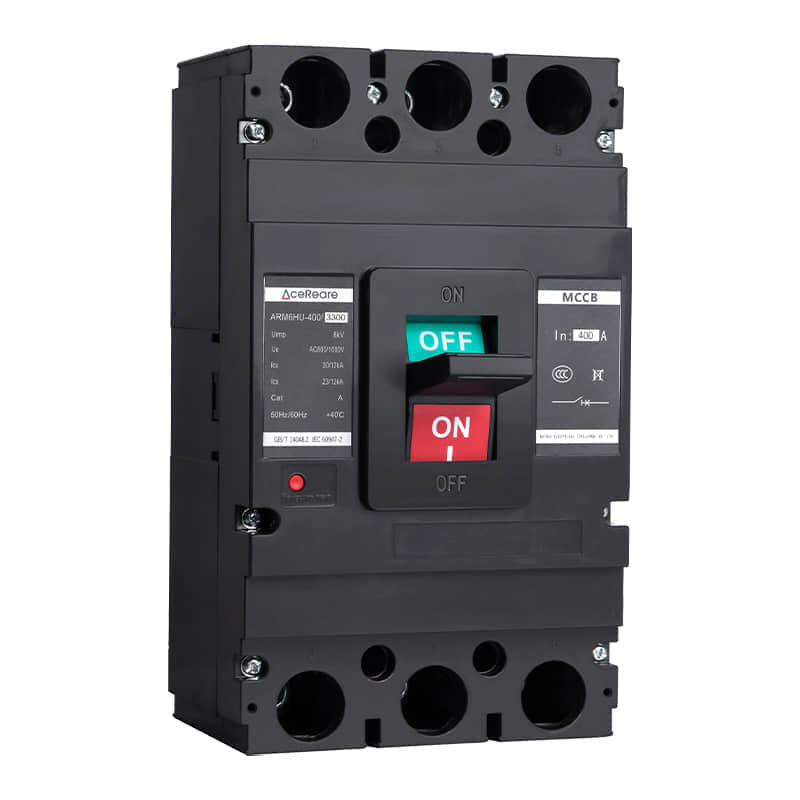
A key factor in the evolution of PV DC circuit breakers is their ability to handle higher voltages and currents. Traditional circuit breakers were designed for lower voltage systems, limiting their application in larger PV installations. However, forward-thinking brands have engineered circuit breakers that can handle the elevated demands of utility-scale solar projects. This scalability not only opens doors for more extensive solar arrays but also contributes to the integration of solar power into the mainstream energy grid. Furthermore, the issue of safety has received paramount attention in the development of PV DC circuit breakers. Arcing, which poses a significant safety hazard, has been a concern. In response, brands have introduced arc-fault detection technology that rapidly senses and extinguishes arcs, minimizing the risk of fires. These safety enhancements are crucial in ensuring the protection of both the PV system and the surrounding environment. The pursuit of efficiency has also driven innovations in PV DC circuit breakers. Traditional circuit breakers often exhibited energy losses in the form of heat dissipation. Modern solutions employ advanced materials and designs that reduce energy waste, leading to more efficient operation of the entire PV system. This not only maximizes power generation but also contributes to the overall sustainability of the solar installation. In the competitive market of PV DC circuit breakers, differentiation comes through the integration of advanced analytics. Brands are now offering circuit breakers with predictive maintenance capabilities. By analyzing real-time operational data, these circuit breakers can predict when maintenance is required, minimizing downtime and ensuring optimal performance. This data-driven approach enhances the reliability and longevity of the PV system, making solar power a more dependable energy source. It’s worth noting that global standards and certifications play a vital role in establishing the credibility of PV DC circuit breaker brands. Renowned brands ensure that their products adhere to international safety and performance standards, instilling confidence in consumers and industry professionals alike. This commitment to quality reflects the brand’s dedication to delivering reliable solutions for the growing solar energy market. In conclusion, the evolution of Photovoltaic DC circuit breaker brands is a testament to the advancement of solar energy technology. With their smart features, scalability, safety enhancements, improved efficiency, and data-driven insights, these circuit breakers are contributing to the widespread adoption of solar power. As the world continues its shift towards renewable energy sources, the innovations in PV DC circuit breakers illuminate a brighter and more sustainable future.
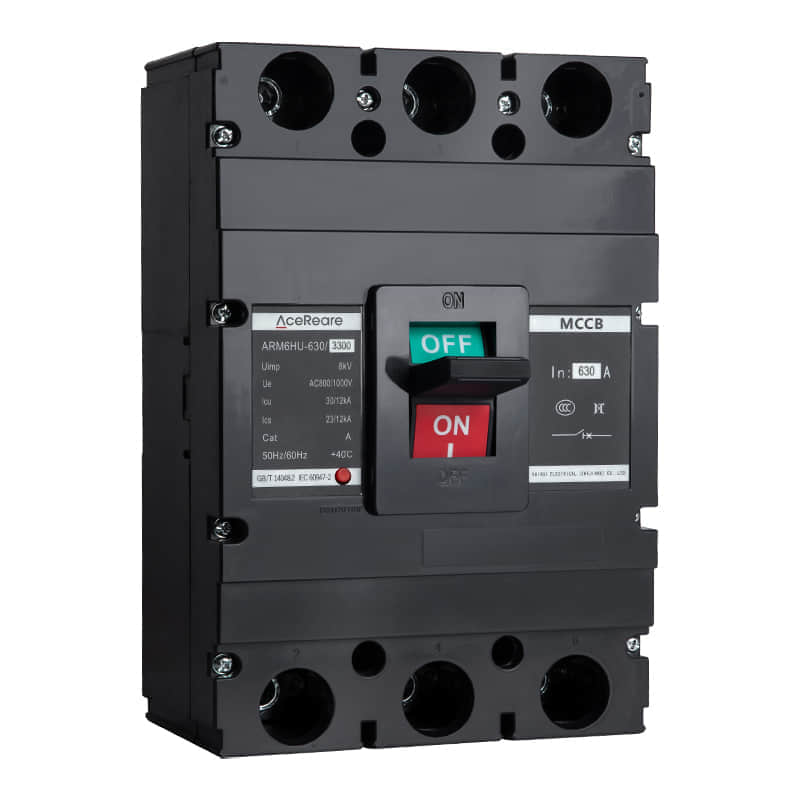