In the realm of electrical systems and power distribution, circuit protection plays a vital role in ensuring safety and reliability. Among the key components in this field, the Molded Case Circuit Breaker (MCCB) and its BMC parts stand out as essential elements. At the forefront of their production lies a leading manufacturer dedicated to quality, innovation, and safety.
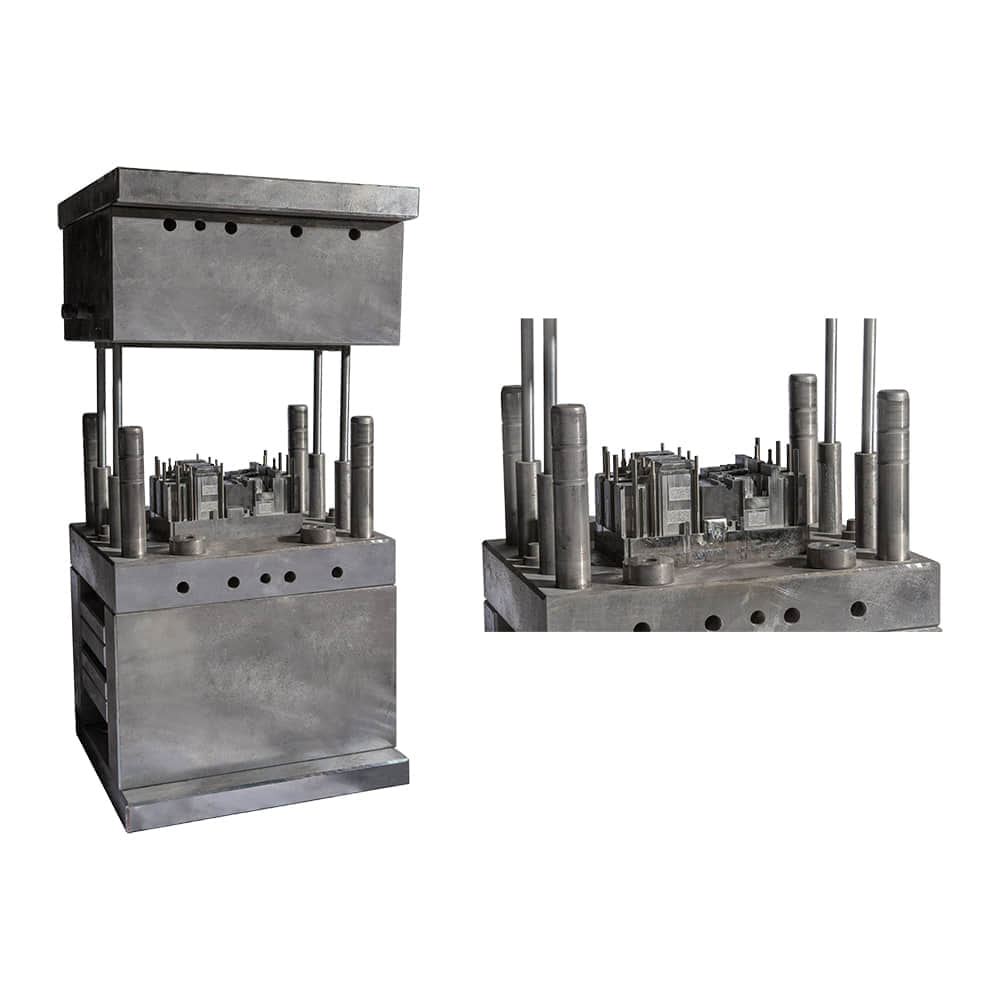
Introduction
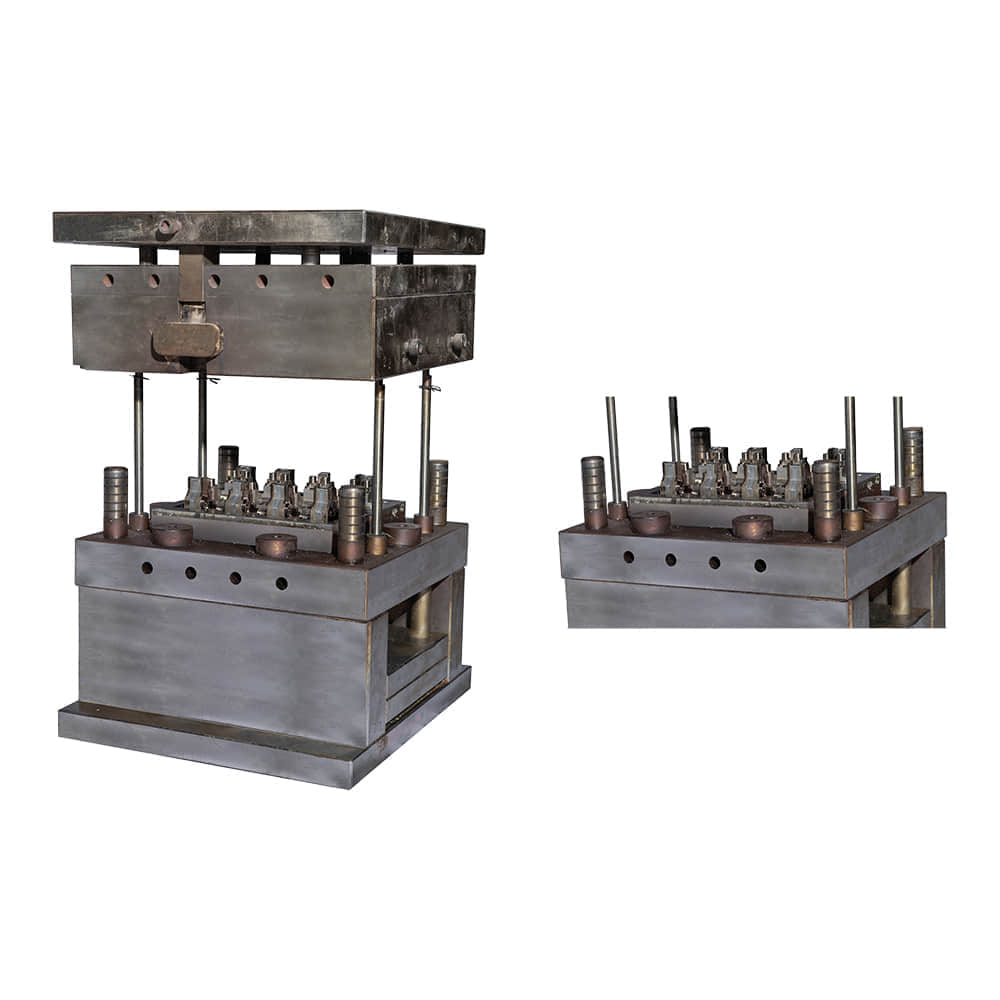
Modern industrial and residential infrastructures heavily rely on efficient power distribution networks. Central to these networks are MCCBs, which safeguard electrical circuits from overloads and short circuits. The Breaker Mechanism and Contacts (BMC) parts within the MCCBs are of paramount importance, contributing to the operational effectiveness and dependability of the circuit protection systems. The Manufacturer’s Commitment to Quality The manufacturer, renowned for its excellence in producing MCCB BMC parts, places a strong emphasis on quality control. Each phase of the manufacturing process is subjected to rigorous testing to ensure that the components meet industry standards and customer expectations. This commitment to quality guarantees that the MCCB BMC parts can withstand the demands of various applications while maintaining peak performance. Innovation as the Driving Force In a rapidly evolving technological landscape, innovation is a cornerstone of the manufacturer’s philosophy. By staying at the forefront of technological advancements, the company consistently introduces cutting-edge features and materials into their MCCB BMC parts. This dedication to innovation not only improves the performance of the components but also enhances the overall safety and efficiency of the electrical systems they protect. Safety First Approach Safety stands as the linchpin of the manufacturer’s operations. MCCB BMC parts are designed not only for optimal functionality but also with the highest safety standards in mind. The manufacturer integrates advanced protection mechanisms within their components to prevent malfunctions that could lead to electrical hazards. This unwavering commitment to safety ensures that their MCCB BMC parts provide reliable protection for people and equipment alike. Customization to Meet Diverse Needs Understanding that different industries and applications have unique requirements, the manufacturer offers a wide range of MCCB BMC parts that can be customized. Whether it’s voltage ratings, current capacities, or specific environmental conditions, the manufacturer collaborates closely with customers to deliver tailored solutions. This level of customization reflects their dedication to providing components that seamlessly integrate into diverse systems. Global Reach and Impact With a global distribution network, the manufacturer’s MCCB BMC parts have made their mark across continents. From industrial power plants to commercial buildings, their components are trusted by engineers and professionals seeking robust and reliable circuit protection solutions. This global reach showcases the universal applicability of their MCCB BMC parts and solidifies their position as an industry leader. Sustainability Initiatives Apart from technical prowess, the manufacturer is also committed to sustainability. They prioritize eco-friendly materials and production processes, ensuring that their MCCB BMC parts contribute to a greener future. This approach aligns with the increasing global focus on environmentally conscious practices and demonstrates the manufacturer’s holistic vision for responsible manufacturing. Conclusion In the intricate world of electrical circuit protection, the role of MCCB BMC parts is indisputable. This leading manufacturer’s unwavering dedication to quality, innovation, safety, and customization has elevated their MCCB BMC parts to a position of prominence in the industry. As technology continues to advance, their contributions will play an integral role in shaping the landscape of electrical systems, fostering efficiency, and ensuring safety for generations to come.
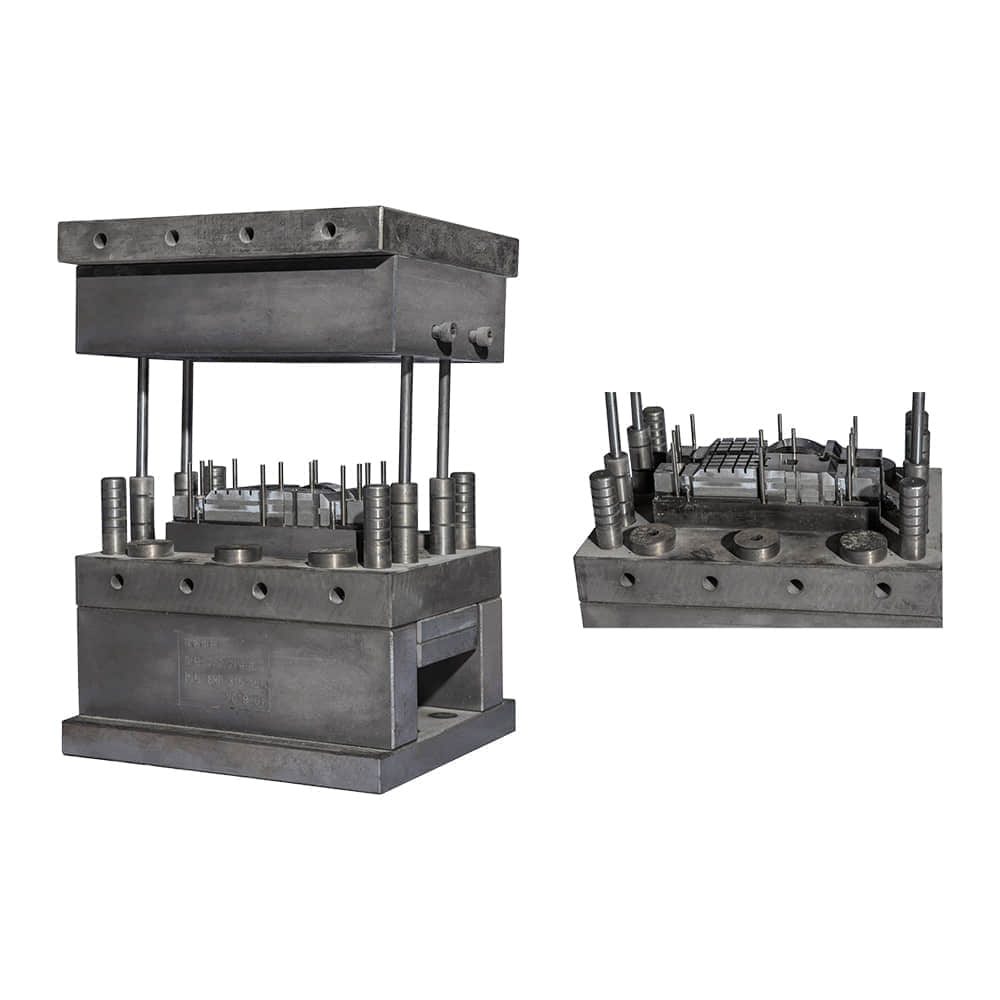