Molded case circuit breakers (MCCBs) play a pivotal role in ensuring electrical safety across various industries. These devices are designed to protect electrical circuits and equipment from overloads and short circuits, making them a crucial component of any electrical system. In this article, we will delve into the world of MCCBs and explore some of the leading brands in this industry.
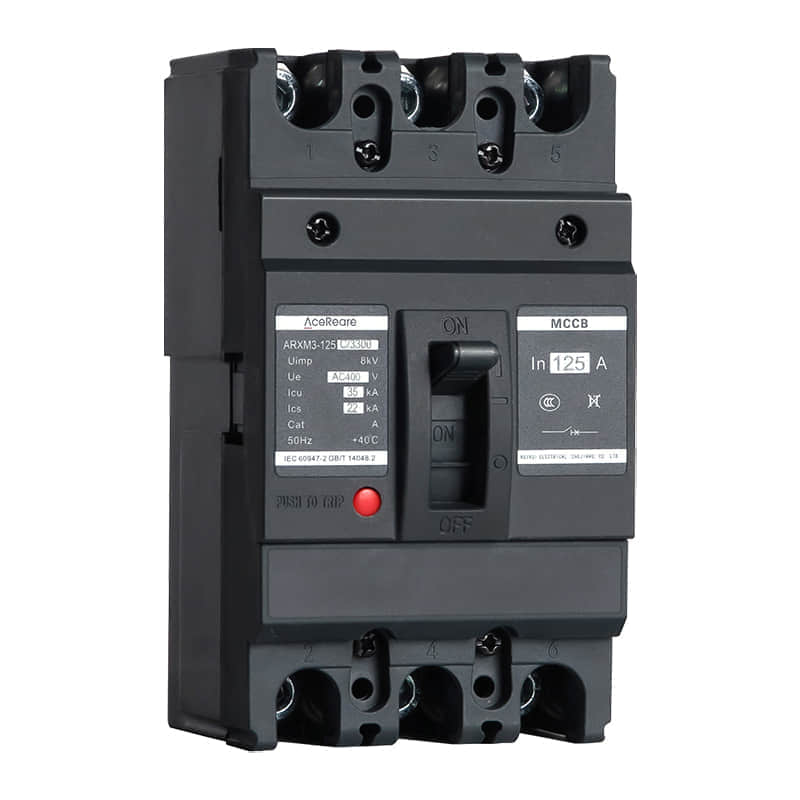
What Are Molded Case Circuit Breakers?
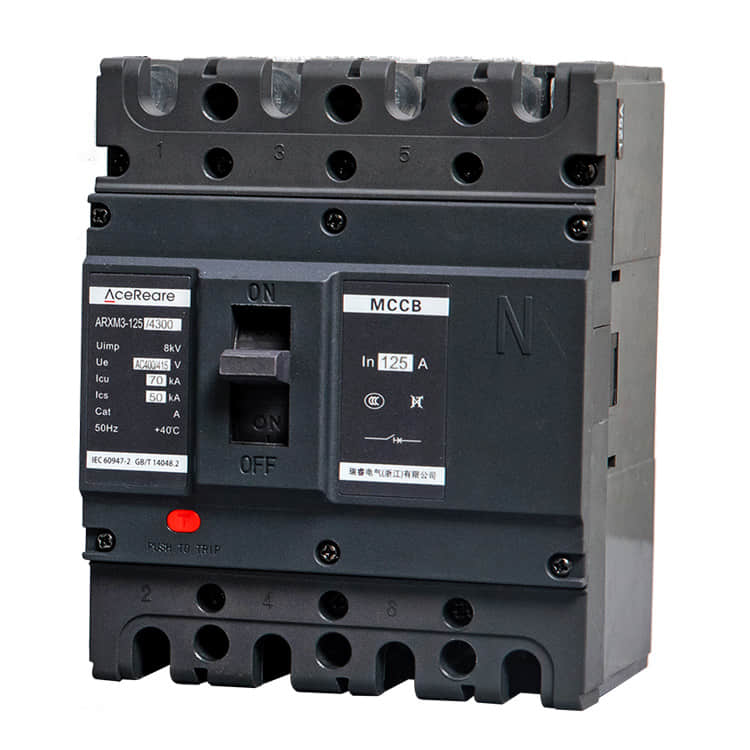
MCCBs are a type of circuit protection device commonly used in commercial, industrial, and residential applications. They are named “molded case” because their outer casing is typically made of molded plastic or other non-metallic materials. This construction not only provides insulation but also enhances the breaker’s durability. Why Are MCCBs Important? The primary function of MCCBs is to interrupt the flow of electricity when a fault occurs, preventing damage to equipment and ensuring the safety of personnel. They can handle a wide range of current levels and are available in various sizes to accommodate different applications. Now, let’s take a closer look at some of the prominent brands that manufacture MCCBs: 1. Schneider Electric: Schneider Electric is a global leader in electrical equipment and automation solutions, including MCCBs. Their MCCBs are known for their reliability and high performance. Schneider Electric offers a wide range of MCCBs to meet the diverse needs of customers across industries. 2. Siemens: Siemens is another well-established player in the electrical industry. Their MCCBs are renowned for their advanced technology and robust design. Siemens offers MCCBs with features like adjustable trip settings and communication capabilities, making them suitable for complex applications. 3. ABB: ABB is a multinational corporation known for its innovation in power and automation technologies. ABB MCCBs are designed for optimal protection and efficiency. They offer a range of MCCBs that cater to both residential and industrial requirements. 4. Eaton: Eaton is a trusted name when it comes to electrical solutions. Their MCCBs are designed to provide high-quality circuit protection. Eaton offers MCCBs that comply with various international standards, ensuring safety and reliability. 5. Square D by Schneider Electric: Square D, a subsidiary of Schneider Electric, specializes in electrical distribution and control products. Their MCCBs are known for their ease of installation and user-friendly features. Square D offers a variety of MCCBs suitable for different applications and environments. 6. Mitsubishi Electric: Mitsubishi Electric is a global leader in electrical and electronic equipment. Their MCCBs are designed to meet the demands of modern electrical systems. Mitsubishi Electric MCCBs are known for their precision and durability, making them a popular choice in the industry. 7. General Electric (GE): GE is a well-known brand in the world of electrical engineering. Their MCCBs are engineered for performance and reliability. GE offers MCCBs with advanced protection features and compatibility with smart systems for enhanced control. Conclusion: Molded case circuit breakers are essential components of electrical systems, ensuring safety and protecting valuable equipment. The brands mentioned above are leaders in the MCCB industry, known for their quality, reliability, and innovation. When selecting an MCCB for your specific application, it’s essential to consider factors such as current rating, trip characteristics, and communication capabilities to ensure optimal protection and performance. By choosing a reputable brand, you can trust that your electrical system will be in safe hands.
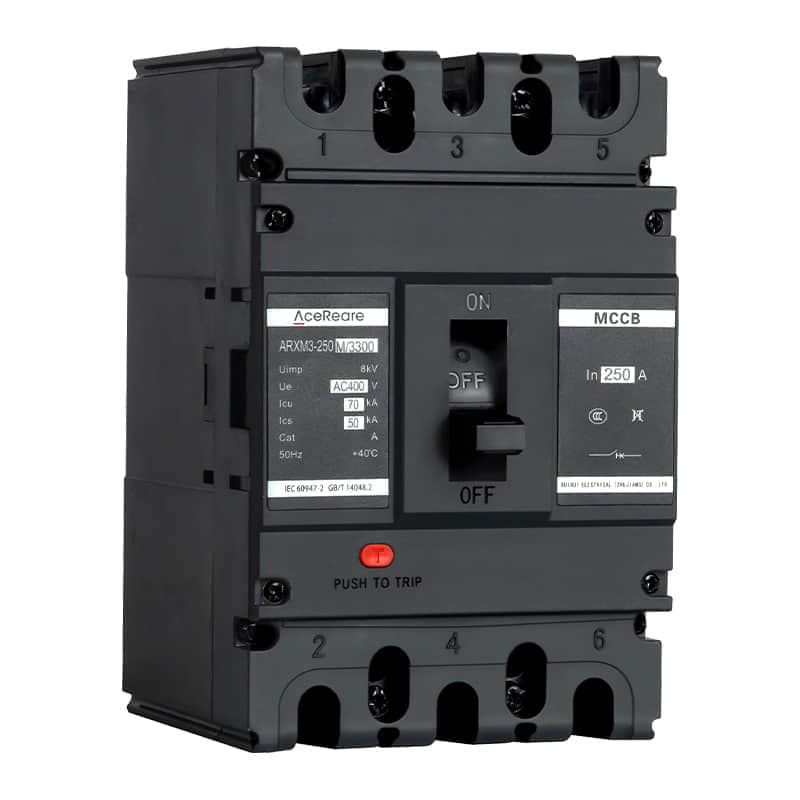