In today’s rapidly evolving industrial landscape, ensuring clean and contaminant-free air is of paramount importance. China, with its growing industrial prowess, has become a global leader in fan filter manufacturing, catering to a diverse range of industries. This article delves into the world of China’s fan filter manufacturers, highlighting their innovative solutions and commitment to cleaner, safer air quality.
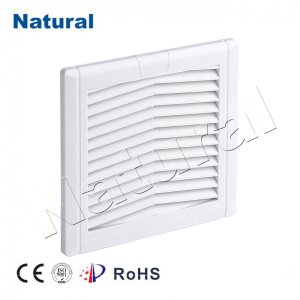
The Rise of China’s Fan Filter Manufacturers China’s emergence as a global manufacturing powerhouse extends to the production of fan filters. These critical components play a pivotal role in maintaining clean air environments across various sectors, from electronics manufacturing to pharmaceuticals. China’s fan filter manufacturers have risen to the occasion, meeting the ever-increasing demand for high-quality filtration solutions. Advanced Technologies and Innovations One of the key reasons behind China’s prominence in the fan filter manufacturing industry is its dedication to research and development. Leading manufacturers invest heavily in cutting-edge technologies to design and produce filters that excel in efficiency and durability. Advanced materials, precision engineering, and stringent quality control measures ensure that China-made fan filters meet or exceed international standards. Customized Solutions for Diverse Industries China’s fan filter manufacturers understand that each industry has unique air quality requirements. As a result, they offer a wide range of customizable solutions to suit various applications. Whether it’s a cleanroom for semiconductor production, a hospital operating room, or an industrial setting, these manufacturers can tailor their fan filters to meet specific needs. Energy Efficiency and Sustainability Environmental sustainability is a global concern, and China’s fan filter manufacturers are not left behind. They are committed to designing energy-efficient filters that minimize power consumption while maximizing air quality. The incorporation of sustainable materials and processes aligns with global efforts to reduce carbon footprints and promote eco-friendly manufacturing practices. Global Reach and Competitive Pricing China’s fan filter manufacturers have earned a reputation for providing high-quality products at competitive prices. This combination of quality and affordability has made them attractive partners for businesses worldwide. Their extensive distribution networks ensure that their filters are readily available to customers across the globe. Stringent Quality Assurance Quality assurance is a top priority for China’s fan filter manufacturers. Stringent testing and certification processes guarantee that each product leaving their facilities meets or exceeds industry standards. This commitment to quality has earned these manufacturers the trust of customers from diverse sectors. Embracing Digital Transformation In the era of Industry 4.0, China’s fan filter manufacturers are embracing digital transformation to enhance their production processes. Automation, data analytics, and real-time monitoring systems improve efficiency, reduce errors, and enable predictive maintenance, further ensuring the reliability of their products. Global Collaboration and Innovation China’s fan filter manufacturers actively collaborate with international partners and participate in industry exhibitions and conferences. This collaboration fosters innovation and promotes the exchange of knowledge and best practices, ultimately benefiting customers with access to the latest advancements in air filtration technology. Conclusion China’s fan filter manufacturers have emerged as leaders in the field of air quality control, driven by innovation, commitment to sustainability, and dedication to quality. Their customized solutions cater to a wide array of industries, and their global reach ensures that businesses worldwide can benefit from clean and contaminant-free air environments. As these manufacturers continue to invest in advanced technologies and embrace digital transformation, they are poised to remain at the forefront of the fan filter manufacturing industry for years to come.