Molded Case Circuit Breakers (MCCBs) play a pivotal role in electrical systems, providing vital protection against overloads and short circuits. Behind these critical devices are manufacturers that continually strive for innovation and excellence. In this article, we delve into the world of MCCB manufacturing, exploring the key aspects that make these companies stand out in the industry.
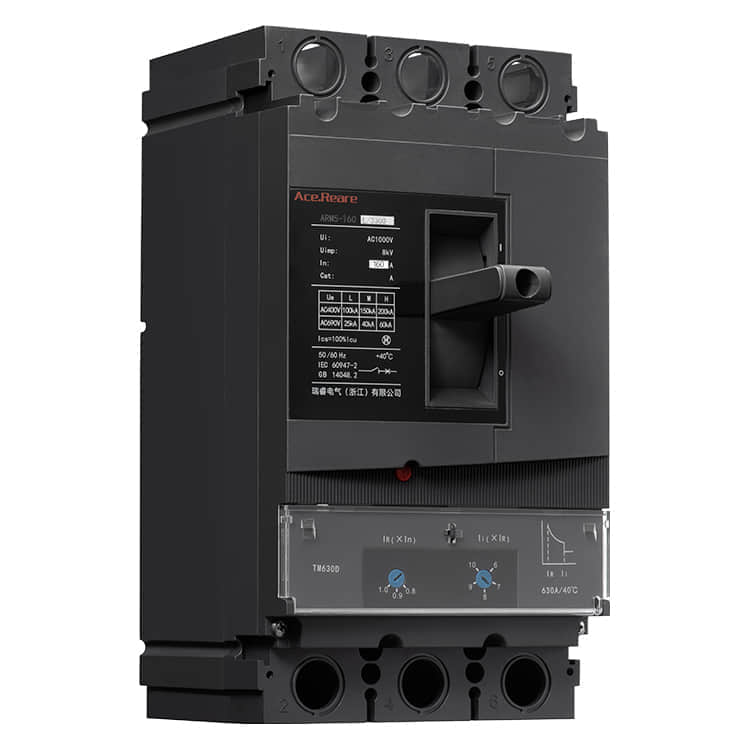
1. Cutting-Edge Technology Integration
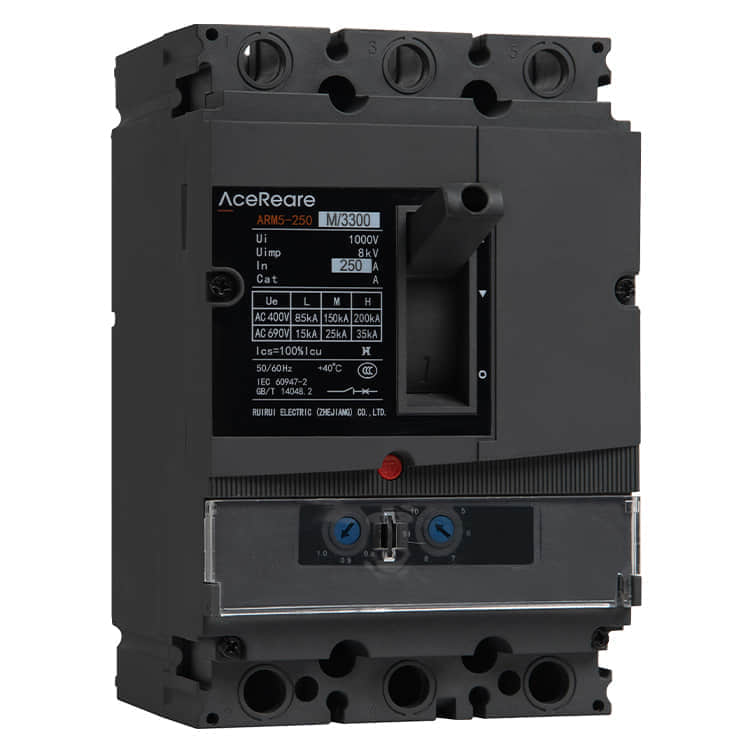
Leading MCCB manufacturers are distinguished by their unwavering commitment to incorporating cutting-edge technology into their products. This includes the use of advanced materials, such as high-impact, flame-resistant thermoplastics, to enhance MCCBs’ durability and safety. Moreover, the integration of intelligent trip units and digital communication capabilities has transformed MCCBs into smart devices capable of providing real-time data on electrical conditions. These technological advancements ensure that MCCBs are at the forefront of electrical safety and performance. 2. Stringent Quality Control Quality control is non-negotiable in MCCB manufacturing. Renowned manufacturers subject their products to rigorous testing processes, adhering to international standards and certifications. This ensures that MCCBs operate flawlessly under various conditions, safeguarding both people and equipment from electrical faults. In addition to functional testing, manufacturers implement strict quality checks on components, guaranteeing reliability throughout the MCCB’s lifespan. 3. Customization for Diverse Applications Different industries and applications demand MCCBs with unique specifications. Leading manufacturers understand this and offer a wide range of MCCBs tailored to diverse needs. Whether it’s for industrial machinery, data centers, or residential installations, these companies provide MCCBs with varying current ratings, trip curves, and accessories to accommodate specific requirements. This level of customization enhances the versatility and adaptability of MCCBs across various sectors. 4. Sustainability Initiatives In today’s environmentally conscious world, MCCB manufacturers are increasingly adopting sustainable practices. They aim to reduce their carbon footprint by employing eco-friendly materials and production processes. Moreover, some manufacturers prioritize energy-efficient MCCB designs to help end-users lower their energy consumption and reduce greenhouse gas emissions. 5. Comprehensive Technical Support Exceptional customer support is another hallmark of top MCCB manufacturers. They offer comprehensive technical assistance to customers, helping them select the right MCCB for their applications and providing guidance on installation and maintenance. This commitment to customer satisfaction ensures that MCCBs perform optimally throughout their service life. 6. Global Reach and Local Presence To cater to a global market, leading MCCB manufacturers establish a strong global presence. They have a network of distributors, partners, and service centers around the world, ensuring that their products are readily available and supported in various regions. Simultaneously, they often maintain local manufacturing facilities to meet the specific needs of regional markets while adhering to local regulations. 7. Continuous Research and Development Staying ahead in the MCCB industry requires continuous research and development efforts. Renowned manufacturers invest heavily in R&D to create next-generation MCCBs that are more efficient, reliable, and technologically advanced. By anticipating future electrical system requirements, these manufacturers remain at the forefront of innovation. Conclusion Manufacturers of Molded Case Circuit Breakers are vital contributors to electrical safety and reliability. Their commitment to technological innovation, quality control, customization, sustainability, customer support, global presence, and R&D distinguishes them as leaders in the industry. As the world’s electrical systems evolve, MCCB manufacturers play a pivotal role in ensuring that these systems remain safe and efficient.
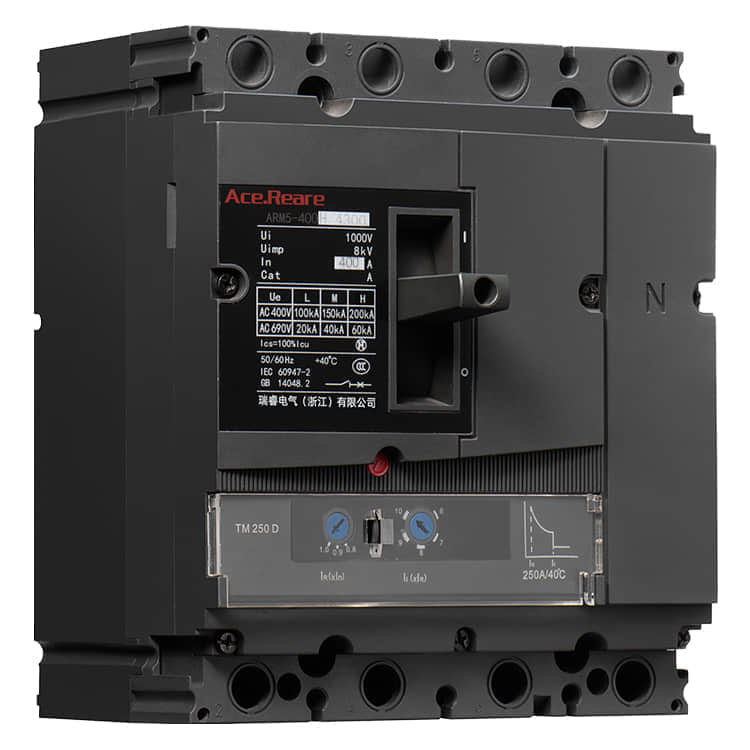