Metal stamping parts are a critical component of modern manufacturing processes, playing an integral role in various industries, from automotive and aerospace to electronics and appliances. In this article, we will delve into the fascinating world of metal stamping parts, exploring their significance, applications, and the intricate processes involved in their production.
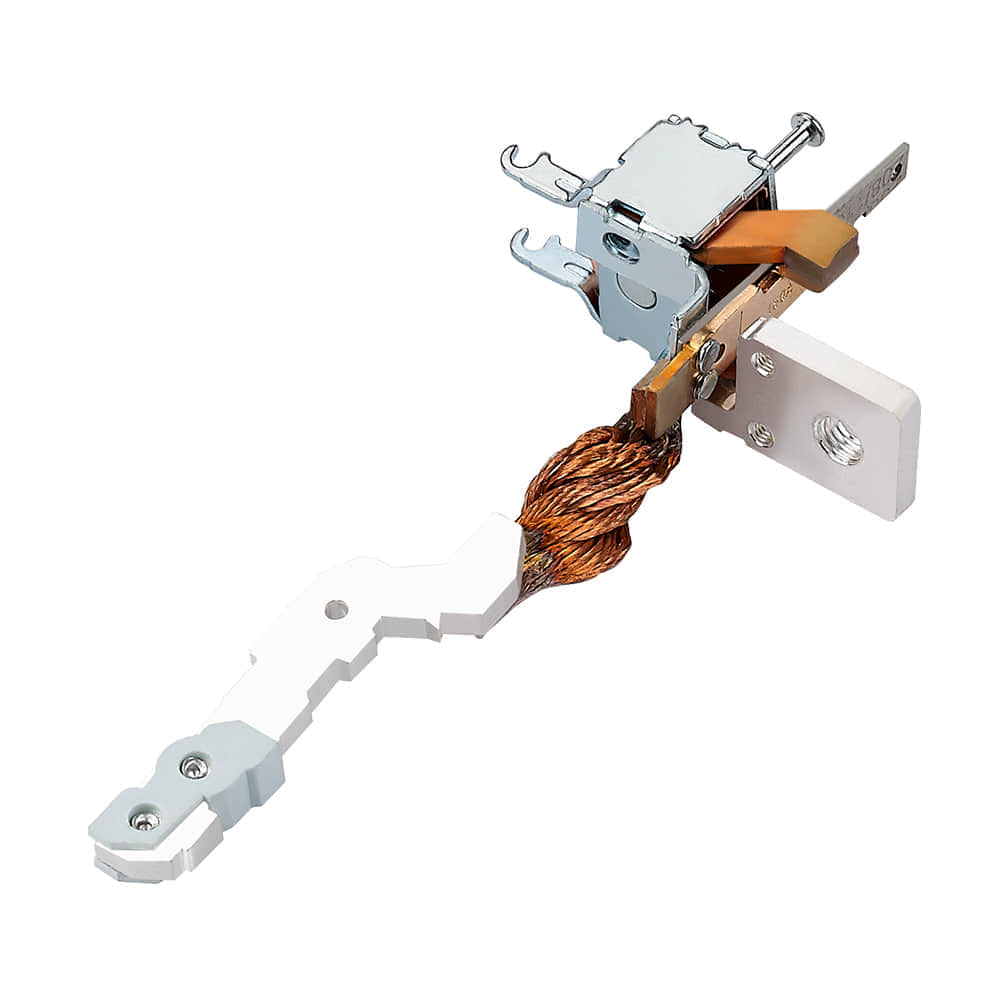
The Significance of Metal Stamping Parts
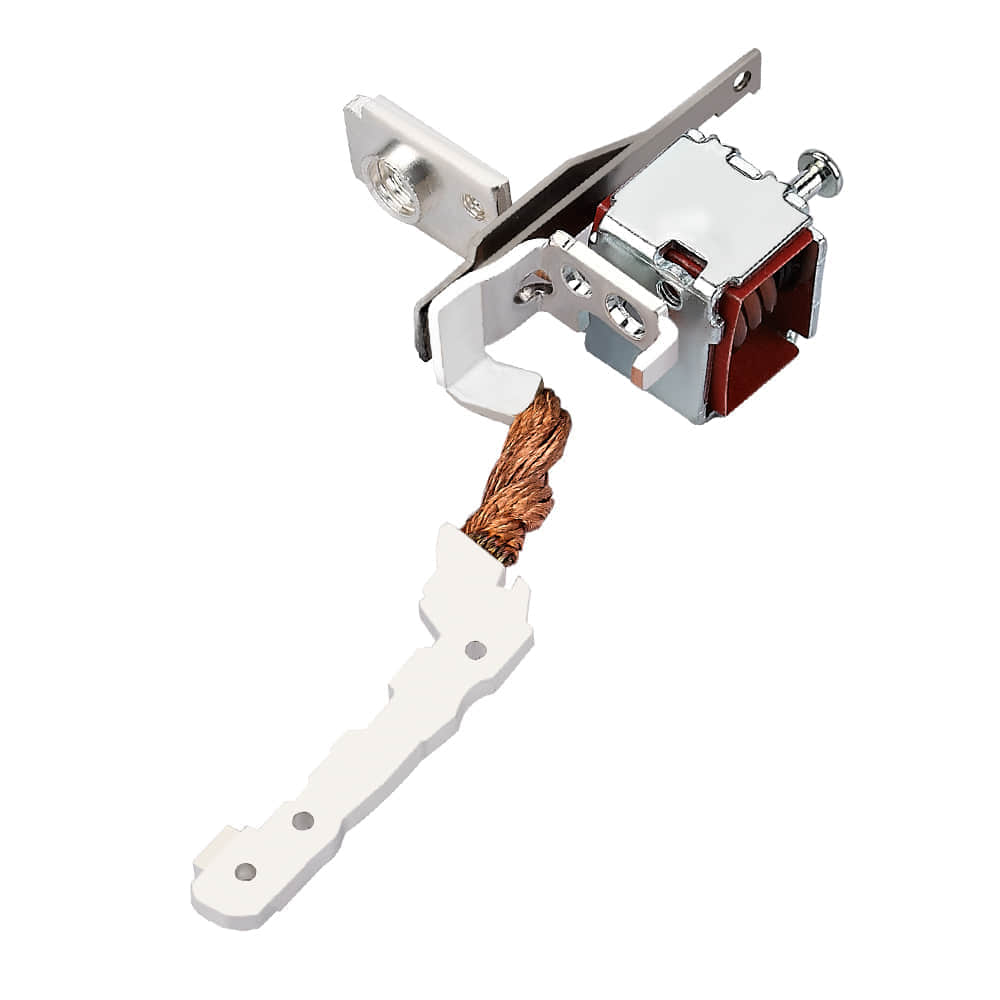
Metal stamping parts are essential in manufacturing due to their versatility and cost-effectiveness. These parts are typically made from sheet metal, which is easy to shape and manipulate. This makes them ideal for producing intricate and complex components that are used in a wide range of products. One of the primary advantages of metal stamping parts is their ability to be mass-produced quickly and accurately. This efficiency helps manufacturers meet high production demands while maintaining consistent quality. Additionally, metal stamping allows for the creation of lightweight yet durable components, contributing to the overall performance and efficiency of various products. Applications Across Industries Metal stamping parts find applications across a multitude of industries, making them an indispensable part of the manufacturing landscape. Automotive Industry:Metal stamping is extensively used in the automotive sector to create body panels, chassis components, and various other parts. These parts are not only crucial for vehicle aesthetics but also for safety and structural integrity. Aerospace Industry:In aerospace, precision and reliability are paramount. Metal stamping parts are used to manufacture components for aircraft, including structural parts, brackets, and connectors. Electronics and Appliances:The electronics and appliance industries rely on metal stamping for producing casings, connectors, and other intricate parts. The precision and repeatability of metal stamping are essential for ensuring product functionality. Medical Devices:In the medical field, metal stamping is used to manufacture surgical instruments, diagnostic equipment, and implantable devices. The high level of precision required in this industry makes metal stamping an ideal choice. Construction:Metal stamping parts are also found in construction materials and equipment. They are used to produce various structural components, fasteners, and fixtures. The Metal Stamping Process The process of creating metal stamping parts involves several precise steps: Design and Prototyping:The process begins with the design of the part using computer-aided design (CAD) software. Prototypes are often created and tested to ensure the part’s functionality and manufacturability. Material Selection:The appropriate sheet metal material is chosen based on factors such as strength, corrosion resistance, and cost. Blanking:In this step, a flat sheet of metal is cut into the desired shape. This is often done with the help of a die and a press machine. Forming:The blanked metal is then formed into its final shape using a combination of dies, punches, and press machines. This step can include bending, deep drawing, and other processes to achieve the desired geometry. Finishing:After forming, the part may undergo additional processes such as welding, coating, or plating to enhance its properties or appearance. Quality Control:Strict quality control measures are employed to ensure that each stamped part meets the required specifications. This may involve dimensional inspections, material testing, and visual checks. Assembly:In some cases, multiple metal stamping parts are assembled to create a more complex component or product. Conclusion Metal stamping parts are a fundamental element of modern manufacturing, with diverse applications across various industries. Their cost-effectiveness, precision, and efficiency make them indispensable in producing high-quality components for countless products. As technology continues to advance, the world of metal stamping will undoubtedly evolve, driving innovation and shaping the future of manufacturing.
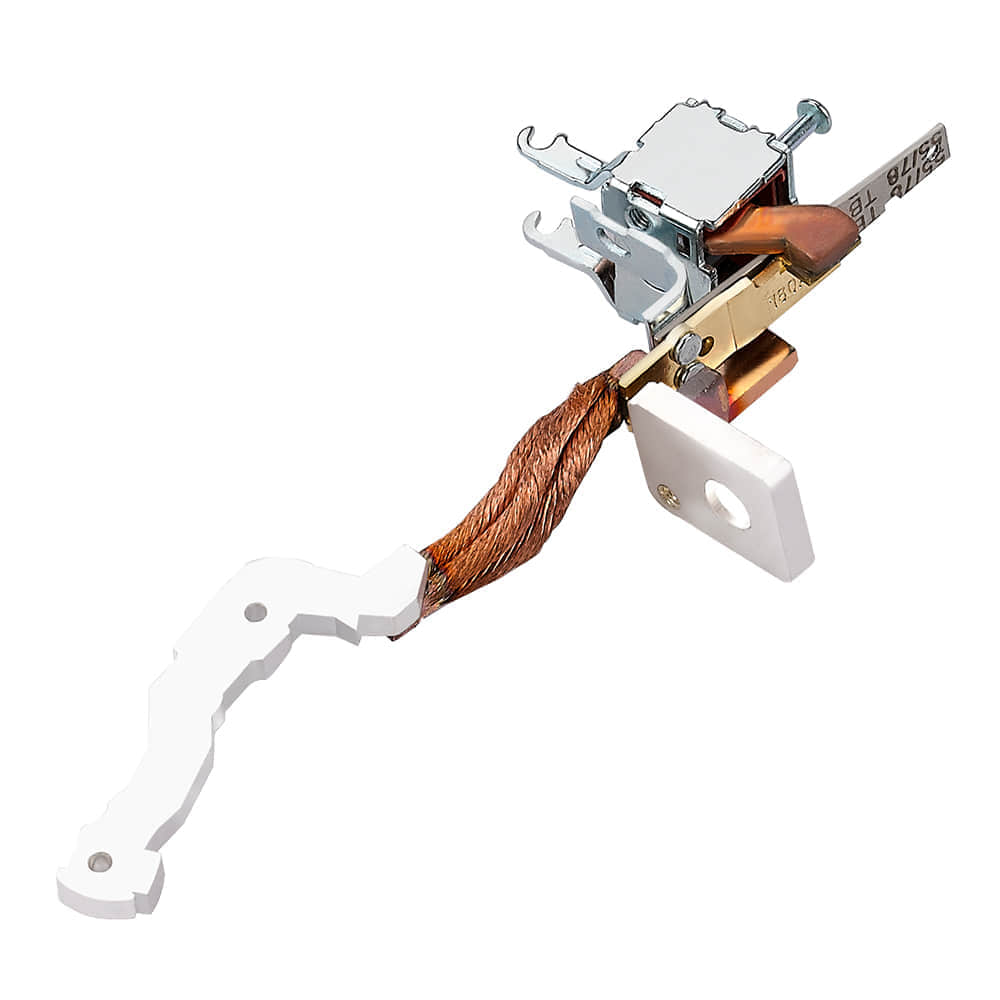