In the dynamic world of electrical engineering, safety and reliability are paramount. When it comes to ensuring the protection of electrical circuits and equipment, China Molded Case Circuit Breaker OEM Manufacturers stand out as leaders in the industry. With their commitment to innovation, quality, and customer satisfaction, these manufacturers have earned a global reputation for excellence.
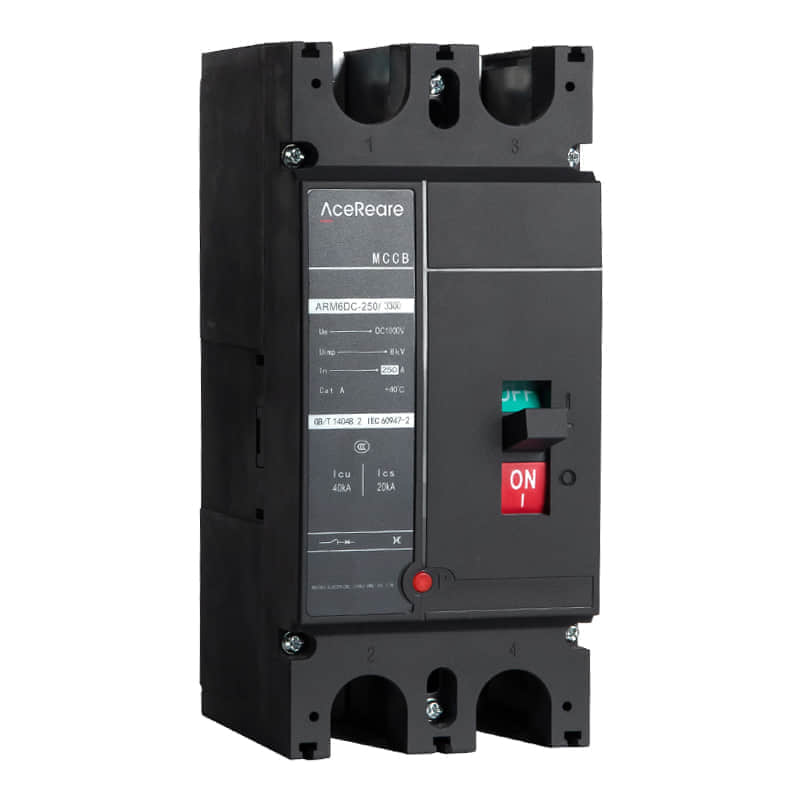
A Legacy of Innovation
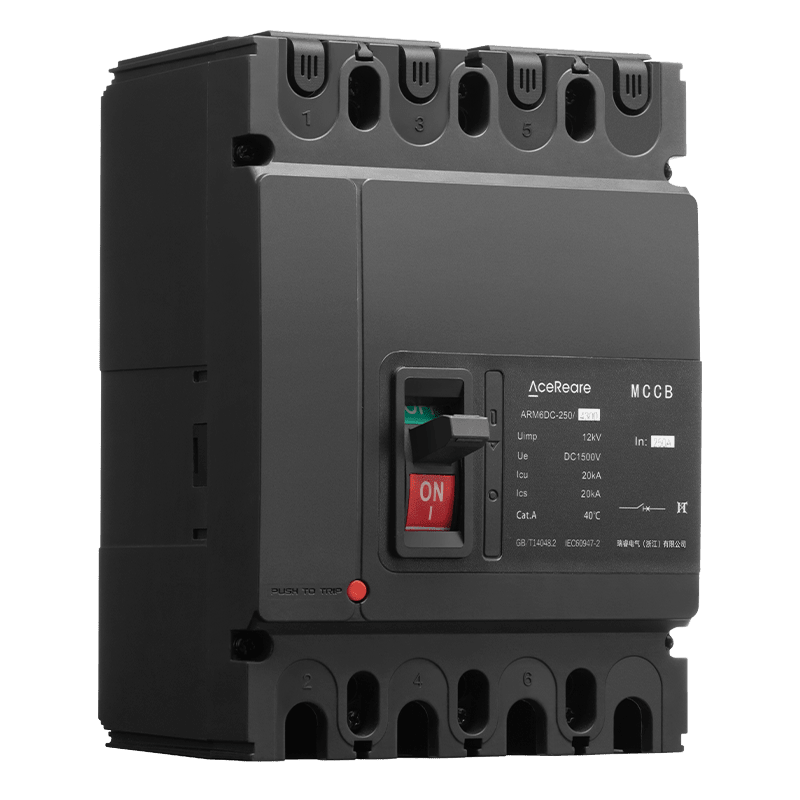
China Molded Case Circuit Breaker OEM Manufacturers have a rich history of innovation that dates back decades. They have consistently pushed the boundaries of technology, designing circuit breakers that are not only reliable but also adaptable to a wide range of applications. These circuit breakers are crucial components in any electrical system, serving as the first line of defense against overcurrents and short circuits. Quality as a Priority One of the key reasons why China Molded Case Circuit Breaker OEM Manufacturers excel is their unwavering commitment to quality. They adhere to stringent quality control processes throughout the manufacturing journey, from the selection of raw materials to the final product testing. This dedication to quality ensures that their circuit breakers meet or exceed international standards, providing peace of mind to customers worldwide. Versatility in Product Range China Molded Case Circuit Breaker OEM Manufacturers understand that every electrical system is unique, with specific requirements and challenges. To address this, they offer a diverse range of circuit breakers that cater to various industries and applications. Whether it’s for industrial, commercial, or residential use, these manufacturers provide solutions tailored to the needs of their customers. Customization Options Flexibility is another hallmark of China Molded Case Circuit Breaker OEM Manufacturers. They understand that one size doesn’t fit all, and they are well-equipped to customize circuit breakers to meet specific project requirements. This level of customization ensures that customers receive the perfect solution for their unique electrical protection needs. Commitment to Sustainability In today’s environmentally conscious world, China Molded Case Circuit Breaker OEM Manufacturers are also at the forefront of sustainability efforts. They integrate eco-friendly materials and processes into their manufacturing, reducing their carbon footprint. This commitment to sustainability not only benefits the environment but also aligns with the global shift towards green technologies. Global Reach and Local Support While China Molded Case Circuit Breaker OEM Manufacturers have a global presence, they also prioritize local customer support. Their extensive network of distributors and service centers ensures that customers receive timely assistance, whether it’s for product inquiries, technical support, or maintenance. Embracing Digitalization In an era of digital transformation, China Molded Case Circuit Breaker OEM Manufacturers have embraced the power of technology. They offer smart circuit breakers equipped with advanced monitoring and control features. These intelligent circuit breakers provide real-time data, enabling predictive maintenance and enhancing overall system reliability. Compliance and Certification China Molded Case Circuit Breaker OEM Manufacturers take compliance and certification seriously. Their products meet a host of international standards, including IEC, UL, and CE, ensuring that they are accepted and trusted worldwide. These certifications underline the manufacturers’ commitment to safety and reliability. Continual Improvement Continuous improvement is a core philosophy of China Molded Case Circuit Breaker OEM Manufacturers. They invest in research and development to stay ahead of industry trends and evolving customer needs. This commitment to innovation ensures that their circuit breakers remain at the forefront of electrical protection technology. In conclusion, China Molded Case Circuit Breaker OEM Manufacturers have established themselves as industry leaders through a combination of innovation, quality, versatility, and customer-centricity. Their unwavering commitment to excellence in electrical protection has made them a trusted choice for customers worldwide. Whether in terms of safety, reliability, or sustainability, these manufacturers continue to set the standard for the industry.
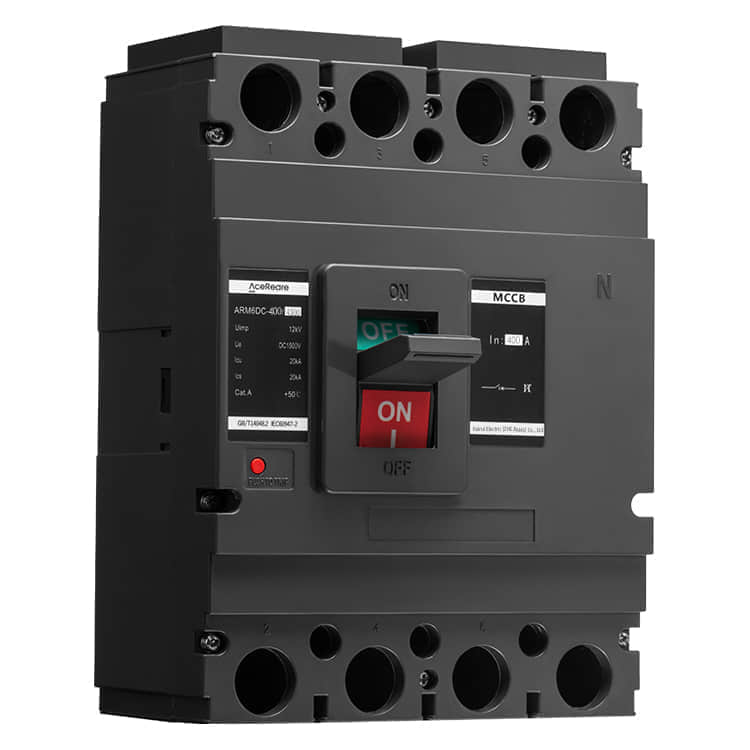