In the realm of modern manufacturing, thermoplastic injection molds have emerged as indispensable tools for producing a wide array of products with precision and efficiency. These molds have revolutionized various industries, from automotive to electronics, by enabling the creation of intricate and high-quality components. This article delves into the key aspects and recent advancements in thermoplastic injection molds.
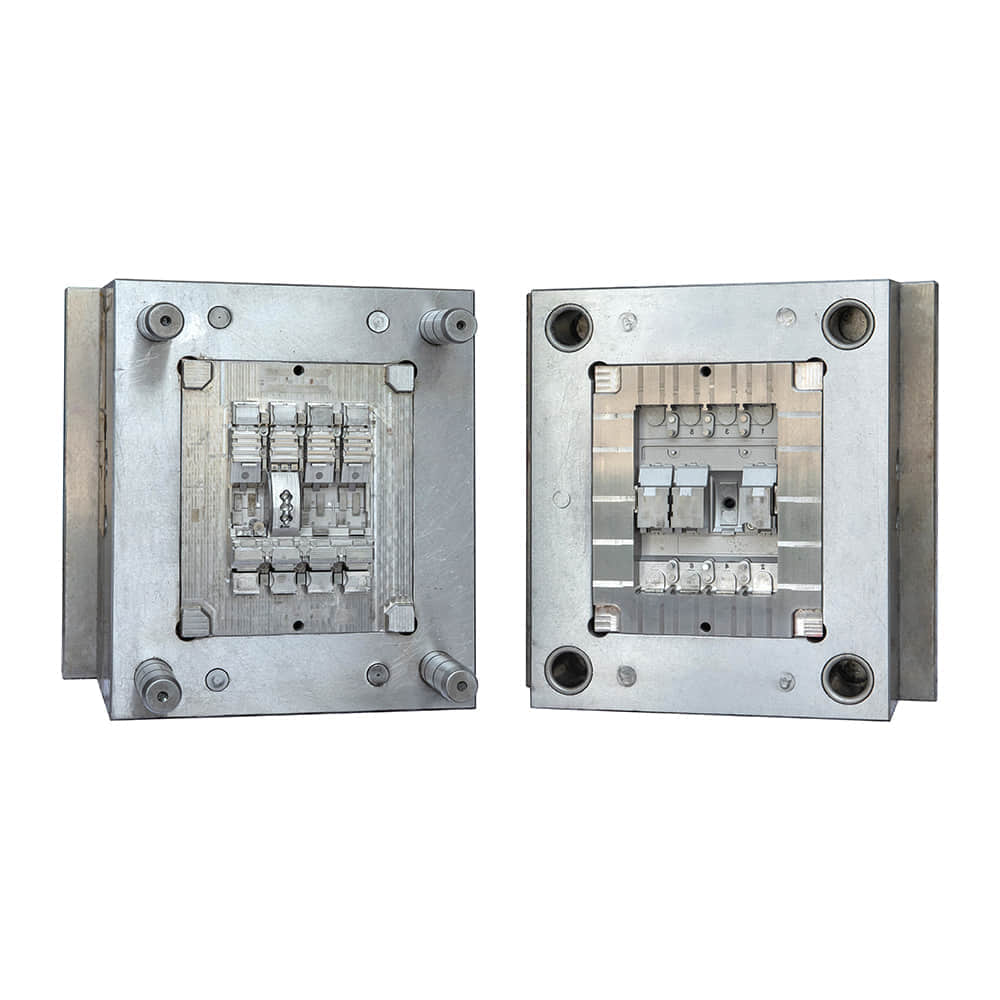
The Evolution of Thermoplastic Injection Molds: A Brief OverviewThermoplastic injection molds are the cornerstone of injection molding, a process that involves injecting molten thermoplastic materials into a mold cavity to create a desired shape upon cooling and solidification. This technique offers unparalleled versatility, allowing manufacturers to produce complex geometries, fine details, and consistent quality on a large scale. Over the years, continuous research and innovation have led to remarkable advancements in the design, materials, and manufacturing processes associated with thermoplastic injection molds.
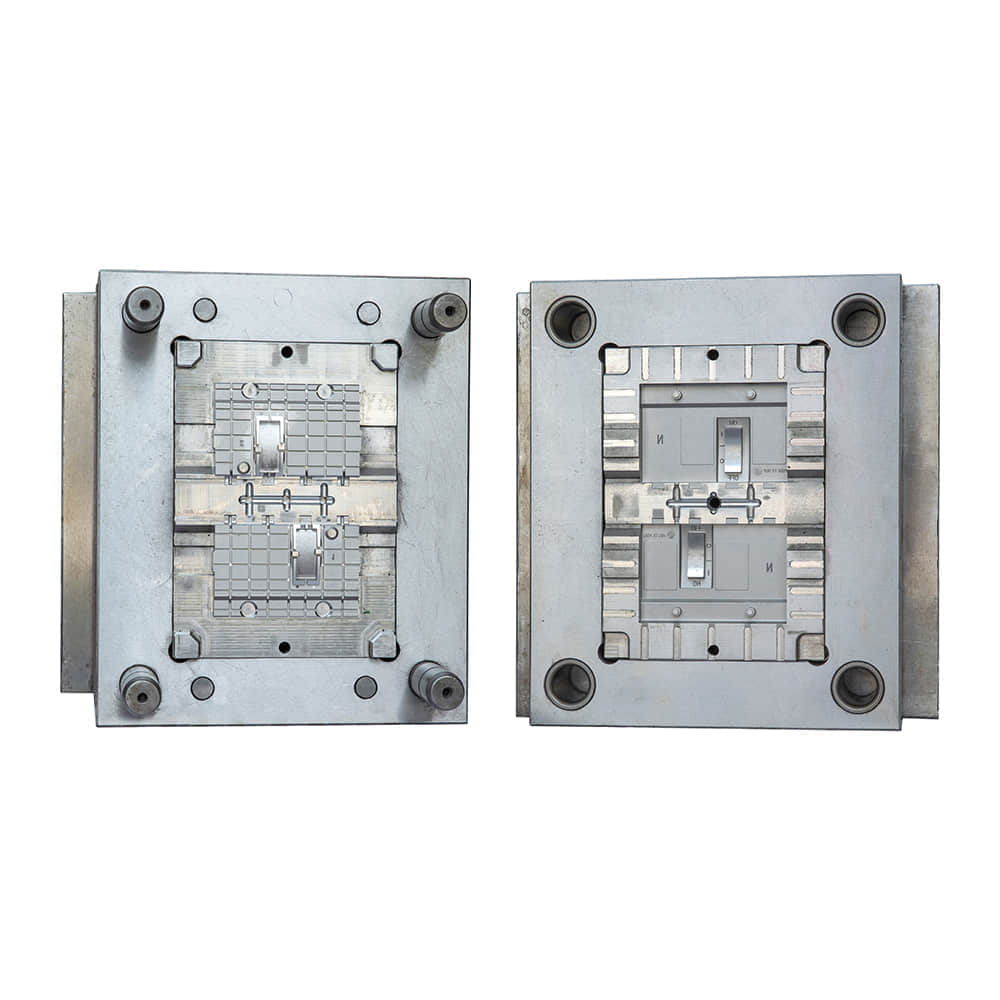
Precision Engineering and DesignOne of the critical factors contributing to the success of thermoplastic injection molds is precision engineering. Computer-aided design (CAD) software and simulation tools have revolutionized mold design, enabling engineers to create intricate mold structures and optimize them for maximum efficiency. With the aid of these tools, factors such as mold flow, cooling channels, and ejection mechanisms can be meticulously analyzed and refined before the mold even enters the production phase. This not only reduces development time but also enhances the overall quality of the final product. Innovations in Mold MaterialsAdvancements in material science have paved the way for the development of new mold materials that offer enhanced performance and durability. Traditional metals like steel remain popular choices due to their excellent heat resistance and longevity. However, newer materials, such as beryllium-copper alloys, offer superior thermal conductivity, allowing for more efficient cooling during the molding process. Moreover, the rise of high-performance polymers has introduced non-metallic options that are corrosion-resistant, lightweight, and conducive to molding intricate shapes. Additive Manufacturing and PrototypingAdditive manufacturing, or 3D printing, has also made its mark on the world of thermoplastic injection molds. This technology allows for rapid and cost-effective prototyping of mold components, enabling engineers to iterate designs and test functionality before committing to traditional machining methods. The ability to produce complex geometries with additive manufacturing has led to innovative mold designs that were previously unattainable, further pushing the boundaries of what is achievable in injection molding. Industry 4.0 IntegrationThe integration of Industry 4.0 concepts into manufacturing processes has not bypassed thermoplastic injection molding. Smart molds embedded with sensors and connectivity features are now capable of providing real-time data on parameters such as temperature, pressure, and cycle times. This data-driven approach enables manufacturers to monitor and optimize the molding process, leading to improved product consistency, reduced downtime, and predictive maintenance. Sustainability and Circular EconomyIn recent years, sustainability concerns have driven the development of environmentally friendly practices in various industries. Thermoplastic injection molding is no exception. Manufacturers are exploring ways to incorporate recycled thermoplastics into their processes, reducing waste and minimizing the environmental impact. Additionally, advancements in mold design and process optimization have led to reduced energy consumption and material wastage, aligning with the principles of the circular economy. ConclusionThermoplastic injection molds have come a long way since their inception, evolving through precision engineering, material advancements, additive manufacturing, and digital integration. These molds have enabled the production of intricate and high-quality components across diverse industries, contributing to technological progress and efficiency. As we continue to explore new horizons in manufacturing, it’s clear that thermoplastic injection molds will remain at the forefront of innovation, driving the creation of products that shape our modern world.
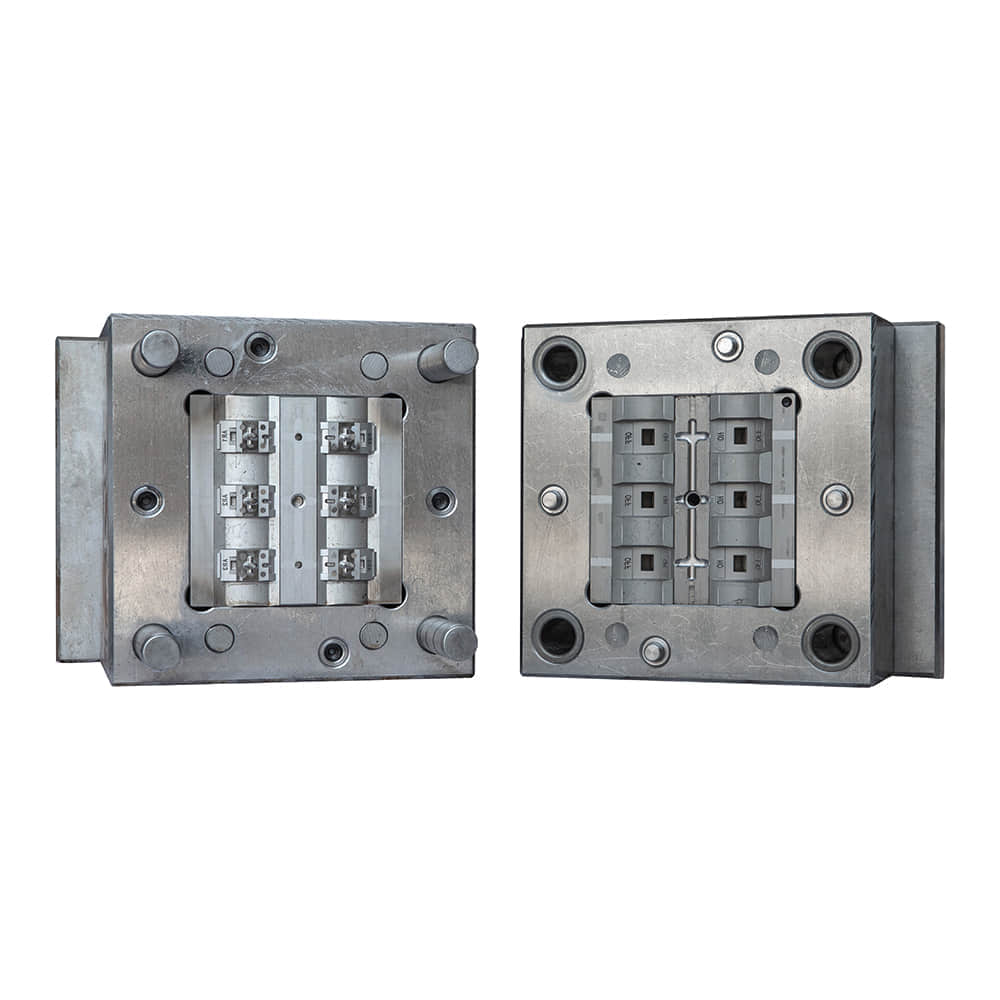